PVD (Physical Vapor Deposition) coating is a versatile and advanced surface treatment technology used across a wide range of industries and applications. It is primarily employed to enhance the durability, performance, and aesthetic appeal of various products and components. PVD coatings are known for their ability to improve hardness, wear resistance, corrosion resistance, and oxidation resistance, making them ideal for demanding environments. They are applied to substrates ranging from metals and polymers to ceramics, and their use spans industries such as aerospace, automotive, medical, consumer goods, and electronics. PVD coatings are also environmentally friendly, offering a sustainable alternative to traditional plating methods.
Key Points Explained:
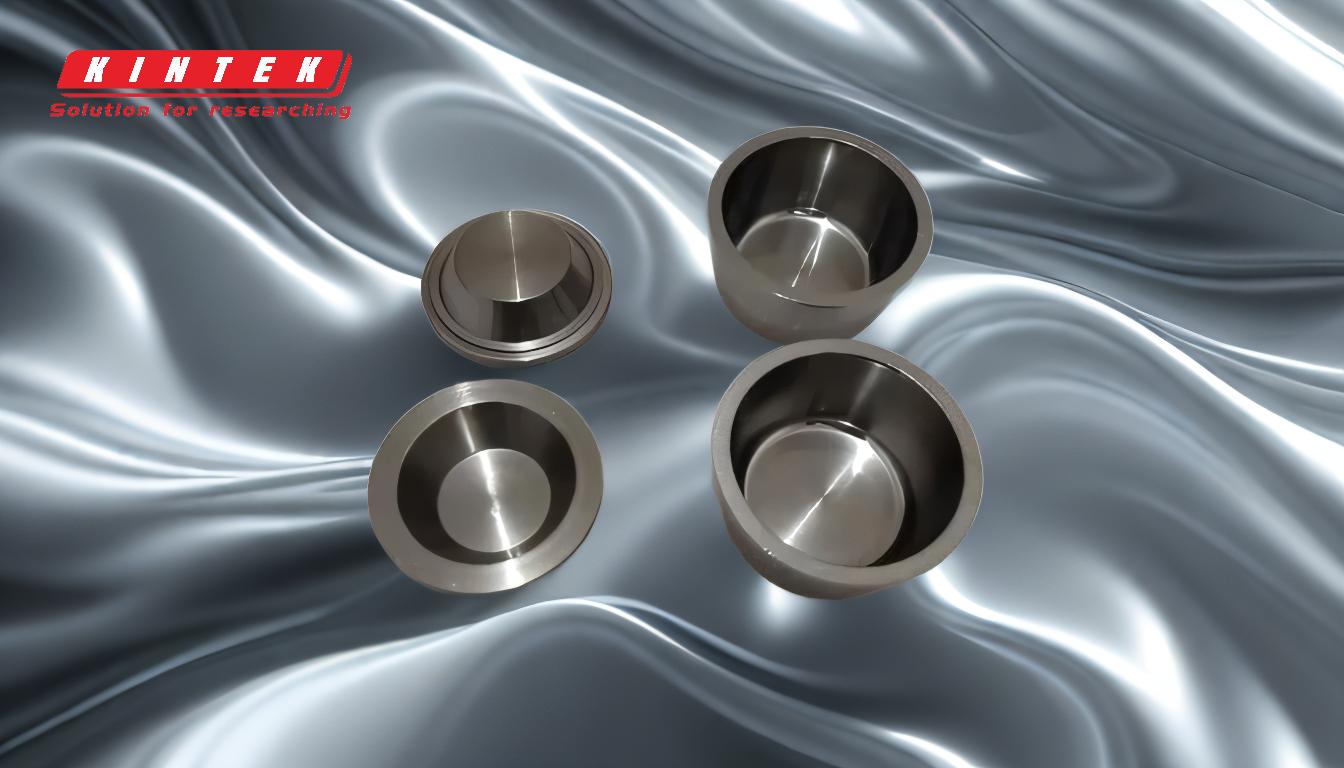
-
Aerospace and Automotive Industries
- PVD coatings are extensively used in aerospace and automotive applications due to their ability to improve hardness, wear resistance, and oxidation resistance.
