Electric induction furnaces offer significant advantages over direct current electric arc furnaces (EAF) during cool start-up operations. These benefits stem from their design, operational efficiency, and environmental considerations. Induction furnaces are known for their energy efficiency, fast heating, precise temperature control, and clean melting process, which make them ideal for industrial applications. They eliminate the need for an arc or combustion, reducing contamination risks and ensuring a safer working environment. Additionally, their compact size, low power consumption, and ability to produce homogeneous metal mixtures further enhance their appeal. Below, the key advantages are explained in detail.
Key Points Explained:
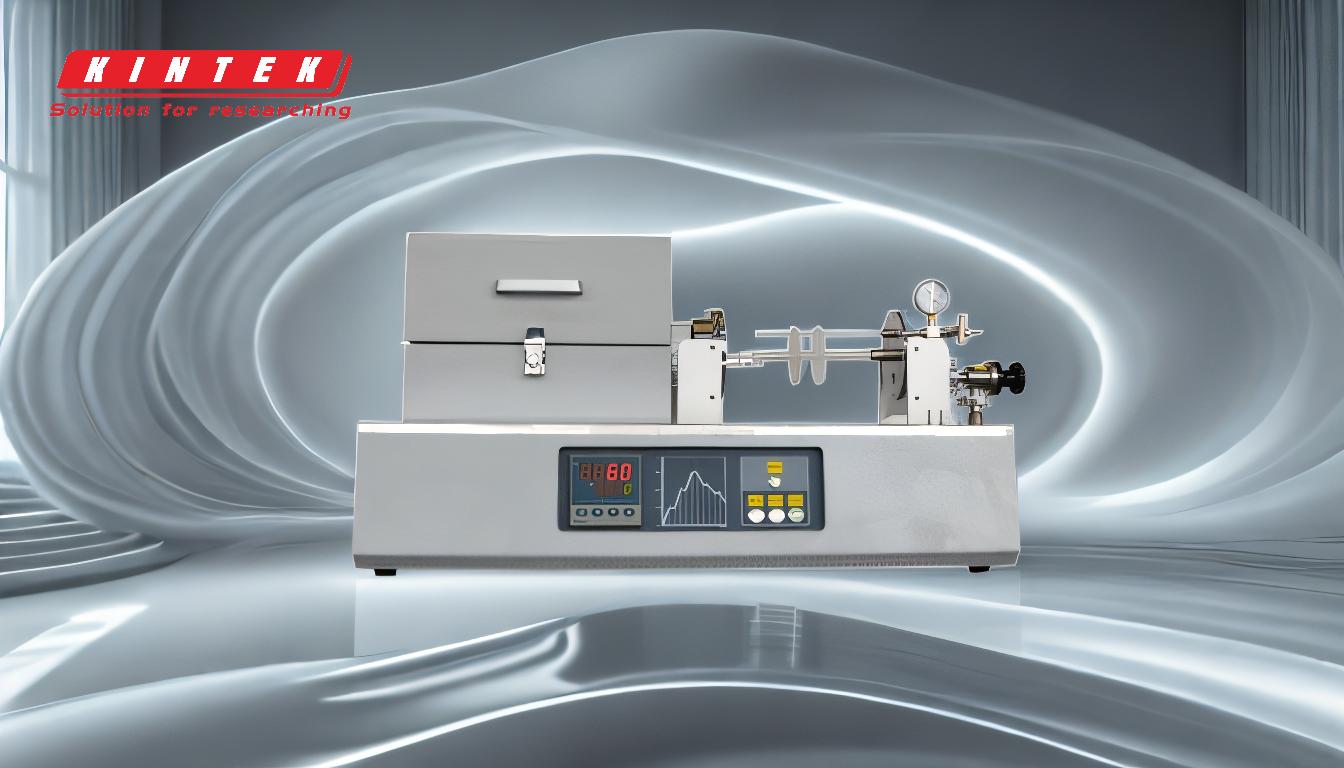
-
Energy Efficiency and Low Power Consumption:
- Induction furnaces are highly energy-efficient, converting electrical energy directly into heat within the metal charge. This minimizes energy losses and reduces power consumption compared to EAFs, which rely on arcs that can be less efficient during start-up.
