The sputtering technique is a versatile and widely used method in various industries, primarily for depositing thin films and coatings on substrates. It involves bombarding a target material with high-energy particles, causing atoms to be ejected and deposited onto a substrate, forming a thin film. This process is critical in industries such as consumer electronics, optics, semiconductors, and aerospace, where precision, durability, and performance are paramount. Sputtering is employed in applications ranging from creating anti-reflective coatings for optical lenses to depositing thin films for semiconductor devices, making it an indispensable tool in modern manufacturing and research.
Key Points Explained:
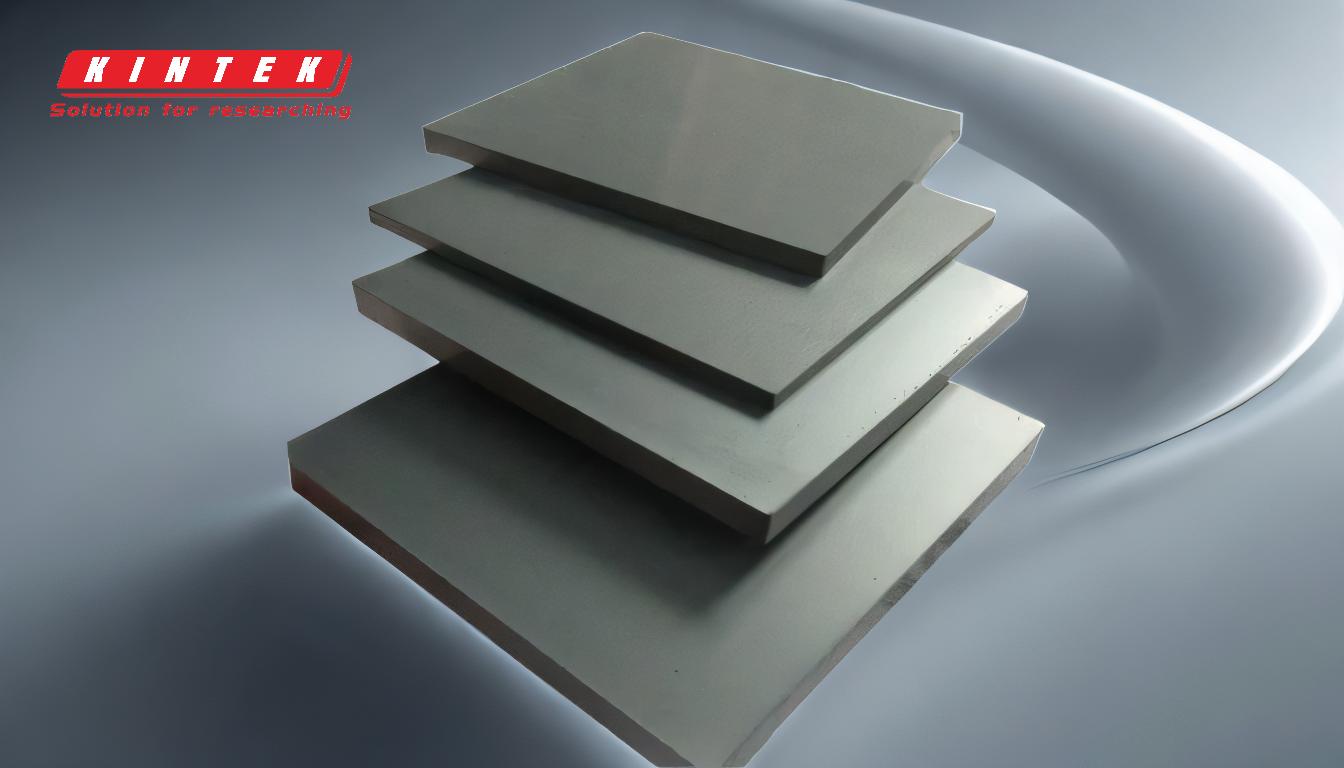
-
Consumer Electronics:
- Application: Sputtering is extensively used in the production of CDs, DVDs, LED displays, and magnetic storage devices like hard and floppy disks.
- Explanation: The technique allows for the precise deposition of thin metal layers, which are essential for data storage and display technologies. For example, the reflective layers in CDs and DVDs are created using sputtering, enabling the storage and retrieval of digital information.
-
Optics:
- Application: Sputtering is used to create optical filters, precision optics, laser lenses, and anti-reflective coatings.