- In aerospace, they are applied to components like turbine blades, engine parts, and structural elements to enhance performance and longevity.
- In the automotive sector, PVD coatings are used on parts such as pistons, wheels, and engine components to reduce friction, improve durability, and resist corrosion.
- These coatings also contribute to fuel efficiency and reduced maintenance costs by extending the lifespan of critical components.
-
Medical and Surgical Applications
- PVD coatings are widely used in the medical field for surgical tools, implants, and biomedical instruments.
- For example, titanium coatings are applied to medical implants to improve biocompatibility and resistance to wear and corrosion.
- Surgical tools coated with PVD layers benefit from enhanced hardness and reduced friction, ensuring precision and longevity.
- These coatings also help in reducing the risk of contamination and improving sterilization processes.
-
Consumer Goods and Decorative Applications
- PVD coatings are popular in consumer goods for both functional and aesthetic purposes.
- They are used in kitchen and bath fixtures (faucets, showerheads, nozzles), door hardware, jewelry, eyeglass frames, and writing instruments.
- The coatings provide a durable, scratch-resistant, and visually appealing finish, often mimicking precious metals like gold, silver, or bronze.
- In sporting goods, PVD coatings are applied to golf clubs, firearms, and other equipment to improve performance and durability.
-
Electronics and Optics
- PVD coatings play a critical role in the electronics and optics industries.
- They are used to deposit thin films for semiconductors, photovoltaic cells, and optical devices, enhancing electrical conductivity and optical performance.
- Gold and silver thin films are applied to replace traditional plating methods in electronics, offering better performance and environmental benefits.
- Anti-reflection coatings on lenses and mirrors are another common application, improving clarity and reducing glare.
-
Industrial Tools and Machinery
- PVD coatings are applied to cutting tools, dies, molds, and other industrial equipment to improve hardness and wear resistance.
- These coatings extend the lifespan of tools, reduce downtime, and enhance productivity in material processing industries.
- Ceramic coatings, in particular, are used for their chemical resistance and ability to withstand high temperatures.
-
Marine and Architectural Applications
- In marine environments, PVD coatings are used on hardware and components to resist corrosion caused by saltwater exposure.
- Architectural applications include coatings on lighting fixtures, bathroom accessories, and home hardware, providing durability and aesthetic appeal.
- These coatings are also used in gaming equipment and other decorative items, ensuring long-lasting performance and visual quality.
-
Environmental and Sustainability Benefits
- PVD coatings are considered a greener alternative to traditional chrome plating, as they do not produce toxic byproducts.
- Studies have shown that PVD coatings can extend the lifespan of products by up to ten times, reducing waste and promoting sustainability.
- Their ability to enhance durability and reduce maintenance makes them an eco-friendly choice for various industries.
In summary, PVD coatings are a highly versatile and valuable technology used across numerous industries to improve the performance, durability, and appearance of a wide range of products and components. Their applications span from high-tech aerospace and medical fields to everyday consumer goods, making them an essential part of modern manufacturing and design.
Summary Table:
Industry | Applications | Key Benefits |
---|---|---|
Aerospace & Automotive | Turbine blades, engine parts, pistons, wheels | Improved hardness, wear resistance, corrosion resistance, fuel efficiency |
Medical & Surgical | Surgical tools, implants, biomedical instruments | Enhanced biocompatibility, reduced friction, improved sterilization |
Consumer Goods | Kitchen fixtures, jewelry, eyeglass frames, sporting goods | Durable, scratch-resistant, aesthetic finishes |
Electronics & Optics | Semiconductors, photovoltaic cells, optical devices | Enhanced electrical conductivity, optical performance, environmental benefits |
Industrial Tools | Cutting tools, dies, molds | Extended tool lifespan, reduced downtime, high-temperature resistance |
Marine & Architecture | Marine hardware, lighting fixtures, bathroom accessories | Corrosion resistance, durability, aesthetic appeal |
Sustainability | Eco-friendly alternative to chrome plating | Reduced waste, extended product lifespan, lower maintenance costs |
Unlock the potential of PVD coatings for your industry—contact our experts today!