Atomic Layer Deposition (ALD) is a highly precise and controlled thin-film deposition technique used to create ultra-thin, uniform, and conformal layers of material at the atomic scale. It operates through a cyclic process involving sequential exposure of a substrate to two or more gas-phase precursors, which react with the surface in self-limiting reactions. This ensures precise control over film thickness, density, and conformality, making ALD ideal for applications requiring nanometer-scale accuracy, such as semiconductor manufacturing, coatings, and nanotechnology. The process is characterized by its ability to produce highly uniform films even on complex 3D structures, with excellent step coverage and repeatability.
Key Points Explained:
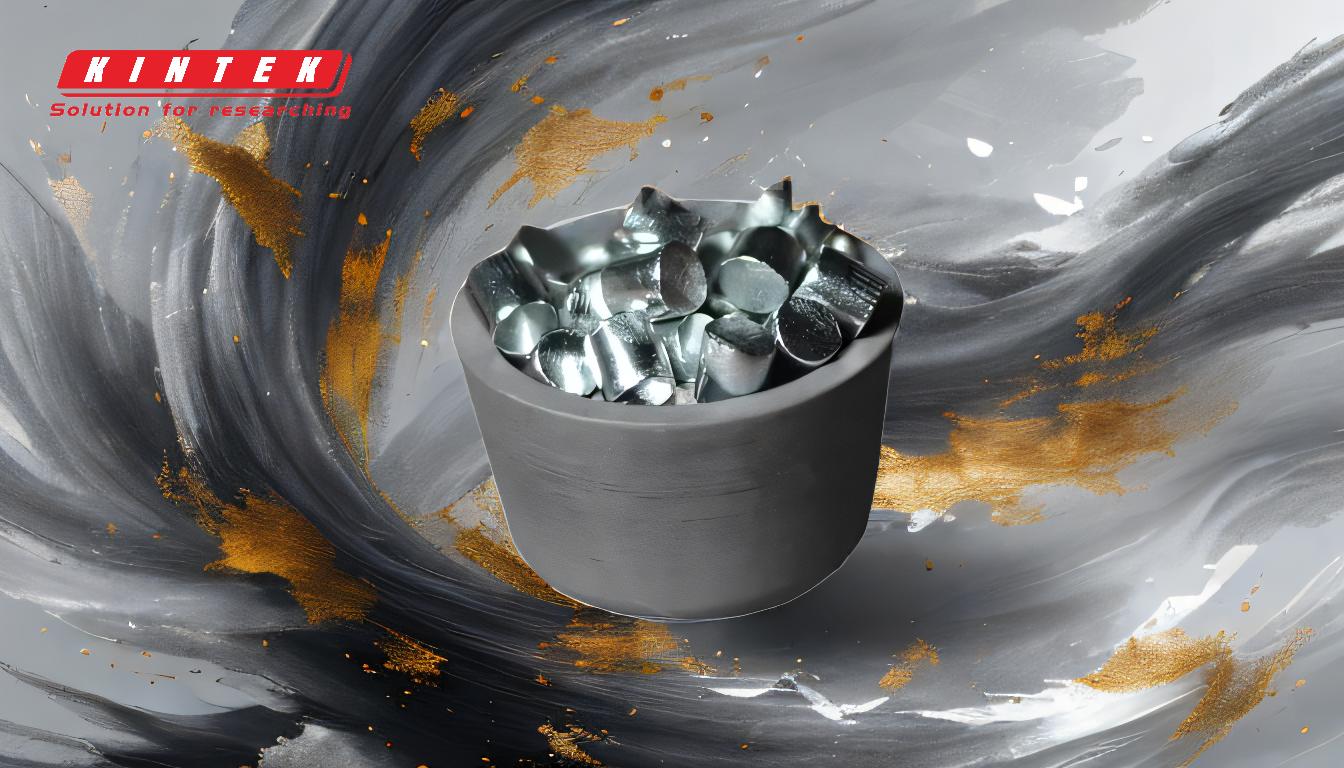
-
Sequential Deposition Process:
- ALD relies on a cyclic process where two or more precursors are introduced into the reaction chamber sequentially.
- The first precursor adsorbs onto the substrate surface, forming a chemically bound monolayer.
- The second precursor is then introduced, reacting with the first precursor to form a thin film layer.
- This cycle is repeated until the desired film thickness is achieved, with each cycle adding a layer of just a few angstroms in thickness.
-
Self-Limiting Reactions:
- The reactions in ALD are self-limiting, meaning the precursor molecules react only with the active sites on the substrate surface.
- Once all active sites are occupied, the reaction stops, ensuring precise control over film thickness and uniformity.
- This self-limiting nature eliminates the risk of over-deposition and ensures consistent results across multiple cycles.
-
Purging and By-Product Removal:
- After each precursor exposure, the reaction chamber is purged with an inert gas to remove any excess precursor and volatile reaction by-products.
- This step is critical to prevent unwanted chemical reactions and ensure the purity of the deposited film.
- The purge step also allows for precise control over the reaction environment, contributing to the high quality of the final film.
-
High Precision and Uniformity:
- ALD is renowned for its ability to produce films with atomic-level precision and uniformity.
- The process can achieve film thicknesses as low as a few nanometers, with excellent conformality even on complex 3D structures.
- This makes ALD particularly suitable for applications requiring high aspect ratios and step coverage, such as in microelectronics and nanotechnology.
-
Controlled Temperature and Environment:
- ALD is performed in a controlled temperature range to optimize the reactivity of the precursors and the quality of the deposited film.
- The reaction chamber is maintained under precise conditions to ensure consistent and repeatable results.
- Temperature control is critical for achieving the desired film properties, such as density, adhesion, and chemical composition.
-
Applications of ALD:
- ALD is widely used in semiconductor manufacturing for depositing high-k dielectrics, gate oxides, and diffusion barriers.
- It is also employed in the production of coatings for optical devices, sensors, and energy storage systems.
- The technique's ability to deposit ultra-thin, uniform films makes it ideal for advanced applications in nanotechnology, such as quantum dots and nanowires.
-
Advantages Over Other Deposition Techniques:
- Compared to traditional Chemical Vapor Deposition (CVD), ALD offers superior control over film thickness and conformality.
- The self-limiting nature of ALD reactions ensures excellent step coverage and uniformity, even on high-aspect-ratio structures.
- ALD can produce films with fewer defects and higher purity, making it suitable for high-performance applications.
-
Challenges and Limitations:
- ALD is a relatively slow process due to its cyclic nature, which can limit throughput in high-volume manufacturing.
- The need for precise control over temperature, pressure, and precursor delivery adds complexity to the process.
- The cost of ALD equipment and precursors can be higher compared to other deposition techniques, making it less suitable for cost-sensitive applications.
By combining these key points, ALD emerges as a powerful and versatile technique for depositing ultra-thin, high-quality films with unparalleled precision and uniformity. Its unique process characteristics make it indispensable in advanced manufacturing and research applications.
Summary Table:
Key Aspect | Details |
---|---|
Process | Cyclic, sequential exposure to gas-phase precursors. |
Self-Limiting Reactions | Ensures precise control over film thickness and uniformity. |
Purging | Removes excess precursors and by-products for high-purity films. |
Precision & Uniformity | Achieves nanometer-scale thickness and conformality on 3D structures. |
Applications | Semiconductors, coatings, sensors, nanotechnology, and energy storage. |
Advantages | Superior control, step coverage, and fewer defects compared to CVD. |
Challenges | Slower process, higher equipment and precursor costs. |
Learn how ALD can revolutionize your manufacturing process—contact our experts today!