Sintering in a furnace is a thermal process used to compact and form a solid mass of material by heating it below its melting point. This process is widely used in various industries, including ceramics, metallurgy, and dentistry, to create durable and high-performance components. The sintering process typically involves three stages: forming a green part with a bonding agent, removing the bonding agent through heating, and fusing the primary particles at elevated temperatures. In specialized applications like dental restorations, precise control of temperature, pressure, and atmosphere is critical to ensure the quality and stability of the final product.
Key Points Explained:
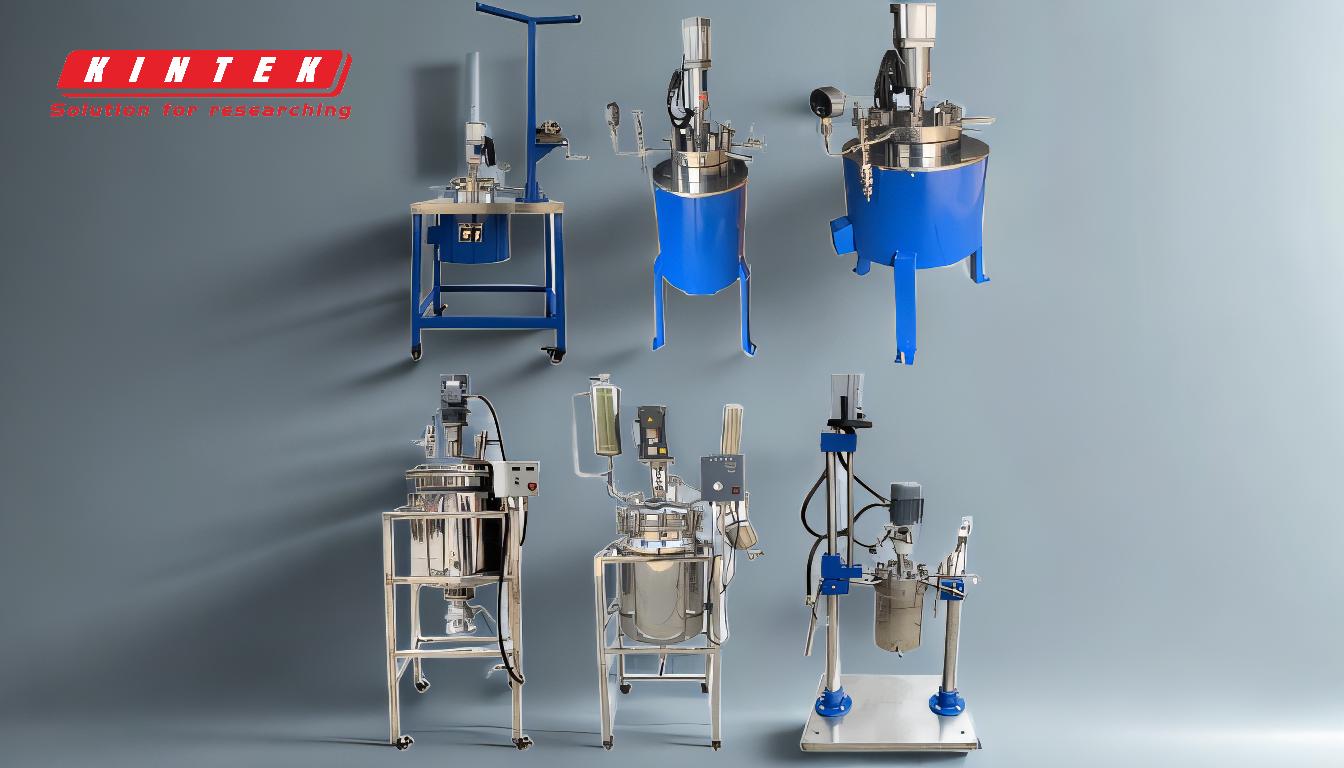
-
Definition of Sintering:
- Sintering is a thermal process where powdered materials are heated below their melting point to form a solid mass. This process is used to enhance the strength, density, and structural integrity of materials.
-
Three Stages of Sintering:
-
Stage 1: Forming the Green Part:
- A blend of primary powder and a bonding agent (such as water, wax, or polymer) is shaped into the desired form. The bonding agent holds the powder particles together, creating a "green part" that is fragile but holds its shape.
-
Stage 2: Removal of the Bonding Agent:
- During heating, the bonding agent evaporates or burns away. This step is crucial to prevent contamination and ensure the purity of the final product.
-
Stage 3: Particle Fusion:
- As the temperature increases, the primary particles begin to melt at their surfaces, causing them to fuse together. Alternatively, an intermediate bonding agent (like bronze) may melt and bond the particles while leaving the primary material unchanged.
-
Stage 1: Forming the Green Part:
-
Importance of Temperature, Pressure, and Atmosphere:
- In applications like dental sintering, precise control of these parameters is essential. For example:
- Temperature: Must be carefully regulated to ensure proper particle fusion without overheating, which could damage the material.
- Pressure: Applied to compact the material further, enhancing density and strength.
- Atmosphere: Controlled to prevent oxidation or contamination, especially in sensitive materials like ceramics or metals.
- In applications like dental sintering, precise control of these parameters is essential. For example:
-
Applications of Sintering:
- Sintering is used in various industries, including:
- Ceramics: To produce durable and heat-resistant components.
- Metallurgy: To create metal parts with high strength and precision.
- Dentistry: To fabricate dental restorations like crowns and bridges, where precision and material integrity are critical.
- Sintering is used in various industries, including:
-
Advantages of Sintering:
- Material Efficiency: Minimal waste, as powdered materials are used.
- Complex Shapes: Allows for the creation of intricate geometries that are difficult to achieve with other methods.
- Enhanced Properties: Improves mechanical strength, density, and thermal stability of materials.
-
Challenges in Sintering:
- Precision Requirements: Achieving the right balance of temperature, pressure, and atmosphere can be challenging, especially in high-precision fields like dentistry.
- Material Limitations: Not all materials are suitable for sintering, and some may require specialized equipment or conditions.
By understanding the sintering process and its stages, manufacturers and purchasers can make informed decisions about equipment and materials, ensuring high-quality outcomes in their respective applications.
Summary Table:
Aspect | Details |
---|---|
Definition | Heating powdered materials below melting point to form a solid mass. |
Stages | 1. Forming green part with bonding agent. 2. Removing bonding agent. 3. Fusing primary particles. |
Key Parameters | Temperature, pressure, and atmosphere control for precision. |
Applications | Ceramics, metallurgy, dentistry (e.g., crowns, bridges). |
Advantages | Material efficiency, complex shapes, enhanced mechanical properties. |
Challenges | Precision requirements, material limitations. |
Discover how sintering can optimize your production process—contact us today for expert advice!