Spark Plasma Sintering (SPS) is an advanced sintering technique that combines plasma activation, hot pressing, and resistance heating to achieve rapid and efficient densification of materials. It operates at lower temperatures compared to traditional sintering methods, saving energy and time while producing high-density, fine-grained, and mechanically robust sintered bodies. The process involves localized heating through electrical discharges between powder particles, which purifies and activates the surfaces, leading to the formation of strong bonds ("necks") between particles. Key advantages include uniform heating, fast sintering speed, and the ability to maintain the microstructure of the original particles, making it ideal for producing advanced materials with superior properties.
Key Points Explained:
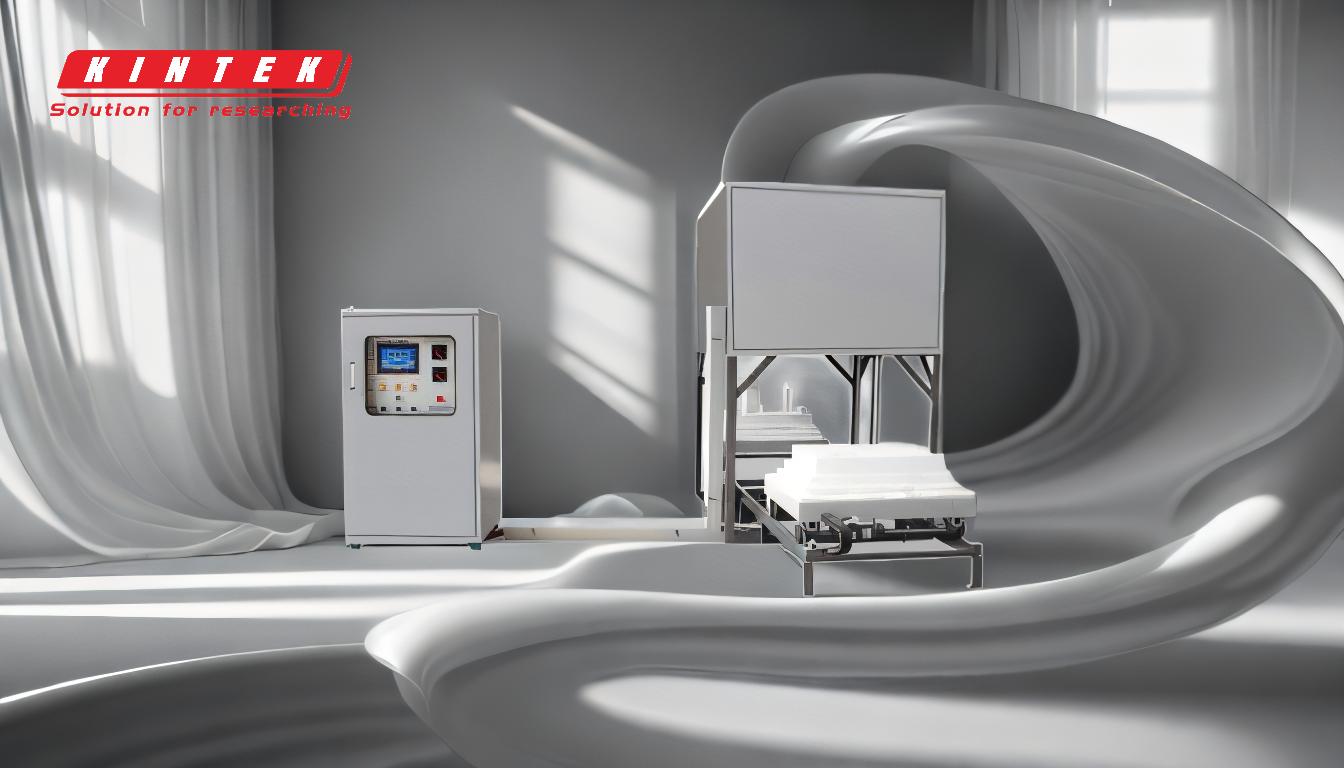
-
What is Spark Plasma Sintering (SPS)?
- SPS is a modern sintering technique that integrates plasma activation, hot pressing, and resistance heating. It uses a pulsed direct current (DC) to generate localized heating between powder particles, enabling rapid densification at lower temperatures.
- The process is particularly effective for materials with high melting points, such as ceramics, metals, and composites, as it avoids the need for extreme temperatures.
-
How Does SPS Work?
- During the plasma heating stage, electrical discharges occur between powder particles, creating localized heating up to several thousand degrees Celsius. This heating is uniform across the sample, purifying particle surfaces by vaporizing impurities.
- The purified surfaces melt and fuse, forming "necks" between particles, which are essential for creating a dense and strong sintered body.
- The process also involves Joule heating from resistance heating and plastic deformation caused by applied pressure, further enhancing densification.
-
Advantages of SPS
- Fast Heating and Sintering: SPS achieves rapid heating rates and short sintering times, significantly reducing processing time compared to conventional methods.
- Lower Sintering Temperature: The process operates at temperatures lower than traditional sintering, saving energy and minimizing thermal stress on materials.
- Uniform Heating: The uniform distribution of heat ensures consistent material properties throughout the sintered body.
- High Density and Fine Microstructure: SPS inhibits grain growth, maintaining a fine and uniform microstructure, which improves mechanical properties such as strength and toughness.
- Energy Efficiency: The combination of low-temperature operation and fast processing makes SPS an energy-efficient method.
-
Applications of SPS
- SPS is widely used in the research and production of advanced materials, including ceramics, metals, composites, and nanomaterials.
- It is particularly beneficial for materials that require high density, fine grain size, and superior mechanical properties, such as cutting tools, aerospace components, and biomedical implants.
-
Comparison with Traditional Sintering Methods
- Traditional sintering methods, such as hot pressing and pressureless sintering, often require higher temperatures and longer processing times, leading to grain growth and reduced material performance.
- SPS overcomes these limitations by enabling rapid sintering at lower temperatures, preserving the microstructure and enhancing the final product's properties.
-
Unique Features of SPS
- Plasma Activation: The electrical discharges between particles activate and purify the surfaces, promoting better bonding.
- Resistance Heating: Joule heating from the applied current provides additional heat, aiding in densification.
- Pressure Application: The applied pressure enhances plastic deformation, reducing porosity and improving density.
In summary, Spark Plasma Sintering is a highly efficient and versatile technique for producing dense, high-performance materials with fine microstructures. Its unique combination of plasma activation, resistance heating, and pressure application makes it a superior choice for advanced material fabrication.
Summary Table:
Aspect | Details |
---|---|
Technique | Combines plasma activation, hot pressing, and resistance heating. |
Key Advantage | Fast sintering at lower temperatures, saving energy and time. |
Heating Mechanism | Electrical discharges create localized heating, purifying particle surfaces. |
Benefits | High density, fine microstructure, and superior mechanical properties. |
Applications | Ceramics, metals, composites, cutting tools, aerospace, and biomedical. |
Learn how Spark Plasma Sintering can transform your material fabrication process—contact us today!