RF magnetron sputtering is a specialized technique used to deposit thin films onto substrates, particularly in applications requiring high-quality coatings. It combines the principles of radio frequency (RF) sputtering with magnetron technology to enhance the efficiency and quality of the deposition process. In RF magnetron sputtering, an RF power source is used to create a plasma, which bombards a target material, causing atoms to be ejected and deposited onto a substrate. The addition of a magnetic field near the target surface increases plasma density and sputtering rates, making it ideal for depositing insulating materials and achieving uniform coatings. This method is widely used in industries such as electronics, optics, and medical devices due to its ability to produce films with excellent crystallinity, purity, and adhesion.
Key Points Explained:
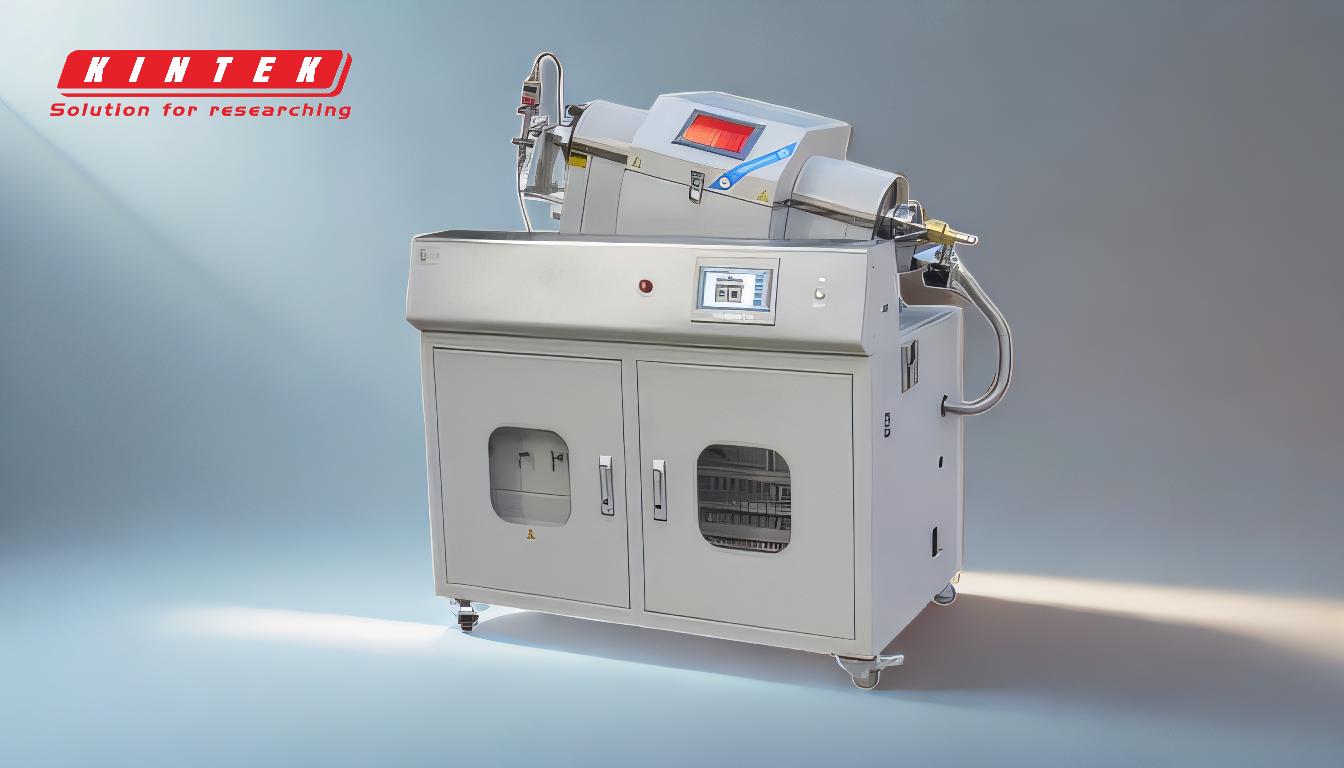
-
Basic Principle of RF Magnetron Sputtering:
- RF magnetron sputtering involves using an RF power source to generate a plasma. The plasma consists of ions that are accelerated toward a target material due to a negative voltage applied to the target.
- The ions collide with the target surface, transferring energy. If the energy exceeds the binding energy of the target atoms, sputtering occurs, ejecting neutral atoms from the target.
- These ejected atoms travel through the vacuum chamber and deposit onto a substrate, forming a thin film.
-
Role of Magnetic Fields:
- A key feature of magnetron sputtering is the use of magnetic fields. Permanent magnets or electromagnets are placed behind the target to create magnetic flux lines parallel to the target surface.
- These magnetic fields trap electrons near the target, increasing the density of the plasma and enhancing ion bombardment. This results in higher sputtering rates and more efficient deposition compared to conventional sputtering methods.
-
Advantages of RF Magnetron Sputtering:
- High-Quality Coatings: The process produces thin films with excellent crystallinity, purity, and uniformity, making it suitable for applications requiring precise material properties.
- Versatility: RF magnetron sputtering can deposit both conductive and insulating materials, unlike DC sputtering, which is limited to conductive targets.
- Low Operating Pressure: The process operates under low-pressure conditions, reducing contamination and improving film quality.
-
Applications of RF Magnetron Sputtering:
- Electronics: Used to deposit thin films for semiconductors, solar cells, and optical coatings.
- Medical Devices: Applied in the manufacture of anti-rejection coatings, dental implants, and radiation capsules.
- Optics: Utilized for creating reflective and anti-reflective coatings on lenses and mirrors.
-
Comparison with Other Sputtering Techniques:
- DC Sputtering: Limited to conductive materials and typically operates at higher pressures, resulting in lower film quality compared to RF magnetron sputtering.
- RF Sputtering: Can deposit insulating materials but lacks the enhanced plasma density provided by magnetron configurations.
- Magnetron Sputtering (DC and RF): Combines the benefits of magnetic fields with either DC or RF power sources, offering higher deposition rates and better film quality.
-
Challenges and Considerations:
- Industrial Scaling: While RF magnetron sputtering produces high-quality films, scaling the process for industrial applications can be challenging due to the need for precise control over vacuum conditions and magnetic fields.
- Cost: The equipment and operational costs for RF magnetron sputtering are higher than for simpler sputtering techniques, making it less suitable for some applications.
By combining RF power with magnetron technology, RF magnetron sputtering offers a powerful and versatile method for depositing high-quality thin films across a wide range of industries. Its ability to handle insulating materials and produce uniform coatings makes it a preferred choice for advanced applications in electronics, optics, and medical devices.
Summary Table:
Aspect | Details |
---|---|
Principle | Uses RF power to create plasma, ejecting target atoms for thin film deposition. |
Role of Magnetic Fields | Increases plasma density and sputtering rates for efficient deposition. |
Advantages | High-quality, uniform coatings; versatile for conductive and insulating materials. |
Applications | Electronics, medical devices, optics, and more. |
Challenges | High equipment costs and scaling difficulties for industrial use. |
Discover how RF magnetron sputtering can elevate your thin film processes—contact our experts today!