A rotary kiln electric furnace is a specialized thermal processing equipment designed for calcining, roasting, or drying granular and powdery materials. It combines the principles of a rotary kiln with electric heating to achieve uniform heat distribution and consistent radial temperature. The furnace operates by rotating a long barrel slightly inclined to ensure materials are evenly heated and processed. This design promotes thorough mixing and turning of materials, enhancing the treatment effect. Key components include the shell, refractory lining, support tyres, drive gear, and internal heat exchangers. The electric heating method ensures precise temperature control and energy efficiency, making it suitable for applications requiring indirect continuous heating, such as in the production of lithium batteries or other materials needing uniform heat treatment.
Key Points Explained:
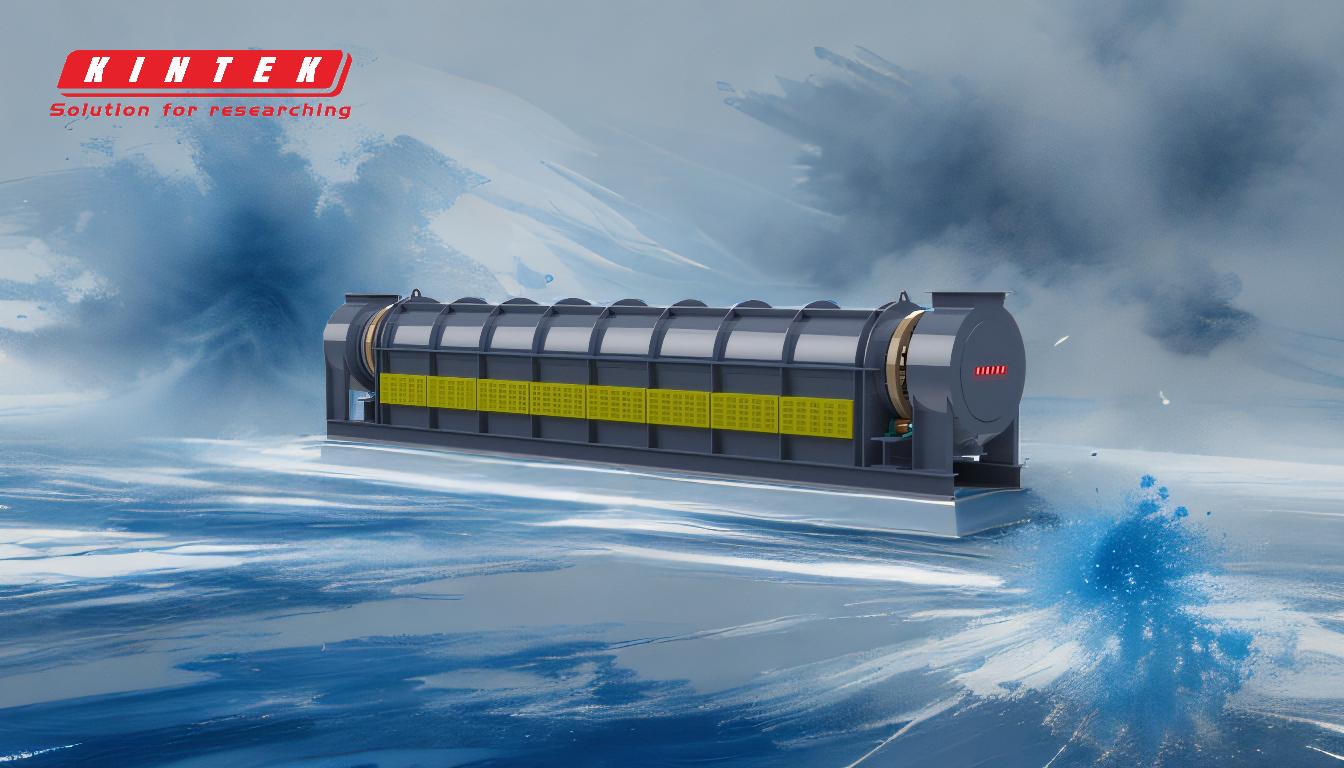
-
Definition and Function:
- A rotary kiln electric furnace is a thermal processing equipment used for calcining, roasting, or drying granular and powdery materials. It combines the rotation mechanism of a kiln with electric heating to ensure uniform heat distribution and consistent radial temperature.
-
Key Components:
- Shell: The outer structure of the furnace that houses the internal components.
- Refractory Lining: A heat-resistant material lining the inside of the shell to protect it from high temperatures.
- Support Tyres (Riding Rings) and Rollers: These components support the rotating barrel and allow it to rotate smoothly.
- Drive Gear: The mechanism that drives the rotation of the barrel.
- Internal Heat Exchangers: Components that facilitate the transfer of heat to the materials being processed.
-
Operation Mechanism:
- The furnace operates by rotating a long barrel slightly inclined. This rotation ensures that materials are evenly heated and processed, promoting thorough mixing and turning of materials.
- The heat required for the material is obtained by electric heating outside the barrel, ensuring precise temperature control and uniform heat distribution.
-
Applications:
- Lithium Battery Production: The uniform heat distribution and consistent radial temperature make it ideal for the production of lithium batteries, ensuring uniform and consistent heat treatment.
- Other Materials: Suitable for various materials requiring indirect continuous heating, such as calcining, roasting, or drying processes.
-
Advantages:
- Uniform Heat Distribution: Ensures consistent radial temperature, enhancing the treatment effect.
- Precise Temperature Control: Electric heating allows for precise control of the temperature, ensuring optimal processing conditions.
- Energy Efficiency: Electric heating is more energy-efficient compared to traditional combustion methods, reducing fuel consumption.
-
Comparison with Other Furnaces:
- Indirect-Fired Rotary Kiln: Unlike an indirect-fired rotary kiln, which uses combustion chambers and flue gas for heating, a rotary kiln electric furnace uses electric heating, offering better temperature control and energy efficiency.
- Retort Furnace: While a retort furnace offers quicker heating times and improved operating conditions, a rotary kiln electric furnace provides more uniform heat distribution and is better suited for continuous processing of granular and powdery materials.
By understanding these key points, a purchaser can make an informed decision about whether a rotary kiln electric furnace meets their specific thermal processing needs.
Summary Table:
Aspect | Details |
---|---|
Definition | Thermal processing equipment for calcining, roasting, or drying materials. |
Key Components | Shell, refractory lining, support tyres, drive gear, internal heat exchangers. |
Operation Mechanism | Rotates an inclined barrel for uniform heating and material mixing. |
Applications | Lithium battery production, calcining, roasting, drying processes. |
Advantages | Uniform heat distribution, precise temperature control, energy efficiency. |
Ready to enhance your thermal processing? Contact us today to learn more about rotary kiln electric furnaces!