The atmosphere of a furnace refers to the controlled environment inside the furnace chamber, which plays a critical role in heat treatment processes. It is designed to optimize the conditions for metal components by regulating gas composition, temperature, and pressure. This controlled atmosphere prevents oxidation, decarburization, and contamination, ensuring high-quality and consistent results. Furnaces can operate under various atmospheres, including inert gases, vacuum, or reactive gases, depending on the specific requirements of the process. Proper maintenance, such as keeping the furnace clean and using appropriate sealing mechanisms, is essential to maintain the integrity of the atmosphere and ensure safety and efficiency.
Key Points Explained:
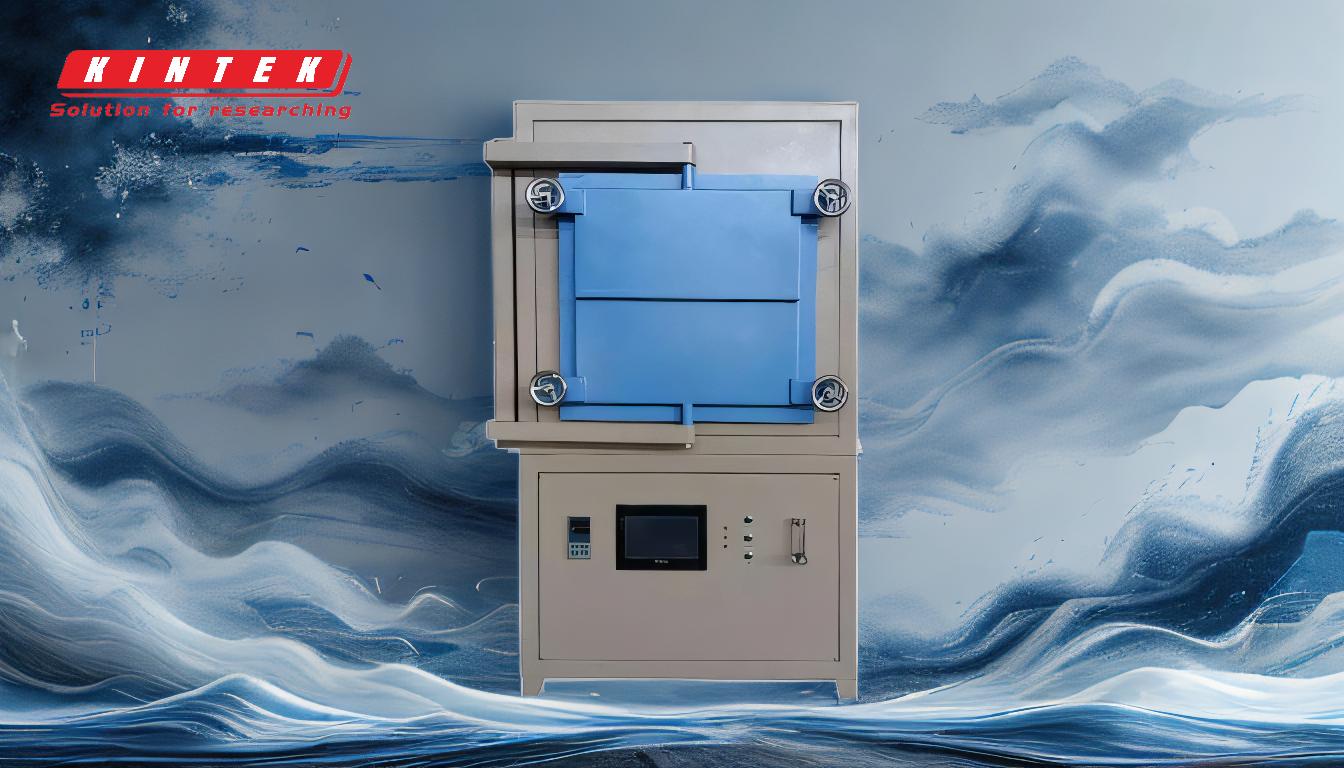
-
Purpose of a Controlled Atmosphere:
- The atmosphere in a furnace is crucial for heat treatment processes, as it directly impacts the quality of the metal components being treated.
- By controlling the gas composition and flow, the furnace minimizes oxidation and decarburization, which can degrade the material's properties.
- A well-regulated atmosphere ensures consistent results, improved product quality, and enhanced production efficiency.
-
Types of Furnace Atmospheres:
- Inert Atmospheres: These include gases like nitrogen or argon, which are non-reactive and prevent oxidation or contamination of the metal.
- Vacuum Atmospheres: A vacuum environment eliminates air and gases, reducing the risk of oxidation and contamination. This is particularly useful for sensitive materials.
- Reactive Atmospheres: Certain processes may require reactive gases like hydrogen or carbon monoxide to achieve specific chemical reactions or surface modifications.
-
Components of a Controlled Atmosphere System:
- Gas Flow Control: Precise regulation of gas flow ensures the desired atmosphere is maintained throughout the process.
- Sealing Mechanisms: High-quality sealing components, such as stainless steel flanges, prevent leaks and maintain the integrity of the atmosphere.
- Working Tubes: Materials like quartz glass, metal, or corundum are used for working tubes, depending on the specific requirements of the process.
-
Importance of Cleanliness:
- Keeping the furnace clean is essential to prevent contamination, which can compromise the quality of the heat treatment.
- Regular maintenance ensures the efficient operation of the vacuum pump and reduces the risk of safety hazards like fires or explosions.
-
Applications of Controlled Atmosphere Furnaces:
- These furnaces are widely used in industries such as aerospace, automotive, and manufacturing, where precise control over material properties is critical.
- They are particularly beneficial for processes like annealing, brazing, sintering, and hardening, where maintaining a specific atmosphere is essential for achieving the desired results.
-
Design Considerations:
- Furnaces like chamber furnaces are designed for compactness and ease of access, with features such as side doors for quick loading and unloading.
- The choice of materials and components, such as sealing flanges and working tubes, is tailored to the specific requirements of the process and the materials being treated.
By understanding and optimizing the furnace atmosphere, manufacturers can achieve superior results in heat treatment processes, ensuring the durability, performance, and consistency of their products.
Summary Table:
Aspect | Details |
---|---|
Purpose | Prevents oxidation, decarburization, and contamination during heat treatment. |
Types of Atmospheres | Inert (e.g., nitrogen, argon), vacuum, and reactive (e.g., hydrogen, CO). |
Key Components | Gas flow control, sealing mechanisms, and working tubes (quartz, metal). |
Applications | Aerospace, automotive, and manufacturing industries. |
Maintenance | Regular cleaning and sealing to ensure safety and efficiency. |
Discover how a controlled furnace atmosphere can enhance your heat treatment processes—contact us today for expert guidance!