- Explanation: In the optics industry, sputtering is employed to deposit thin films that enhance the performance of optical components. Anti-reflective coatings, for instance, reduce glare and improve light transmission, making them essential for lenses used in cameras, microscopes, and eyeglasses.
-
Semiconductor Industry:
- Application: Sputtering is crucial for depositing thin films of various materials in integrated circuit processing.
- Explanation: The semiconductor industry relies on sputtering to create the intricate layers of materials needed for the fabrication of microchips and other electronic components. This includes the deposition of conductive metals, insulating layers, and barrier materials that are essential for the functionality of semiconductor devices.
-
Architectural Glass:
- Application: Sputtering is used to apply low-emissivity coatings on double-pane windows and other large-area surfaces.
- Explanation: Low-emissivity coatings, created through sputtering, improve the energy efficiency of buildings by reducing heat transfer through windows. This application is particularly important in the construction industry, where energy conservation is a key concern.
-
Aerospace and Defense:
- Application: Sputtering is used to apply gadolinium films for neutron radiography and to create gas-impermeable films for corrosion protection.
- Explanation: In aerospace and defense, sputtering is employed to produce coatings that protect materials from harsh environments and enhance their performance. Gadolinium films, for example, are used in neutron radiography to detect flaws in critical components, while gas-impermeable films prevent corrosion in metal parts.
-
Medical Devices:
- Application: Sputtering is used to produce dielectric stacks for electrically isolating surgical tools.
- Explanation: In the medical field, sputtering is utilized to create coatings that improve the performance and safety of surgical instruments. Dielectric stacks, for instance, provide electrical insulation, preventing short circuits and ensuring the reliability of medical devices.
-
Photovoltaic Solar Cells:
- Application: Sputtering is employed in the manufacturing of photovoltaic solar cells.
- Explanation: The technique is used to deposit thin films of materials that convert sunlight into electricity. This application is critical in the renewable energy sector, where sputtering helps to improve the efficiency and durability of solar panels.
-
Surface Physics and Analysis:
- Application: Sputtering is used as a cleaning method for preparing high-purity surfaces and for analyzing the chemical composition of surfaces.
- Explanation: In surface physics, sputtering is employed to remove contaminants from surfaces, ensuring high-purity conditions for experiments. Additionally, it is used in analytical techniques to study the composition and properties of materials at the atomic level.
-
Tool Coating:
- Application: Sputtering is used to coat tool bits with nitrides and other hard materials.
- Explanation: In the manufacturing industry, sputtering is applied to enhance the durability and performance of cutting tools. Nitride coatings, for example, increase the hardness and wear resistance of tool bits, extending their lifespan and improving machining efficiency.
-
Advanced Materials and Coatings:
- Application: Sputtering is a key technique for developing advanced materials and coatings.
- Explanation: Researchers and engineers use sputtering to create innovative materials with unique properties, such as enhanced strength, conductivity, or optical characteristics. This application is crucial for the development of new technologies and products across various industries.
In summary, the sputtering technique is a fundamental process with a wide range of applications across multiple industries. Its ability to deposit thin films with high precision and uniformity makes it an essential tool for advancing technology and improving the performance of various products.
Summary Table:
Industry | Applications | Key Benefits |
---|---|---|
Consumer Electronics | CDs, DVDs, LED displays, magnetic storage devices | Precise deposition of thin metal layers for data storage and display technologies |
Optics | Optical filters, anti-reflective coatings, precision optics | Enhanced performance of optical components, reduced glare, improved light transmission |
Semiconductors | Integrated circuit processing, microchip fabrication | Deposition of conductive metals, insulating layers, and barrier materials |
Architectural Glass | Low-emissivity coatings for energy-efficient windows | Improved energy efficiency in buildings |
Aerospace & Defense | Gadolinium films for neutron radiography, corrosion protection | Protection from harsh environments, enhanced material performance |
Medical Devices | Dielectric stacks for surgical tools | Electrical insulation, improved safety and reliability |
Solar Cells | Photovoltaic solar cell manufacturing | Enhanced efficiency and durability of solar panels |
Surface Physics | High-purity surface preparation, chemical composition analysis | Contaminant removal, atomic-level material analysis |
Tool Coating | Nitride coatings for cutting tools | Increased hardness, wear resistance, and tool lifespan |
Advanced Materials | Development of innovative materials with unique properties | Enhanced strength, conductivity, and optical characteristics |
Unlock the potential of sputtering for your industry—contact our experts today to learn more!