Surface sputtering is a process where ions or neutral particles bombard a solid target material, causing atoms or molecules near the surface to gain enough energy to escape. These ejected particles then deposit onto a substrate, forming a thin film. This technique is widely used in industries such as semiconductors, optics, and aerospace for applications like thin film deposition, surface cleaning, and material analysis. It operates under vacuum conditions, ensuring precision and purity in the coatings produced.
Key Points Explained:
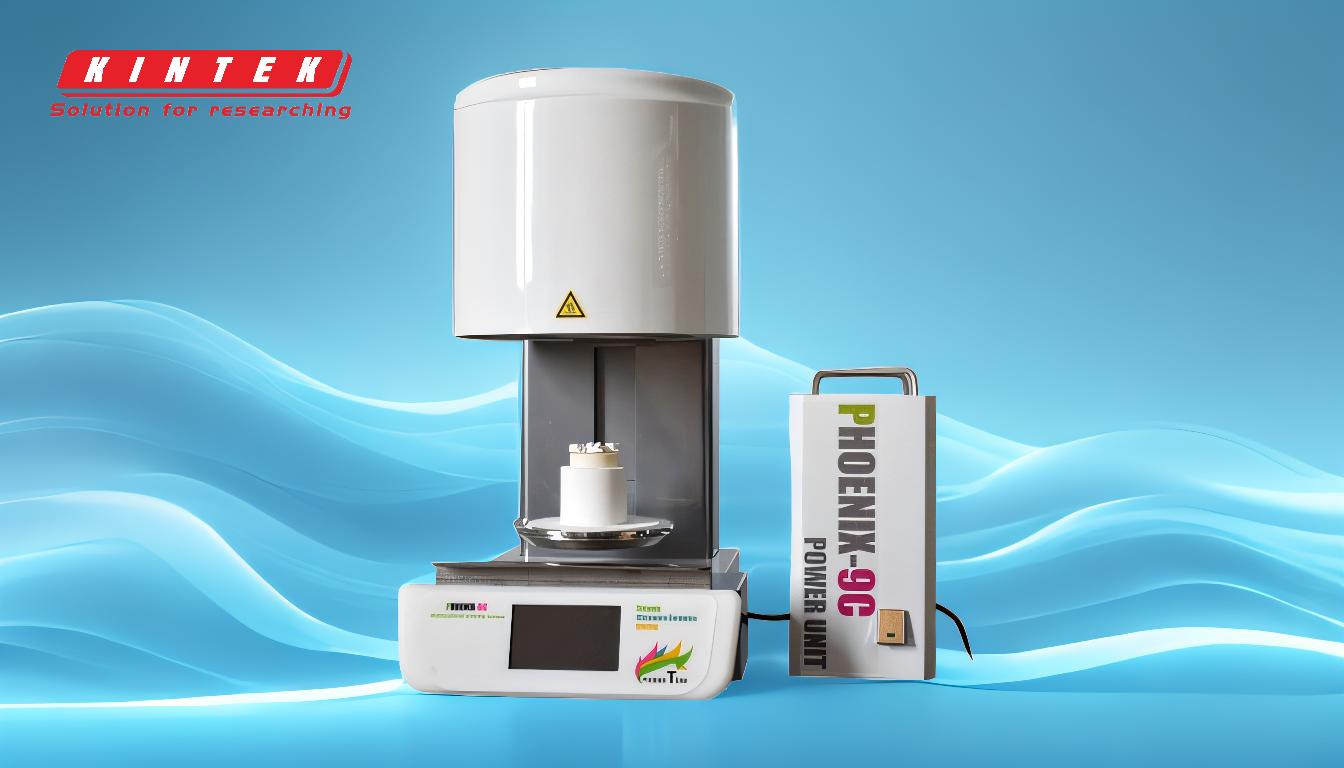
-
Definition of Surface Sputtering:
- Surface sputtering involves bombarding a solid target with ions or neutral particles, causing atoms or molecules near the surface to escape due to energy transfer.
- The ejected material, typically in the form of neutral particles, travels through a vacuum and deposits onto a substrate, forming a thin film.
-
Mechanism of Sputtering:
- The process begins with the acceleration of ions (often from inert gases like argon) toward a target material.
- Upon impact, the ions transfer energy to the target's surface atoms, causing them to dislodge.
- The ejected atoms or molecules traverse the vacuum chamber and deposit onto a substrate, creating a thin film.
-
Applications of Sputtering:
- Semiconductor Industry: Used for depositing thin films of materials in integrated circuit fabrication.
- Optical Industry: Applied for creating antireflection coatings, polarization filters, and low-emissivity coatings on glass.
- Architectural Glass: Used for coating large-area surfaces to enhance durability and energy efficiency.
- Data Storage: Essential for depositing metal layers in CDs, DVDs, and hard disks.
- Aerospace and Defense: Used for applying gadolinium films in neutron radiography and creating corrosion-resistant coatings.
- Medical Devices: Produces dielectric stacks to electrically isolate surgical tools.
-
Advantages of Sputtering:
- Precision: Allows for the deposition of thin films with thicknesses ranging from nanometers to micrometers.
- Versatility: Can deposit a wide range of materials, including metals, alloys, and nitrides.
- Purity: Operates in a vacuum, minimizing contamination and ensuring high-quality coatings.
- Uniformity: Provides consistent and even coatings over large areas.
-
Vacuum Requirement:
- Sputtering must be performed under vacuum conditions to prevent interference from atmospheric gases and ensure the efficient transfer of particles from the target to the substrate.
-
Role in Advanced Materials:
- Sputtering is a key technique in developing advanced materials and coatings, enabling the creation of smaller, lighter, and more durable products. It plays a critical role in innovations across industries, from electronics to renewable energy.
-
Process Variations:
- Sputter Deposition: A specific application of sputtering used to create thin films on substrates.
- Surface Cleaning: Used in surface physics to prepare high-purity surfaces for analysis.
- Material Analysis: Helps in studying the chemical composition of surfaces.
By understanding these key points, one can appreciate the versatility and importance of surface sputtering in modern technology and industrial applications. Its ability to produce precise, high-quality coatings makes it indispensable in fields ranging from electronics to aerospace.
Summary Table:
Aspect | Details |
---|---|
Definition | Bombardment of a solid target with ions or neutral particles to eject atoms. |
Mechanism | Energy transfer from ions causes surface atoms to dislodge and deposit. |
Applications | Semiconductors, optics, aerospace, data storage, and medical devices. |
Advantages | Precision, versatility, purity, and uniformity in coatings. |
Vacuum Requirement | Operates under vacuum for contamination-free and efficient deposition. |
Learn how surface sputtering can enhance your projects—contact us today for expert guidance!