Safety in the pyrolysis process is a multifaceted concern that involves mitigating risks associated with high temperatures, flammable materials, and toxic byproducts. The process operates at temperatures exceeding the autoignition point of produced gases, creating significant explosion risks if oxygen is present. Additionally, toxic gases like carbon monoxide are generated, posing health hazards. Safety measures must address equipment integrity, human safety, and process control, particularly during critical phases like startup, shutdown, and operational upsets. Inert gas purging is essential to prevent explosions, and rigorous monitoring is required to ensure safe operations. Neglecting these precautions can lead to fires, explosions, and severe injuries.
Key Points Explained:
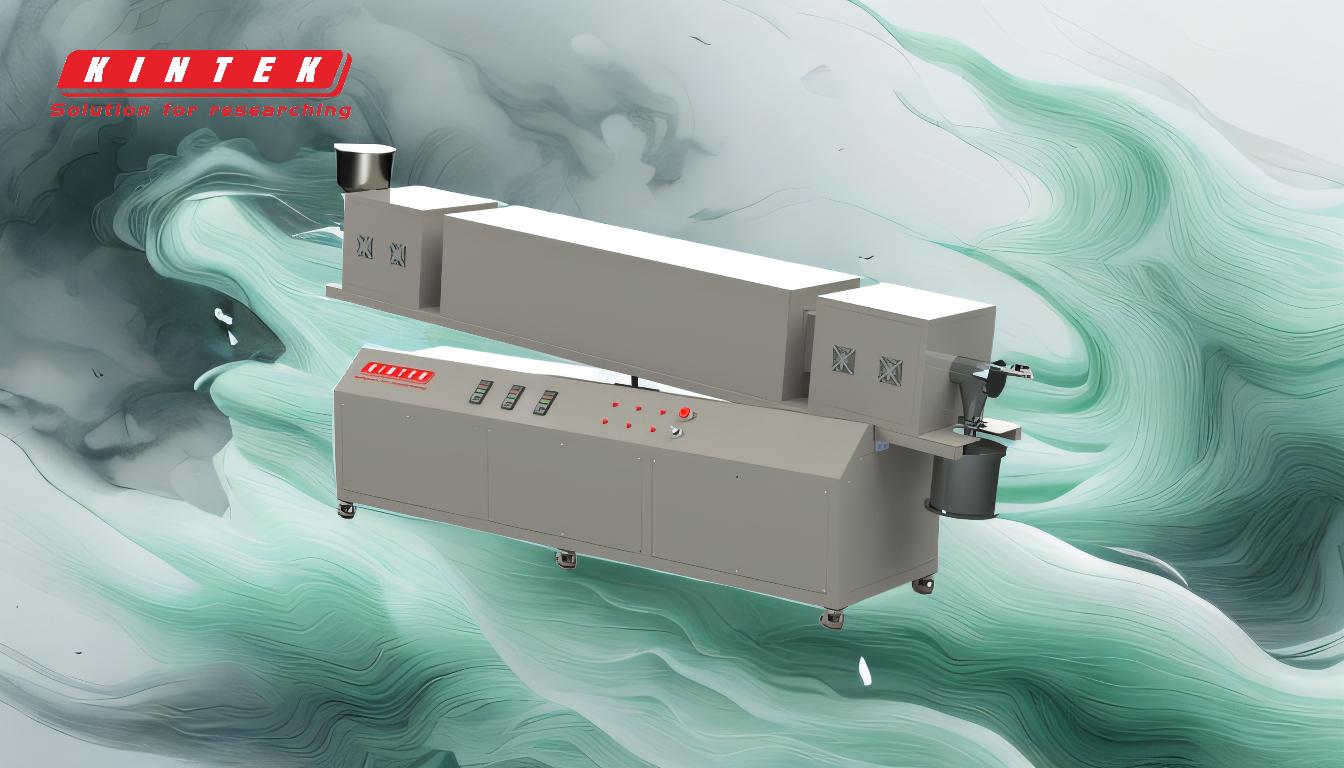
-
High-Temperature Risks:
- Pyrolysis involves heating materials to extremely high temperatures, often exceeding the autoignition point of the gases produced.
- These temperatures create a significant risk of explosion if oxygen is introduced into the system.
