PVD (Physical Vapor Deposition) coating is a versatile and advanced surface treatment technology used across a wide range of industries. It enhances the durability, performance, and aesthetic appeal of products while offering environmental benefits compared to traditional methods like chrome plating. PVD coatings are applied to various materials, including metals, ceramics, and plastics, to improve wear resistance, corrosion resistance, and hardness. Common applications include automotive parts, surgical tools, decorative hardware, medical devices, firearms, and consumer electronics. Additionally, PVD coatings are used in industries such as jewelry, marine, and sporting goods to provide long-lasting finishes and functional improvements.
Key Points Explained:
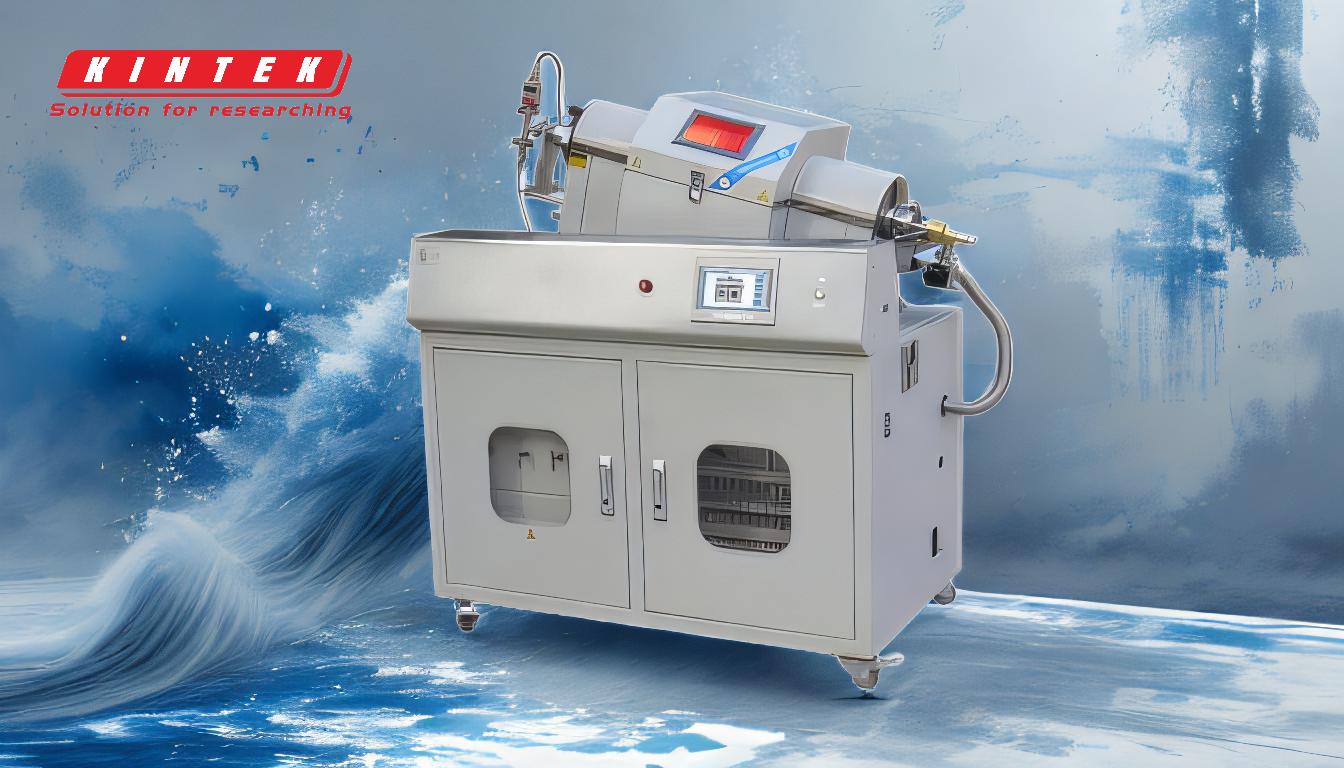
-
Durability and Lifespan Enhancement:
- PVD coatings are widely used to extend the life of products by providing superior wear resistance and hardness. For example, car parts like wheels and pistons, as well as surgical tools and drill bits, benefit from PVD coatings, which can increase their lifespan by up to ten times, sometimes lasting more than 25 years.
- This makes PVD coating a cost-effective solution for industries requiring long-lasting performance.
-
Environmental Benefits:
- PVD coating is considered a greener alternative to traditional chrome plating. It does not produce toxic substances, making it environmentally friendly. This aligns with modern sustainability goals and regulations in manufacturing.
-
Decorative Applications:
- PVD technology is extensively used in decorative products, including jewelry, door and window hardware, kitchen and bathroom fixtures, lamps, and handicrafts. It offers a variety of colors and finishes, enhancing the aesthetic appeal of these items while also providing scratch and wear resistance.
-
Industrial and Consumer Applications:
- In industries like firearms, PVD coatings enhance durability and performance, making components more resistant to wear and corrosion.
- In home products, PVD coatings are used to create decorative finishes and improve the longevity of kitchen and bath fixtures, such as faucets, nozzles, and showerheads.
-
Medical and Dental Uses:
- PVD coatings are applied to medical devices to add chemical resistance, wear resistance, and hardness without compromising performance. Applications include surgical instruments, orthopedics, and dentistry, where durability and hygiene are critical.
-
Consumer Electronics and Optics:
- Thermal Evaporation PVD is used in applications such as solar cells, cosmetics, computers, cell phones, and optical devices. It provides functional and decorative benefits, such as improving the durability of electronic components and enhancing the appearance of consumer goods.
-
Versatility Across Industries:
- PVD coatings are used in a wide range of industries, including automotive, marine, sporting goods, and musical instruments. For example, golf clubs, eyeglass frames, and marine hardware benefit from the enhanced durability and aesthetic qualities of PVD coatings.
By offering a combination of functional and decorative benefits, PVD coating has become an essential technology in modern manufacturing, catering to diverse industries and applications. Its ability to improve product performance while being environmentally friendly makes it a preferred choice for many manufacturers.
Summary Table:
Application | Benefits |
---|---|
Automotive Parts | Increased wear resistance, extended lifespan (up to 25 years) |
Surgical Tools | Enhanced durability, chemical resistance, and hygiene |
Decorative Hardware | Aesthetic appeal, scratch resistance, and long-lasting finishes |
Medical Devices | Improved hardness, wear resistance, and performance |
Consumer Electronics | Durability and decorative enhancements for phones, computers, and optics |
Firearms & Sporting Goods | Superior corrosion and wear resistance for high-performance applications |
Jewelry & Marine Hardware | Scratch resistance, aesthetic finishes, and durability in harsh conditions |
Interested in how PVD coating can benefit your industry? Contact us today to learn more!