- The absence of an arc or combustion in induction furnaces ensures that energy is used more effectively, making them suitable for continuous operations and reducing overall operational costs.
-
Fast Heating and High Production Efficiency:
- Induction furnaces heat metals rapidly due to the direct generation of heat within the metal charge. This results in shorter start-up times and faster melting cycles, which is particularly beneficial during cool start-up operations.
- The electromagnetic stirring action ensures uniform heating and mixing, leading to a homogeneous liquid metal mixture without the need for additional sampling or processing.
-
Precise Temperature Control:
- Induction furnaces provide superior temperature control, allowing for precise regulation of the melting process. This is crucial for preserving valuable alloying elements and achieving consistent metal quality.
- The absence of external heat sources reduces the risk of contamination and ensures that the temperature remains stable throughout the process.
-
Clean and Pollution-Free Operation:
- Induction furnaces do not produce dust, fumes, or other pollutants, making them environmentally friendly and safer for workers. This is a significant advantage over EAFs, which can generate harmful emissions during start-up.
- The lack of combustion or arc-related byproducts ensures a cleaner melting process, reducing the need for extensive filtration systems and minimizing environmental impact.
-
Compact Design and Ease of Operation:
- Induction furnaces are smaller and lighter than EAFs, making them easier to install and operate in confined spaces. This is particularly advantageous for facilities with limited space or those looking to upgrade existing equipment.
- The simplicity of operation and low maintenance requirements further enhance their appeal, especially during cool start-up operations where reliability is critical.
-
Uniform Temperature Distribution and Magnetic Stirring:
- The magnetic stirring action in induction furnaces ensures uniform temperature distribution and composition homogeneity, eliminating the need for additional mixing or sampling. This results in higher-quality metal products and reduces processing time.
- The small temperature difference between the core and surface of the metal charge ensures consistent melting and minimizes thermal stress on the materials.
-
Cost Savings and Environmental Benefits:
- Induction furnaces save material and operational costs by reducing oxidation, decarburization, and waste. Their energy-efficient design also contributes to lower electricity bills and a reduced carbon footprint.
- The ability to operate continuously for 24 hours without significant downtime makes them a cost-effective solution for industrial applications.
-
Versatility in Melting Conditions:
- Induction furnaces can operate under specific conditions, such as acidic, neutral, or near-vacuum environments, which are essential for producing high-quality alloys. This versatility is not typically available in EAFs.
- The absence of an electric arc allows for the production of alloys with low carbon content and minimal impurities, making induction furnaces ideal for specialized applications.
In summary, electric induction furnaces outshine direct current EAFs during cool start-up operations due to their energy efficiency, fast heating, precise control, and environmental benefits. Their compact design, ease of operation, and ability to produce high-quality metal products make them a preferred choice for modern industrial settings.
Summary Table:
Advantage | Description |
---|---|
Energy Efficiency | Converts electrical energy directly into heat, reducing power consumption. |
Fast Heating | Rapid heating and shorter start-up times for efficient operations. |
Precise Temperature Control | Ensures stable melting and preserves alloying elements. |
Clean Operation | No dust, fumes, or pollutants, ensuring a safer and eco-friendly process. |
Compact Design | Smaller and lighter, ideal for confined spaces and easy operation. |
Uniform Temperature Distribution | Magnetic stirring ensures homogeneous mixing and consistent melting. |
Cost Savings | Reduces material waste, oxidation, and operational costs. |
Versatility | Operates in acidic, neutral, or near-vacuum conditions for specialized alloys. |
Upgrade your industrial operations with electric induction furnaces—contact us today to learn more!