Sintering is a critical process in mechanical engineering and materials science, where powdery materials are transformed into dense, solid bodies through the application of heat and pressure without reaching the material's melting point. This process is widely used in industries such as powder metallurgy, ceramics, and plastics to create components with enhanced strength, durability, and structural integrity. By bonding adjacent particles through atomic diffusion, sintering ensures the final product exhibits the desired material properties, making it indispensable for manufacturing high-performance parts.
Key Points Explained:
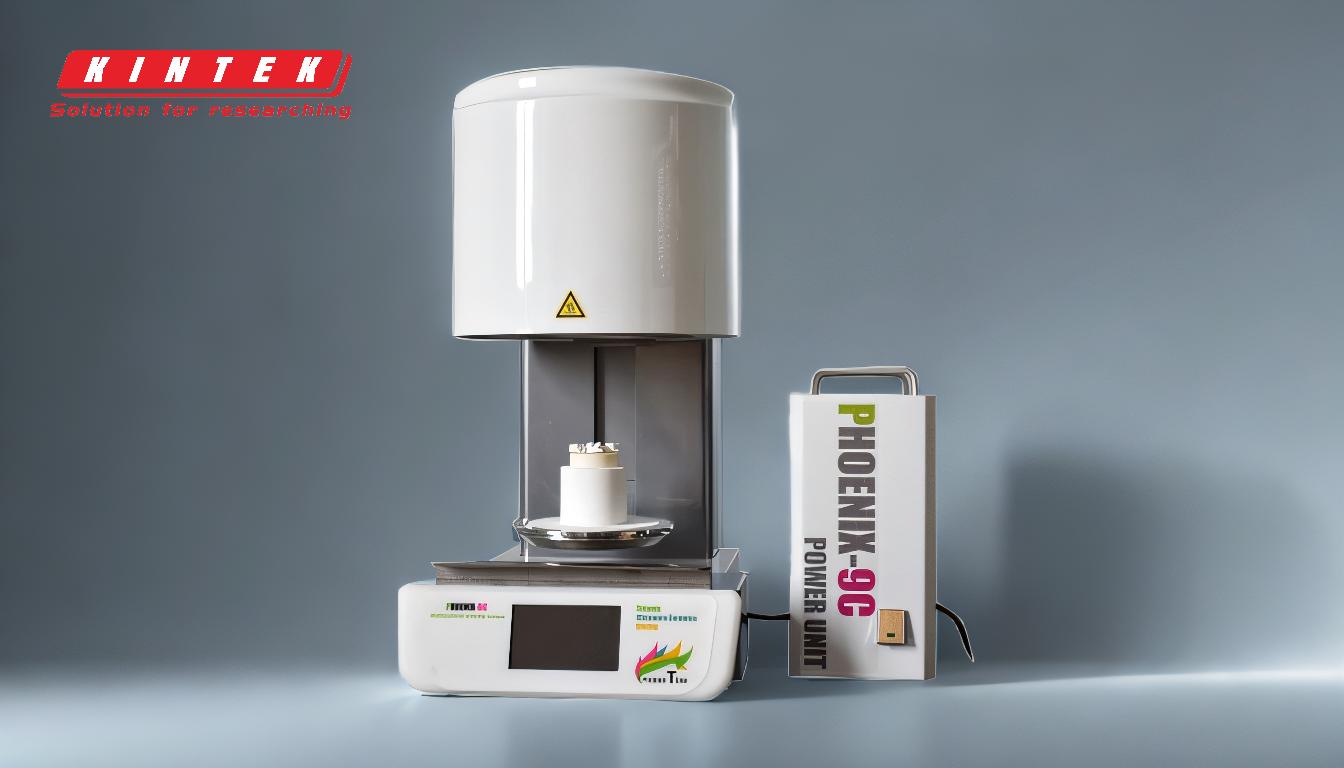
-
Definition of Sintering
- Sintering is the process of transforming powdery materials into dense, solid bodies by applying heat and pressure below the material's melting point.
- It involves the bonding of adjacent particles through atomic diffusion, creating a cohesive mass without liquefaction.
-
Key Components of Sintering
- Heat Application: Heat is applied to facilitate atomic diffusion, allowing particles to bond. The temperature is carefully controlled to remain below the melting point.
- Pressure Application: Pressure helps compact the particles, reducing voids and increasing density.
- Material Diffusion: Atoms diffuse across particle boundaries, fusing them into a single solid structure.
-
Materials Suitable for Sintering
- Metals: Commonly used in powder metallurgy to produce components like gears, bearings, and automotive parts.
- Ceramics: Used in the production of pottery, tiles, and advanced ceramic components.
- Plastics: Applied in creating durable plastic parts with enhanced mechanical properties.
- Other Materials: Includes composites and materials with extremely high melting points, such as tungsten and molybdenum.
-
Applications of Sintering
- Powder Metallurgy: Produces metal components with high strength and precision, such as automotive parts and tools.
- Ceramic Manufacturing: Creates durable ceramic products like tiles, insulators, and advanced ceramics for industrial use.
- Plastic Industry: Enhances the mechanical properties of plastic parts, making them suitable for high-stress applications.
- High-Temperature Materials: Used for materials like tungsten and molybdenum, which are difficult to process using traditional melting methods.
-
Advantages of Sintering
- Enhanced Material Properties: Results in materials with improved strength, durability, and structural integrity.
- Cost-Effective: Reduces material waste and allows for the production of complex shapes with minimal machining.
- Versatility: Applicable to a wide range of materials, including metals, ceramics, and plastics.
- Precision: Enables the production of components with tight tolerances and consistent quality.
-
Challenges and Considerations
- Temperature Control: Precise control of temperature is required to avoid melting and ensure proper bonding.
- Porosity Management: Achieving full density can be challenging, requiring optimization of pressure and sintering time.
- Material Selection: Not all materials are suitable for sintering, and the process may require additional steps like compaction or the use of binders.
-
Comparison with Other Processes
- Sintering vs. Melting: Unlike melting, sintering does not liquefy the material, preserving its original structure and properties.
- Sintering vs. Casting: Sintering produces components with higher density and fewer defects compared to casting.
- Sintering vs. Machining: Sintering reduces material waste and allows for the production of complex shapes that are difficult to achieve through machining.
-
Future Trends in Sintering
- Additive Manufacturing: Combining sintering with 3D printing technologies to produce complex, high-performance components.
- Nanomaterials: Exploring the sintering of nanoparticles to create advanced materials with unique properties.
- Sustainability: Developing eco-friendly sintering processes to reduce energy consumption and environmental impact.
By understanding sintering in mechanical terms, manufacturers and engineers can leverage this process to produce high-quality components with superior mechanical properties, ensuring their suitability for demanding applications across various industries.
Summary Table:
Aspect | Details |
---|---|
Definition | Process of bonding powdery materials using heat and pressure below melting. |
Key Components | Heat, pressure, and atomic diffusion. |
Materials | Metals, ceramics, plastics, and high-melting-point materials. |
Applications | Powder metallurgy, ceramics, plastics, and high-temperature materials. |
Advantages | Enhanced strength, cost-effectiveness, versatility, and precision. |
Challenges | Temperature control, porosity management, and material suitability. |
Future Trends | Additive manufacturing, nanomaterials, and sustainability innovations. |
Discover how sintering can revolutionize your manufacturing process—contact our experts today!