Sintered ceramics, also known as sintered stone or ultra-compact surfaces, are man-made materials created by grinding natural minerals like silica, quartz, feldspars, and clay into fine particles. These particles are then compacted under extreme heat and pressure, without melting, to form a dense, durable solid slab. This process mimics the natural formation of stone but occurs over a much shorter time. Sintered ceramics are highly resistant to UV rays, scratches, extreme temperatures, stains, and abrasion, making them ideal for high-traffic and demanding applications. They are widely used in construction, interior design, and industrial applications due to their superior mechanical strength, hardness, and thermal stability.
Key Points Explained:
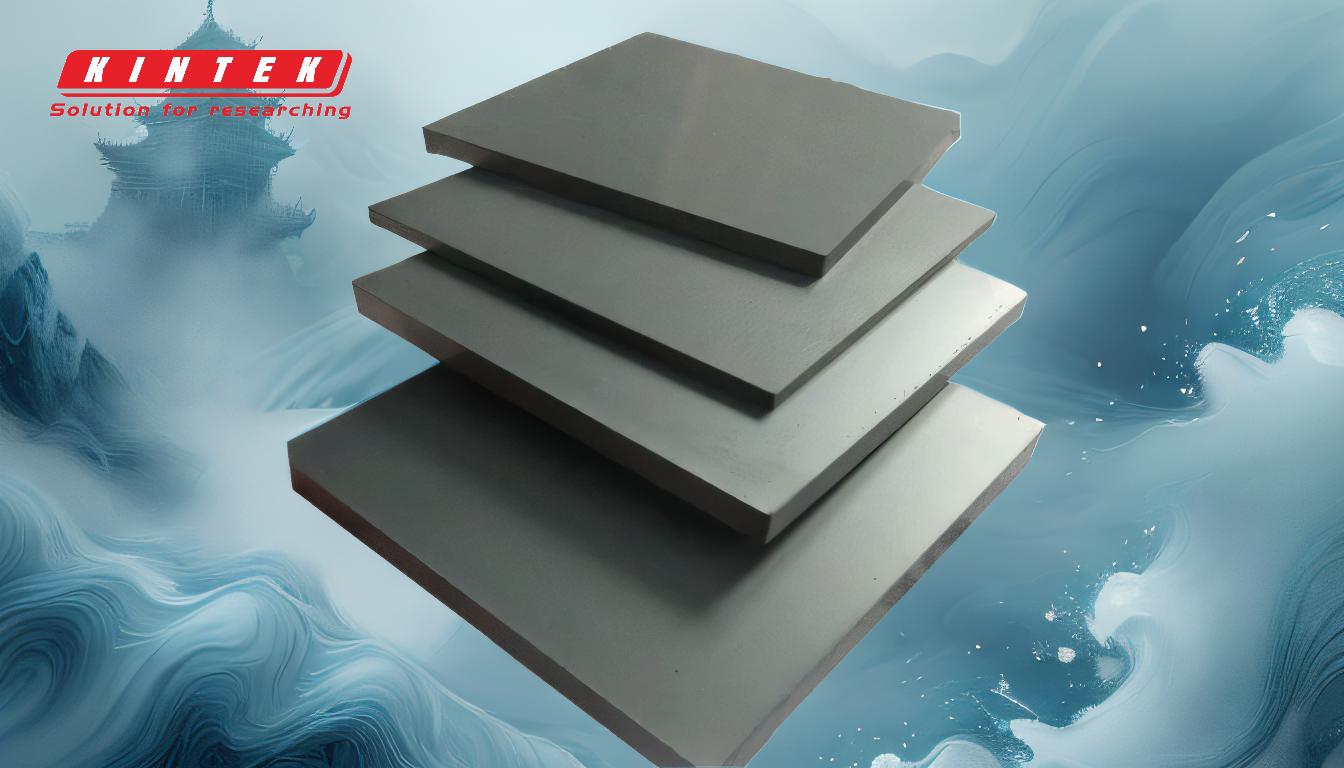
-
Definition and Composition of Sintered Ceramics
- Sintered ceramics are man-made materials crafted from natural minerals such as silica, quartz, feldspars, clay, and mineral pigments.
- These raw materials are ground into fine particles and then compacted under extreme heat and pressure to form a solid slab.
- Unlike traditional ceramics, sintering does not involve melting the material, which preserves its natural properties while enhancing its density and durability.
-
The Sintering Process
- Sintering is an accelerated version of the natural stone formation process, compressing millions of years of geological activity into a short timeframe.
- The process involves:
- Grinding natural materials into fine particles.
- Compacting the particles under extreme pressure (greater than the weight of the Eiffel Tower).
- Firing the compacted slab in a kiln at temperatures around 1200°C to fuse the particles together.
- This process reduces porosity, creating a dense, non-porous material with enhanced mechanical and thermal properties.
-
Properties and Advantages of Sintered Ceramics
- Durability: Sintered ceramics are highly resistant to scratches, extreme temperatures, UV rays, water, stains, and abrasion, making them suitable for high-traffic areas.
- Mechanical Strength: The sintering process improves the material's hardness and mechanical strength, making it ideal for demanding applications.
- Thermal Stability: Sintered ceramics can withstand extreme temperatures without warping or cracking, ensuring long-term performance.
- Aesthetic Versatility: Available in a wide range of colors, textures, and finishes, sintered ceramics can mimic natural stone or offer unique designs.
-
Applications of Sintered Ceramics
- Construction and Interior Design: Used for countertops, flooring, wall cladding, and facades due to their durability and aesthetic appeal.
- Industrial Applications: Ideal for cutting tools, refractory materials, and electrical insulators due to their hardness and thermal stability.
- Additive Manufacturing: Sintering is used in 3D printing to create custom metal shapes and reduce energy consumption compared to traditional melting processes.
- Other Uses: Sintered ceramics are also used in the production of filters, sanitaryware, and other specialized components.
-
Comparison with Natural Stone and Other Materials
- Sintered ceramics offer the aesthetic appeal of natural stone but with enhanced durability and resistance to environmental factors.
- Unlike natural stone, sintered ceramics are non-porous, making them resistant to staining and bacterial growth.
- Compared to traditional ceramics, sintered ceramics have superior mechanical and thermal properties due to the high-pressure compaction and firing process.
-
Environmental and Economic Considerations
- The sintering process is energy-efficient compared to traditional melting methods, reducing the carbon footprint.
- Sintered ceramics are made from abundant natural materials, making them a sustainable choice for construction and industrial applications.
- Their durability and low maintenance requirements result in long-term cost savings for users.
In summary, sintered ceramics are a versatile, durable, and sustainable material created through a unique process that combines natural minerals with advanced manufacturing techniques. Their exceptional properties make them suitable for a wide range of applications, from construction to industrial uses, offering both aesthetic and functional benefits.
Summary Table:
Aspect | Details |
---|---|
Composition | Natural minerals like silica, quartz, feldspars, and clay. |
Sintering Process | Grinding, compacting under extreme pressure, firing at ~1200°C. |
Key Properties | Durable, scratch-resistant, UV-resistant, thermal-stable, non-porous. |
Applications | Countertops, flooring, wall cladding, industrial tools, 3D printing. |
Advantages | Superior strength, aesthetic versatility, sustainability, cost-efficiency. |
Learn more about how sintered ceramics can transform your projects—contact us today!