The beam deposition process, specifically ion beam deposition (IBD) and electron beam deposition (E-Beam), is a sophisticated physical vapor deposition (PVD) technique used to create thin, precise coatings on substrates. In IBD, an ion beam sputters target material atoms, which then deposit onto a substrate. This process is highly controlled, with ions possessing equal energy, making it monoenergetic and collimated. E-Beam deposition, on the other hand, uses an electron beam to vaporize source materials in a vacuum chamber, with the vapor condensing onto the substrate to form coatings. Both methods are enhanced by precise control of parameters like vacuum levels, substrate positioning, and ion-assisted deposition, resulting in high-quality, durable coatings.
Key Points Explained:
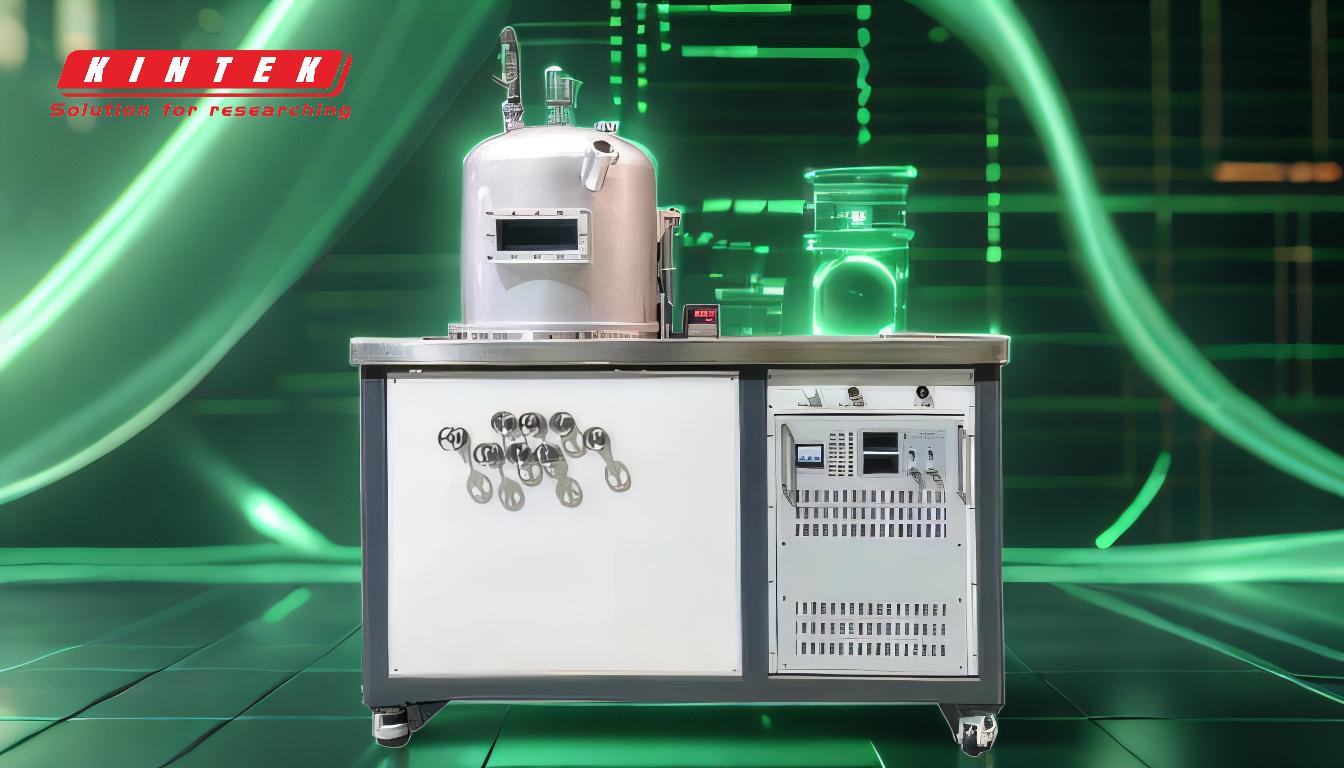
-
Ion Beam Deposition (IBD):
- Process Overview: IBD involves using an ion beam to sputter atoms from a target material, which then deposit onto a substrate. This method is highly controlled and precise.
- Components: A typical IBD system includes an ion source, a target material, and a substrate. Some systems may also include a second ion source for ion-assisted deposition.
- Advantages: The process is monoenergetic and highly collimated, ensuring uniformity and precision in the deposited layers. Ion-assisted deposition can enhance adhesion and coating density.
-
Electron Beam Deposition (E-Beam):
- Process Overview: E-Beam deposition uses an electron beam to vaporize source materials within a vacuum chamber. The vapor then condenses onto a substrate to form a thin coating.
- Components: The system includes an electron beam source, a crucible containing the material, and a substrate. The electron beam is generated by thermionic or field emission and is focused using magnetic fields.
- Advantages: E-Beam deposition allows for precise control over coating thickness and uniformity. The process can be enhanced with ion assistance to improve coating adhesion and density.
-
Key Differences Between IBD and E-Beam Deposition:
- Energy Source: IBD uses an ion beam, while E-Beam uses an electron beam.
- Material Interaction: In IBD, ions sputter the target material, whereas in E-Beam, the electron beam vaporizes the material.
- Control and Precision: Both methods offer high precision, but IBD is particularly noted for its monoenergetic and collimated ion beam, which ensures uniform deposition.
-
Applications of Beam Deposition:
- Optical Coatings: Both IBD and E-Beam are used to create precise optical coatings on lenses and mirrors.
- Semiconductor Manufacturing: These techniques are crucial for depositing thin films in semiconductor devices.
- Protective Coatings: Beam deposition is used to apply durable protective coatings on various materials, enhancing their resistance to wear and corrosion.
-
Enhancements and Control:
- Ion-Assisted Deposition: Using an ion beam to assist in the deposition process can significantly improve the adhesion and density of the coatings.
- Precision Control: Both methods benefit from advanced computer control systems that manage parameters like vacuum levels, substrate positioning, and rotation, ensuring high-quality coatings.
-
Material Considerations:
- Metals and Ceramics: Different materials behave differently under beam deposition. Metals like aluminum will melt and then evaporate, while ceramics will sublimate directly.
- Crucible Cooling: In E-Beam deposition, the crucible is often water-cooled to prevent it from heating up, ensuring that only the target material is vaporized.
-
Vacuum Environment:
- Importance of Vacuum: Both IBD and E-Beam processes require a high-vacuum environment to ensure that the vaporized material travels unimpeded to the substrate, resulting in a clean and uniform coating.
- Mean Free Path: The high mean free path in a vacuum ensures that most of the material is deposited on the substrate, minimizing waste and improving efficiency.
By understanding these key points, one can appreciate the complexity and precision involved in the beam deposition process, making it a valuable technique in various high-tech industries.
Summary Table:
Aspect | Ion Beam Deposition (IBD) | Electron Beam Deposition (E-Beam) |
---|---|---|
Energy Source | Ion beam | Electron beam |
Material Interaction | Ions sputter target material atoms | Electron beam vaporizes source material |
Precision | Monoenergetic, collimated, and highly uniform | Precise control over thickness and uniformity |
Applications | Optical coatings, semiconductor manufacturing, protective coatings | Optical coatings, semiconductor manufacturing, protective coatings |
Enhancements | Ion-assisted deposition improves adhesion and density | Ion assistance enhances coating adhesion and density |
Key Advantage | Uniform and precise deposition | High control over coating thickness |
Ready to explore how beam deposition can elevate your projects? Contact our experts today for tailored solutions!