Pyrolytic decomposition is a thermochemical process where organic materials are chemically broken down at high temperatures (typically 400–1000°C) in the absence of oxygen. This process transforms complex, high-molecular-weight compounds into smaller molecules, producing gases (syngas), liquids (bio-oil), and solids (bio-char). Pyrolysis is widely used to convert biomass, plastics, and tires into useful products, reducing waste and generating valuable outputs. However, it is energy-intensive and requires precise conditions to operate effectively. The term "pyrolysis" originates from the Greek words "pyro" (fire) and "lysis" (separating), reflecting its nature of heat-driven separation.
Key Points Explained:
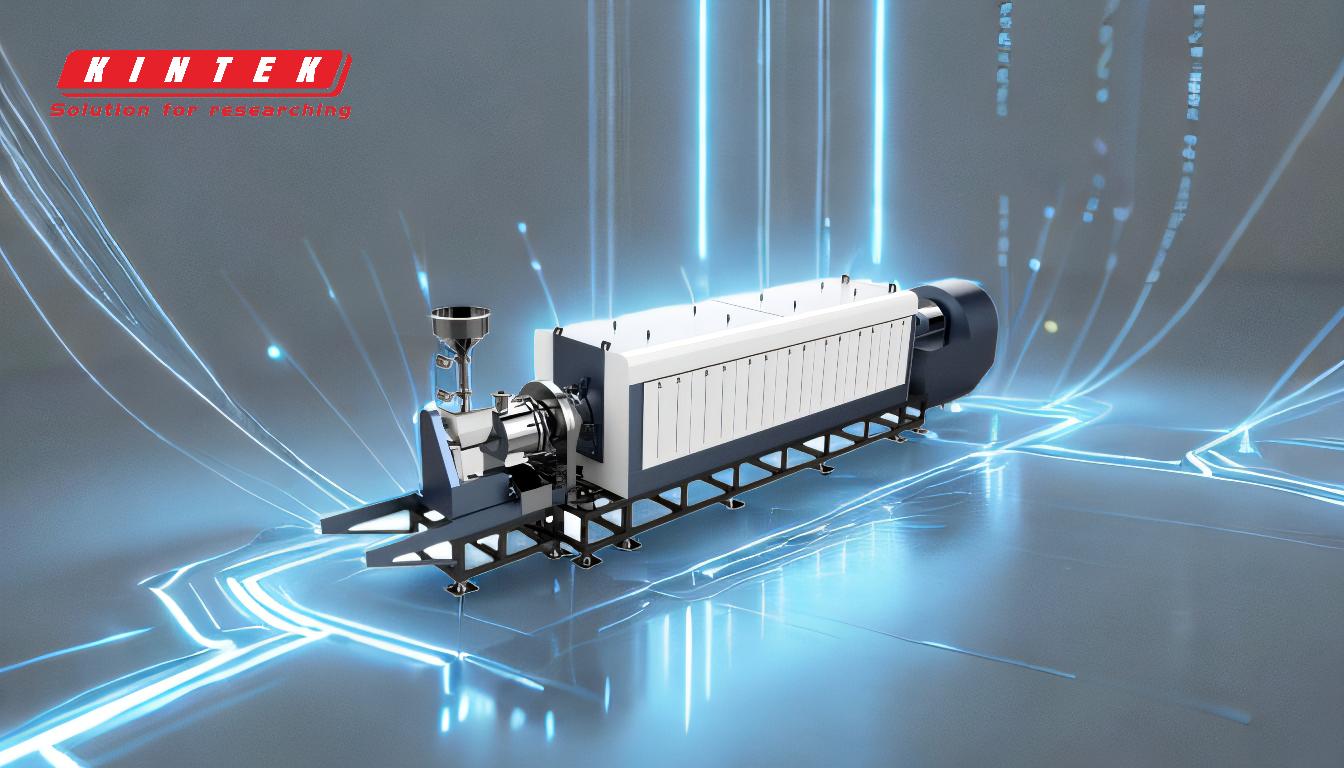
-
Definition and Mechanism of Pyrolysis:
- Pyrolysis is the thermal decomposition of organic materials at elevated temperatures (400–1000°C) in the absence of oxygen.
- The process involves breaking long-chain molecules into smaller molecules due to excessive thermal vibration at high temperatures.
- It is an irreversible process that simultaneously changes the physical phase and chemical composition of the material.
-
Products of Pyrolysis:
- Gases (Syngas): Includes hydrogen, carbon monoxide, and methane, which can be used as fuel or chemical feedstocks.
- Liquids (Bio-oil): A mixture of water and volatile organic compounds, often used as a renewable fuel or for chemical production.
- Solids (Bio-char): A carbon-rich material that can be used as a soil amendment or for carbon sequestration.
-
Applications of Pyrolysis:
- Waste Management: Converts biomass, plastics, and tires into useful products, reducing landfill waste.
- Energy Production: Generates syngas and bio-oil, which can be used as renewable energy sources.
- Chemical Production: Provides feedstock for producing chemicals and fuels.
-
Process Conditions:
- Temperature: Typically ranges from 400–1000°C, depending on the material and desired products.
- Atmosphere: Conducted in the absence of oxygen to prevent combustion and ensure decomposition.
- Pressure: Often performed under pressure to control the reaction and optimize product yields.
-
Challenges and Considerations:
- Energy Intensity: Requires significant energy input to achieve and maintain high temperatures.
- Process Control: Precise control of temperature, pressure, and reaction time is essential to optimize product composition and yield.
- Economic Viability: The cost-effectiveness of pyrolysis depends on the value of the products and the scale of the operation.
-
Comparison to Other Processes:
- Thermal Cracking: Similar to pyrolysis but typically operates at lower temperatures and is used in petroleum refining.
- Combustion: Involves the oxidation of materials in the presence of oxygen, producing heat and carbon dioxide, unlike pyrolysis, which occurs in the absence of oxygen.
-
Etymology and Historical Context:
- The term "pyrolysis" is derived from the Greek words "pyro" (fire) and "lysis" (separating), reflecting its nature of heat-driven separation.
- Historically, pyrolysis has been used for charcoal production and is now being adapted for modern waste management and energy production.
By understanding these key points, one can appreciate the complexity and potential of pyrolytic decomposition as a method for transforming organic materials into valuable products while addressing waste management challenges.
Summary Table:
Aspect | Details |
---|---|
Definition | Thermal decomposition of organic materials at 400–1000°C without oxygen. |
Products | - Gases (syngas) |
- Liquids (bio-oil)
- Solids (bio-char) | | Applications | Waste management, energy production, chemical feedstock. | | Process Conditions | - Temperature: 400–1000°C
- Atmosphere: Oxygen-free
- Pressure: Controlled | | Challenges | Energy-intensive, requires precise control, economic viability concerns. |
Discover how pyrolytic decomposition can transform your waste into valuable resources—contact us today!