The atmosphere in a heat treatment furnace is a critical factor that influences the quality and properties of the treated materials. It can be chemically inert, protecting the material from surface reactions like oxidation and decarburization, or chemically reactive, enabling surface changes such as carburization or nitriding. Controlled atmospheres are designed to prevent unwanted chemical reactions, ensuring the material retains its desired properties. Vacuum furnaces, for instance, offer advantages like high thermal efficiency, no oxidation, and a bright surface finish, making them ideal for precise heat treatment processes. Understanding the atmosphere's role helps in selecting the right furnace and optimizing the heat treatment process for better outcomes.
Key Points Explained:
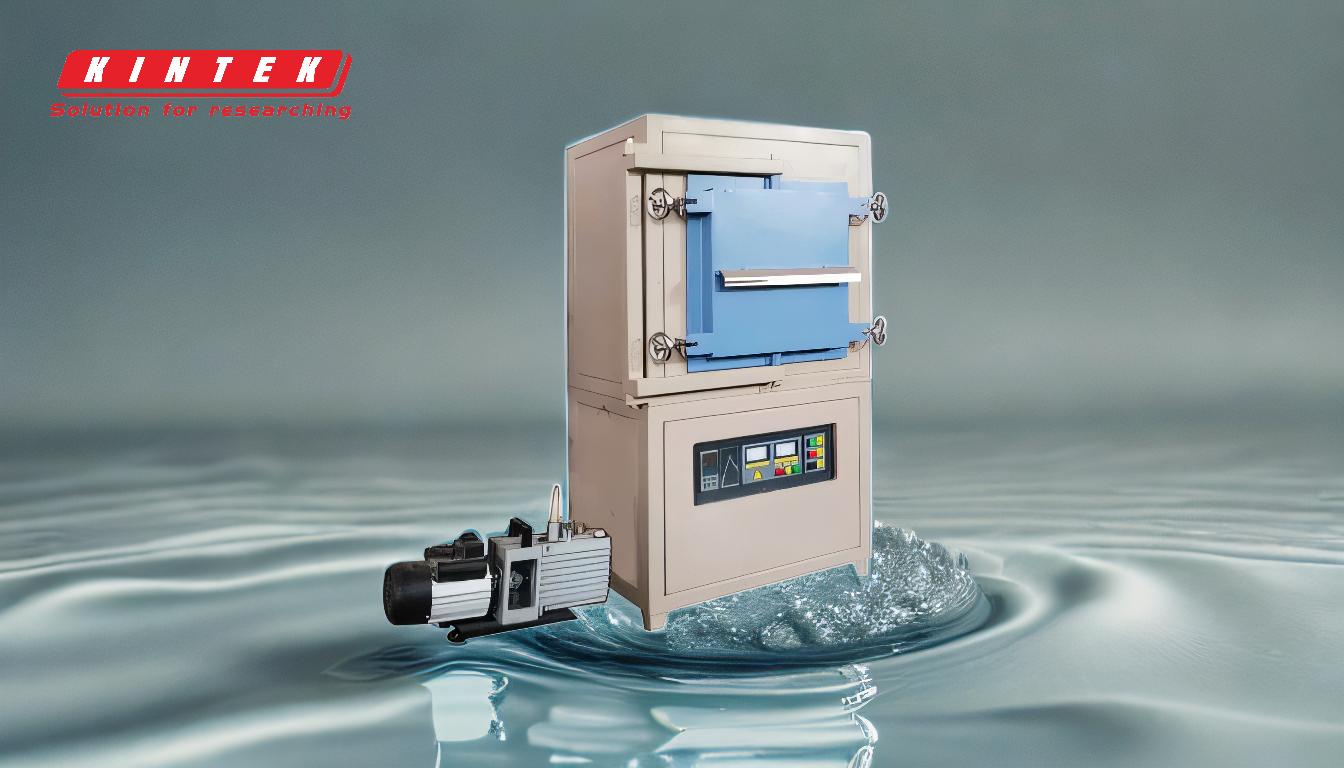
-
Purpose of Controlled Atmosphere in Heat Treatment:
- The primary purpose of a controlled atmosphere in a heat treatment furnace is to prevent oxidation and decarburization of steel workpieces. Oxidation leads to surface scaling, while decarburization reduces the carbon content on the surface, weakening the material.
- By controlling the levels of oxygen (O2), carbon monoxide (CO), and water vapor, the furnace atmosphere ensures the workpiece remains free from these defects, maintaining its mechanical properties and surface integrity.
-
Types of Furnace Atmospheres:
- Inert Atmospheres: These are chemically non-reactive and protect the material from surface reactions. Examples include nitrogen (N2) and argon (Ar). They are used when the goal is to prevent oxidation or other unwanted chemical changes.
- Reactive Atmospheres: These are chemically active and are used to induce specific surface changes. For example, carburizing atmospheres introduce carbon into the surface of the material, while nitriding atmospheres introduce nitrogen.
- Vacuum Atmospheres: Vacuum furnaces operate in a low-pressure environment, eliminating the presence of reactive gases. This prevents oxidation and decarburization, resulting in a bright, clean surface finish.
-
Advantages of Vacuum Furnaces:
- High Thermal Efficiency: Vacuum furnaces heat up and cool down rapidly, reducing cycle times and energy consumption.
- No Oxidation or Decarburization: The absence of oxygen and other reactive gases ensures the material remains pristine.
- Bright Surface Finish: The vacuum environment results in a clean, polished surface without the need for additional finishing processes.
- Improved Mechanical Properties: The controlled environment enhances the material's strength, durability, and service life.
- Environmental Safety: Vacuum furnaces produce no harmful emissions, making them environmentally friendly.
-
Role of Atmosphere in Material Properties:
- The furnace atmosphere directly impacts the material's surface and subsurface properties. For example, a carburizing atmosphere increases surface hardness, while a nitriding atmosphere improves wear resistance.
- Proper control of the atmosphere ensures consistent results, reducing defects and improving the overall quality of the treated components.
-
Economic and Operational Benefits:
- Using the right furnace atmosphere reduces material wastage, lowers manufacturing costs, and improves production efficiency.
- Vacuum furnaces, in particular, offer high product pass rates and reduced thermal stress, minimizing deformation and rework.
-
Applications of Controlled Atmospheres:
- Controlled atmospheres are used in various heat treatment processes, including annealing, hardening, tempering, and case hardening.
- They are essential in industries like aerospace, automotive, and tool manufacturing, where material properties and surface quality are critical.
By understanding the role of the furnace atmosphere, manufacturers can optimize their heat treatment processes, ensuring high-quality results while minimizing costs and environmental impact.
Summary Table:
Aspect | Details |
---|---|
Purpose | Prevent oxidation, decarburization, and ensure material integrity. |
Types of Atmospheres | Inert (e.g., N2, Ar), Reactive (e.g., carburizing, nitriding), Vacuum. |
Vacuum Furnace Benefits | High thermal efficiency, no oxidation, bright finish, improved properties. |
Applications | Annealing, hardening, tempering, case hardening in aerospace, automotive. |
Optimize your heat treatment process with the right furnace atmosphere—contact our experts today for tailored solutions!