A retort furnace is a specialized heating device used primarily in laboratories and industrial settings for processes such as heat treatment, distillation, and chemical reactions. It operates by applying controlled heat to materials within a sealed chamber, often using electric resistance heaters or gas burners. The furnace allows for precise regulation of atmospheric conditions, making it ideal for processes that require low or controlled atmospheres. Retort furnaces are particularly useful for heat treating metals, as they enable uniform heating and controlled cooling, which are essential for achieving desired material properties. Their ability to alter atmospheric conditions during a single firing cycle makes them versatile tools for both research and industrial applications.
Key Points Explained:
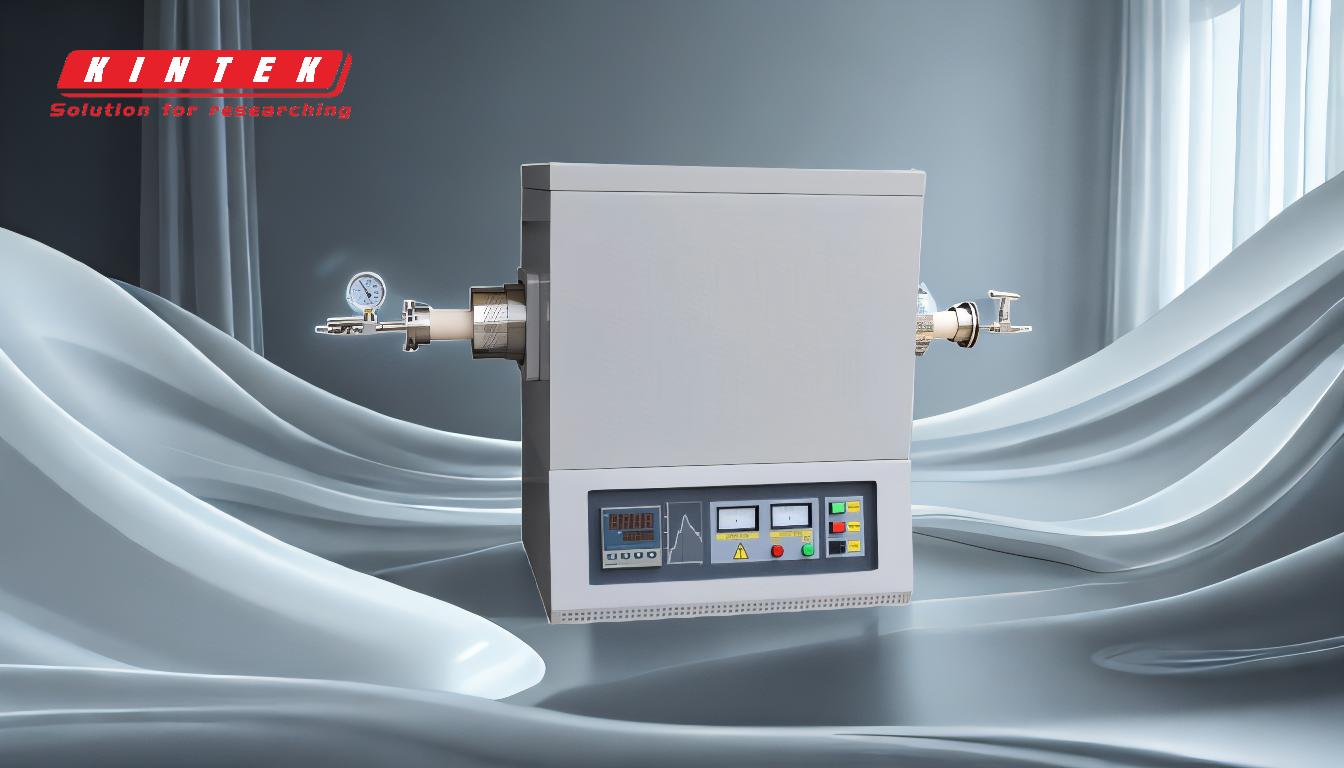
-
Function and Purpose of a Retort Furnace:
- A retort furnace is designed for heat treatment processes, distillation, and chemical reactions. It provides a controlled environment where materials can be heated uniformly and subjected to specific atmospheric conditions. This makes it suitable for applications such as annealing, sintering, and brazing, where precise temperature and atmosphere control are critical.
-
Heating Mechanism:
- The furnace typically uses electric resistance heaters or gas burners to generate heat. Electric resistance heaters are common in laboratory settings due to their precision and ease of control, while gas burners are often used in industrial applications for their high heat output. The heating process is regulated to ensure the furnace reaches and maintains the required temperature for the specific treatment process.
-
Atmospheric Control:
- One of the key features of a retort furnace is its ability to control the atmosphere within the heating chamber. This is achieved by sealing the chamber and introducing specific gases or maintaining a vacuum. The ability to alter atmospheric conditions during a single firing cycle allows for complex processes, such as carburizing or nitriding, which require specific gas compositions at different stages.
-
Applications in Heat Treatment:
- Retort furnaces are widely used in heat treatment processes to alter the physical and chemical properties of materials, particularly metals. For example, they are used in annealing to soften metals, in hardening to increase strength, and in tempering to reduce brittleness. The controlled environment ensures consistent results and prevents oxidation or contamination of the materials being treated.
-
Laboratory and Industrial Use:
- In laboratories, retort furnaces are used for distillation and chemical analysis, where precise control over temperature and atmosphere is essential. In industrial settings, they are employed for large-scale heat treatment of metals and other materials. The versatility of retort furnaces makes them valuable tools in both research and manufacturing.
-
Design and Structure:
- The furnace typically consists of a sealed chamber (retort) that houses the materials to be heated. The upper hot chamber corresponds to the classic retort furnace design, where the heating elements are located around the retort. This design ensures uniform heat distribution and efficient energy use.
-
Advantages of Retort Furnaces:
- The ability to control both temperature and atmosphere makes retort furnaces highly versatile. They are energy-efficient, as they can maintain a constant temperature once the desired level is reached. Additionally, their sealed design minimizes heat loss and prevents contamination, ensuring high-quality results in heat treatment and other processes.
By understanding these key points, purchasers of retort furnaces can make informed decisions based on their specific needs, whether for laboratory research or industrial applications. The precise control over heating and atmospheric conditions makes retort furnaces indispensable tools in material science and manufacturing.
Summary Table:
Key Feature | Description |
---|---|
Function | Designed for heat treatment, distillation, and chemical reactions. |
Heating Mechanism | Uses electric resistance heaters or gas burners for precise temperature control. |
Atmospheric Control | Sealed chamber allows for controlled or low atmospheres, including vacuum. |
Applications | Annealing, sintering, brazing, hardening, and tempering of metals. |
Laboratory & Industrial Use | Ideal for both research and large-scale industrial heat treatment. |
Advantages | Energy-efficient, uniform heating, and contamination-free results. |
Need a retort furnace for your heat treatment needs? Contact our experts today to find the perfect solution!