Spark plasma sintering (SPS) is an advanced sintering technique that offers significant advantages over traditional methods, particularly for polymers and other materials. It combines plasma activation, hot pressing, and resistance heating to achieve rapid sintering at lower temperatures, preserving the microstructure and enhancing material properties. This method is energy-efficient, time-saving, and produces materials with uniform grains, high density, and excellent mechanical properties. SPS is widely used for sintering metals, ceramics, and composites, making it a valuable tool in the research and production of advanced materials.
Key Points Explained:
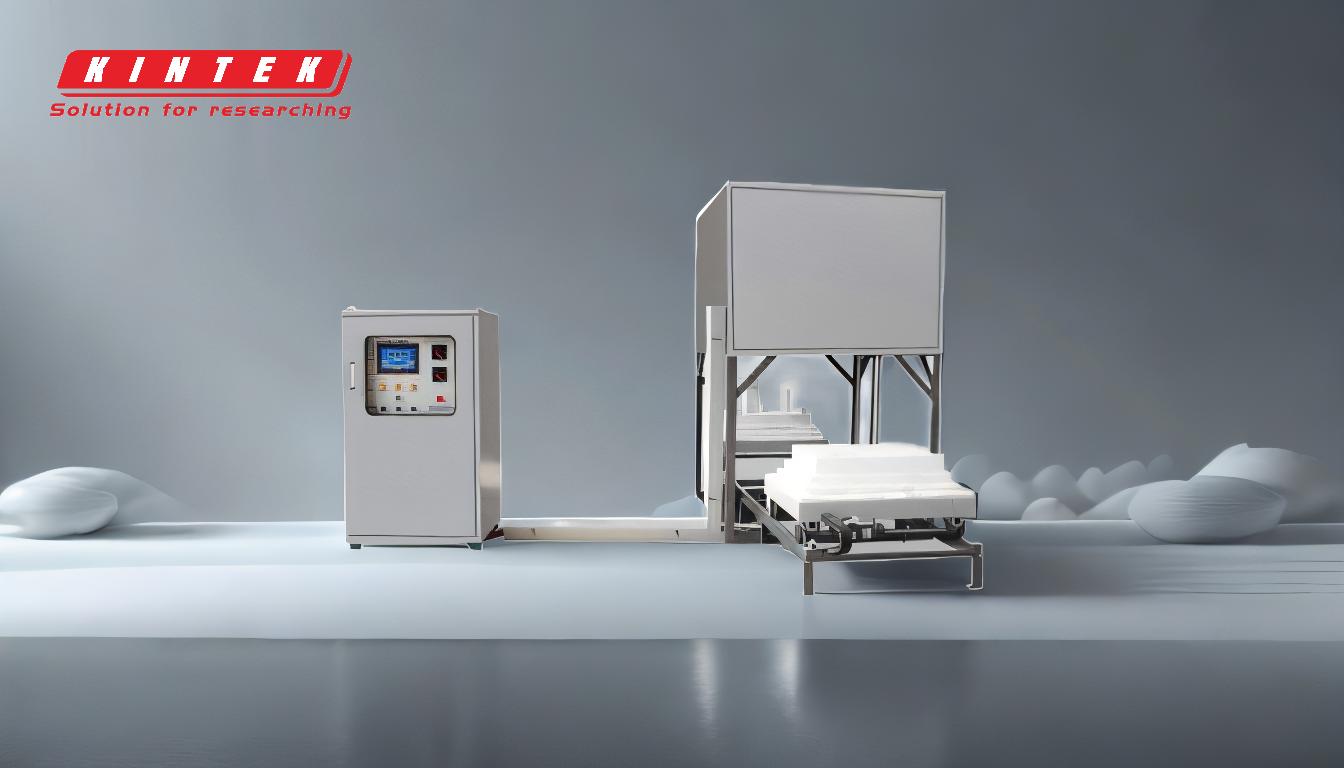
-
What is Spark Plasma Sintering (SPS)?
- SPS is a modern sintering technique that integrates plasma activation, hot pressing, and resistance heating. It uses a DC pulse voltage to generate Joule heat, causing plastic deformation and discharge between powder particles. This unique combination of mechanisms allows for rapid sintering at lower temperatures compared to traditional methods.
-
Advantages of SPS for Polymers and Other Materials:
- Fast Heating Speed: SPS achieves rapid heating, significantly reducing the time required for sintering.
- Lower Sintering Temperature: The process operates at lower temperatures, which is particularly beneficial for heat-sensitive materials like polymers.
- Uniform Heating: Ensures consistent material properties throughout the sintered body.
- Energy Efficiency: SPS consumes less energy due to its shorter processing times and lower temperatures.
- Improved Material Properties: The resulting sintered materials have fine, uniform grain structures, high density, and enhanced mechanical properties.
-
Mechanisms Involved in SPS:
- Joule Heating: The primary heat source in SPS, generated by the resistance of the material to the electric current.
- Plastic Deformation: Pressure applied during sintering causes the particles to deform and bond more effectively.
- Discharge Between Particles: The electric discharge between particles helps to activate their surfaces, promoting better bonding and densification.
-
Applications of SPS:
- Metals and Ceramics: SPS is widely used for sintering these materials, producing high-density, fine-grained products.
- Composite Materials: Effective for creating composites with enhanced properties.
- Nanomaterials: SPS is particularly useful for preparing nanomaterials, preserving their refined microstructures.
- Bulk Amorphous Alloys and Gradient Functional Materials: These advanced materials benefit from the precise control and rapid processing of SPS.
-
Benefits for Polymer Sintering:
- Preservation of Microstructure: SPS allows for the consolidation of polymer powders at lower temperatures and shorter times, maintaining the microstructure achieved through processes like cryogenic milling.
- Enhanced Mechanical Properties: The uniform grain structure and high density achieved through SPS result in polymers with improved mechanical strength and durability.
-
Comparison with Traditional Sintering Methods:
- Time Efficiency: SPS significantly reduces sintering time, making it more efficient for large-scale production.
- Energy Savings: Lower operating temperatures and shorter processing times lead to reduced energy consumption.
- Material Quality: The fine, uniform grain structure and high density of SPS-sintered materials often surpass those produced by traditional methods.
In summary, spark plasma sintering is a highly efficient and effective method for sintering polymers and other materials, offering numerous advantages over traditional techniques. Its ability to produce high-quality materials with enhanced properties makes it a valuable tool in material science and industrial applications.
Summary Table:
Aspect | Details |
---|---|
What is SPS? | Combines plasma activation, hot pressing, and resistance heating for rapid sintering. |
Advantages | Fast heating, lower temperatures, uniform heating, energy efficiency, improved properties. |
Mechanisms | Joule heating, plastic deformation, discharge between particles. |
Applications | Metals, ceramics, composites, nanomaterials, bulk amorphous alloys. |
Polymer Benefits | Preserves microstructure, enhances mechanical properties. |
vs. Traditional Methods | Faster, energy-efficient, superior material quality. |
Learn how spark plasma sintering can revolutionize your material production—contact us today!