Chemical vapor deposition (CVD) is a highly versatile and efficient technique used to deposit thin films and coatings on a variety of substrates. Its advantages include the ability to work with a wide range of materials, such as ceramics, metals, and glass, and to produce coatings with tailored properties like corrosion resistance, abrasion resistance, and high purity. CVD is capable of creating durable, high-performance coatings that can withstand extreme temperatures and high-stress environments. It is also well-suited for coating complex and precision surfaces, ensuring uniform and high-quality results. Additionally, CVD is relatively affordable, scalable, and offers excellent control over film properties, making it ideal for applications in electronics, optics, and advanced materials.
Key Points Explained:
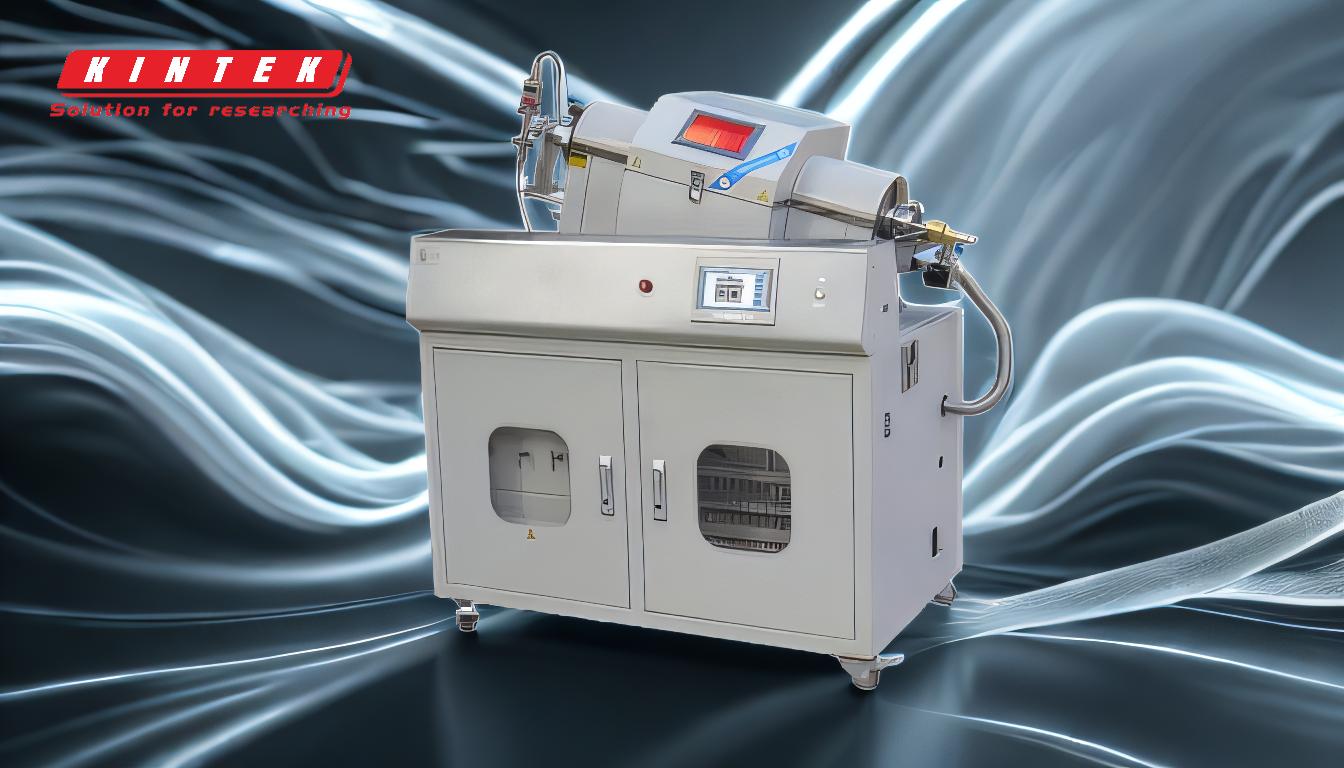
-
Versatility in Material Application
- CVD can be used on a wide range of materials, including ceramics, metals, and glass. This makes it a highly adaptable process for various industries, from electronics to aerospace.
- The ability to optimize gases for specific properties, such as corrosion resistance, abrasion resistance, or high purity, further enhances its versatility.
-
Durable and High-Performance Coatings
- CVD produces coatings that are highly durable and can withstand extreme conditions, such as high-stress environments and extreme temperature variations.
- The coatings are uniform and have excellent adhesion, ensuring long-lasting performance.
-
Precision and Complexity in Coating
- CVD is capable of coating complex and precision surfaces, making it ideal for applications requiring intricate designs or fine details.
- This is particularly useful in industries like microelectronics, where precision is critical.
-
Control Over Film Properties
- CVD allows for precise control over the properties of the deposited film, such as thickness, purity, and crystallinity.
- This control is achieved by adjusting deposition parameters, such as temperature, pressure, and gas composition.
-
High Purity and Uniformity
- The process produces high-purity films with excellent uniformity, which is essential for applications in semiconductors and optics.
- Compared to other deposition techniques, such as sputtering and evaporation, CVD offers superior purity and consistency.
-
Scalability and Affordability
- CVD is relatively affordable and can be easily scaled up for mass production, making it a cost-effective solution for industrial applications.
- Its non-line-of-sight nature ensures uniform coating even on large or complex surfaces.
-
Environmental Benefits
- CVD has a reduced CO2 footprint compared to other coating technologies, such as pitch coating, making it a more environmentally friendly option.
- It also produces smoother surfaces and better mixing compatibility with other materials, enhancing overall performance.
-
Ideal for Advanced Applications
- CVD is particularly well-suited for producing ultra-thin layers of materials, making it ideal for applications in electrical circuits and nanotechnology.
- Its ability to create high-performance coatings with tailored properties makes it a preferred choice for cutting-edge technologies.
For more advanced applications, techniques like microwave plasma chemical vapor deposition can further enhance the capabilities of CVD, offering even greater control and efficiency in film deposition.
In summary, chemical vapor deposition is a highly advantageous process due to its versatility, precision, control, and ability to produce high-quality coatings for a wide range of applications. Its scalability and environmental benefits further solidify its position as a leading deposition technology in modern industries.
Summary Table:
Advantage | Description |
---|---|
Versatility | Works with ceramics, metals, glass, and tailored properties like corrosion resistance. |
Durable Coatings | Withstands extreme temperatures and high-stress environments. |
Precision Coating | Ideal for complex and intricate surfaces, especially in microelectronics. |
Control Over Film Properties | Adjust thickness, purity, and crystallinity for tailored results. |
High Purity & Uniformity | Superior purity and consistency for semiconductors and optics. |
Scalability & Affordability | Cost-effective and scalable for mass production. |
Environmental Benefits | Reduced CO2 footprint and smoother surfaces compared to other techniques. |
Advanced Applications | Ideal for ultra-thin layers in electrical circuits and nanotechnology. |
Ready to enhance your materials with CVD? Contact our experts today to learn more!