Induction furnaces offer several advantages over electric arc furnaces, making them a preferred choice in many industrial applications. They are known for their efficiency, ease of temperature control, and environmentally friendly operation. Induction furnaces are smaller, lighter, and consume less power while providing faster melting and heating capabilities. They also ensure a cleaner melting process with minimal waste and pollutants, making them suitable for preserving valuable alloying elements and reducing the carbon footprint. These features make induction furnaces a modern, efficient, and sustainable alternative to traditional electric arc furnaces.
Key Points Explained:
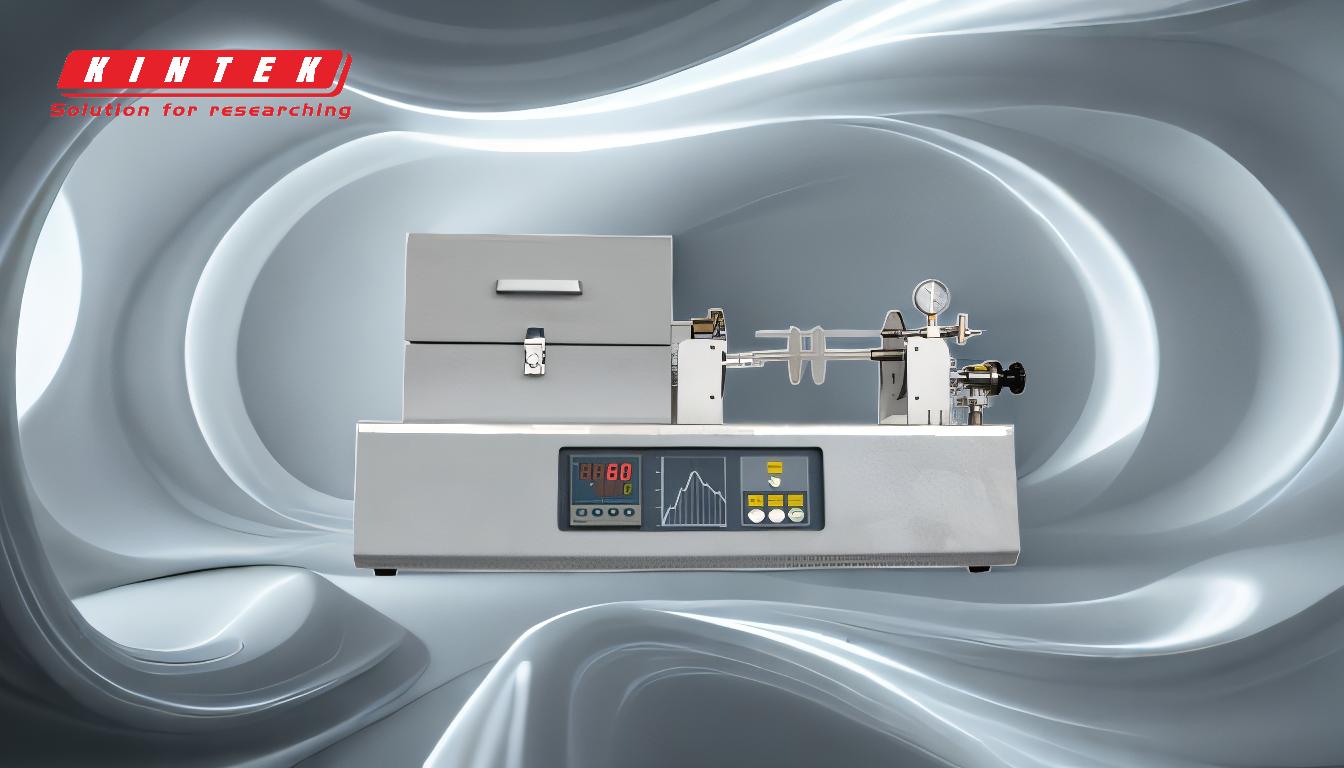
-
Efficiency and Power Consumption:
- Induction furnaces, particularly those using IGBT technology, are highly efficient and consume less power compared to electric arc furnaces. This results in lower operational costs and energy savings.
- The fast melting and heating capabilities of induction furnaces further enhance their efficiency, allowing for quicker production cycles.
-
Temperature Control:
- Induction furnaces provide precise and easy control over furnace temperature, which is crucial for maintaining the quality of the melted metal and preserving valuable alloying elements.
- This level of control is often harder to achieve in electric arc furnaces, where temperature fluctuations can affect the final product.
-
Environmental Benefits:
- Induction furnaces generate minimal waste and pollutants, such as dust and harmful emissions, making them a cleaner and safer option for metal melting.
- This reduction in pollutants contributes to a lower carbon footprint, aligning with modern environmental regulations and sustainability goals.
-
Size and Weight:
- Induction furnaces are generally smaller and lighter than electric arc furnaces, making them easier to install and operate in limited spaces.
- Their compact design also reduces the need for extensive infrastructure, lowering initial setup costs.
-
Cleaner Melting Process:
- The induction melting process is cleaner and more controlled, ensuring higher-quality output with fewer impurities.
- This has led many older iron foundries to replace traditional cupolas with induction furnaces, as they offer a more modern and efficient solution.
-
Preservation of Alloying Elements:
- The controlled melting process of induction furnaces helps preserve valuable alloying elements, which might otherwise be lost or degraded in less precise melting methods.
- This is particularly important in industries where the quality and composition of the final product are critical.
In summary, induction furnaces outperform electric arc furnaces in terms of efficiency, environmental impact, and operational control. Their advanced technology, such as IGBT induction furnaces, makes them a superior choice for modern metal melting applications.
Summary Table:
Advantage | Induction Furnace | Electric Arc Furnace |
---|---|---|
Efficiency | High efficiency with lower power consumption and faster melting/heating capabilities. | Less efficient, higher power consumption, and slower melting/heating. |
Temperature Control | Precise and easy control, ensuring quality and preserving alloying elements. | Harder to control, prone to temperature fluctuations affecting output quality. |
Environmental Impact | Minimal waste, fewer pollutants, and reduced carbon footprint. | Generates more waste and pollutants, contributing to a higher carbon footprint. |
Size and Weight | Compact, lightweight, and easier to install in limited spaces. | Larger, heavier, and requires more infrastructure for installation. |
Melting Process | Cleaner and more controlled, resulting in higher-quality output with fewer impurities. | Less controlled, leading to more impurities and lower-quality output. |
Preservation of Alloys | Preserves valuable alloying elements effectively. | Higher risk of losing or degrading alloying elements during melting. |
Ready to upgrade your metal melting process? Contact us today to explore the benefits of induction furnaces!