- The process must be carefully controlled to prevent thermal runaway or overheating, which can lead to equipment failure and hazardous conditions.
-
Explosion Hazards:
- The presence of oxygen in the pyrolysis chamber can trigger explosions due to the flammable nature of the gases produced.
- Inert gas purging (e.g., using nitrogen) is critical to displace oxygen and minimize explosion risks.
- Accidents have occurred when oxygen levels were not adequately controlled, emphasizing the importance of robust safety protocols.
-
Toxic Gas Emissions:
- Pyrolysis generates toxic gases, primarily carbon monoxide, which poses serious health risks to workers.
- Proper ventilation and gas detection systems are essential to monitor and manage these emissions.
- Failure to control toxic gas release can lead to acute or chronic health issues for personnel and environmental contamination.
-
Critical Operational Phases:
- The highest risks occur during system startup, shutdown, intermittent operation, and operational upsets.
- These phases require heightened vigilance and adherence to safety protocols to prevent accidents.
- Operators must be trained to handle these scenarios safely and respond effectively to any deviations from normal operation.
-
Equipment Safety:
- Pyrolysis equipment must be designed to withstand high temperatures and pressures without failure.
- Regular maintenance and inspections are necessary to ensure the integrity of the equipment.
- Safety features such as pressure relief valves, temperature sensors, and emergency shutdown systems are critical to prevent catastrophic failures.
-
Human Safety:
- Workers must be provided with appropriate personal protective equipment (PPE) to safeguard against high temperatures, toxic gases, and potential explosions.
- Comprehensive training programs should be implemented to educate workers on the risks and proper safety procedures.
- Emergency response plans must be in place to address accidents swiftly and minimize harm.
-
Process Safety:
- Continuous monitoring and control of process parameters (e.g., temperature, pressure, gas composition) are essential to maintain safe operations.
- Automated systems and alarms can help detect and respond to abnormal conditions in real time.
- Process safety management (PSM) systems should be implemented to identify, assess, and mitigate risks throughout the pyrolysis process.
-
Waste Handling and Storage:
- Proper handling and storage of raw materials and byproducts are critical to prevent fires, explosions, and environmental contamination.
- Flammable or reactive materials should be stored in designated areas with appropriate safety measures.
- Waste disposal must comply with regulatory standards to minimize environmental impact.
-
Regulatory Compliance:
- Pyrolysis facilities must adhere to local, national, and international safety regulations and standards.
- Regular audits and inspections should be conducted to ensure compliance and identify areas for improvement.
- Documentation of safety procedures, incident reports, and training records is essential for accountability and continuous improvement.
-
Risk Mitigation Strategies:
- Implementing redundant safety systems (e.g., dual gas detectors, backup power supplies) can reduce the likelihood of accidents.
- Conducting hazard and operability studies (HAZOP) and risk assessments can help identify potential risks and develop mitigation strategies.
- Continuous improvement of safety protocols based on lessons learned from incidents and near-misses is crucial for maintaining a safe operating environment.
By addressing these key points, the pyrolysis process can be conducted safely, minimizing risks to personnel, equipment, and the environment. A proactive approach to safety, combined with rigorous training and adherence to best practices, is essential to prevent accidents and ensure the long-term viability of pyrolysis operations.
Summary Table:
Key Safety Concern | Description |
---|---|
High-Temperature Risks | Risk of explosion if oxygen is introduced; requires precise temperature control. |
Explosion Hazards | Inert gas purging (e.g., nitrogen) is essential to displace oxygen. |
Toxic Gas Emissions | Carbon monoxide and other toxic gases require proper ventilation and monitoring. |
Critical Operational Phases | Highest risks during startup, shutdown, and operational upsets. |
Equipment Safety | Regular maintenance and safety features like pressure relief valves are crucial. |
Human Safety | PPE, training, and emergency response plans protect workers. |
Process Safety | Continuous monitoring and automated systems ensure safe operations. |
Regulatory Compliance | Adherence to local and international safety standards is mandatory. |
Risk Mitigation Strategies | Redundant safety systems and HAZOP studies reduce accident risks. |
Ensure your pyrolysis process is safe and efficient—contact our experts today for tailored solutions!