The best catalyst for plastic pyrolysis depends on several factors, including the type of plastic being processed, the desired end products, and the specific operating conditions of the pyrolysis process. Catalysts play a crucial role in enhancing the quality and yield of pyrolysis products by reducing impurities and increasing the production of valuable hydrocarbons like C1, C2, and C3. Common catalysts used in plastic pyrolysis include zeolites, metal oxides, and mixed catalysts, each offering unique advantages depending on the feedstock and process requirements. The choice of catalyst should align with the specific goals of the pyrolysis process, such as maximizing oil yield or improving the quality of the end products.
Key Points Explained:
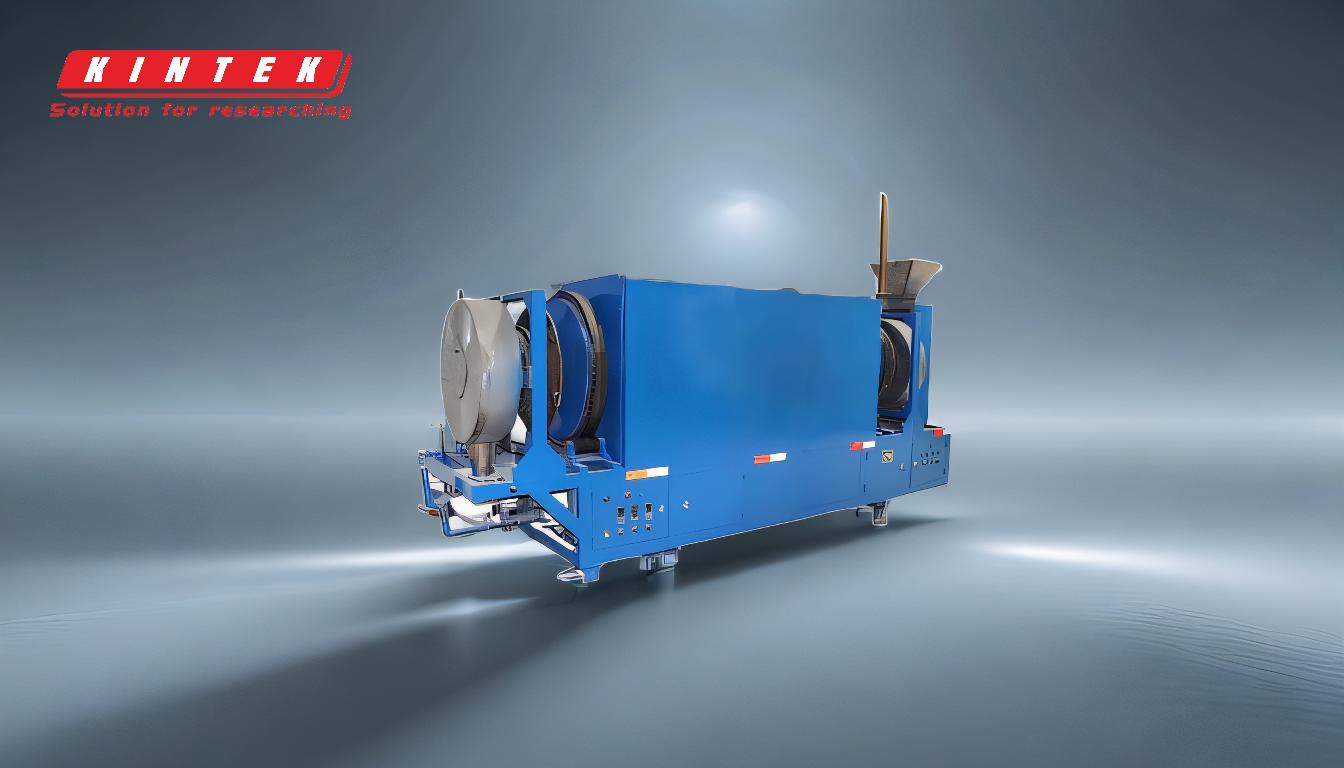
-
Role of Catalysts in Plastic Pyrolysis:
- Catalysts are essential in improving the efficiency and quality of plastic pyrolysis. They help break down complex polymers into simpler hydrocarbons, reduce oxygenates and impurities, and enhance the yield of valuable products like bio-oil and gases.
- For example, catalysts can increase the production of C1, C2, and C3 hydrocarbons, which are critical for creating drop-in fuels that are compatible with existing fuel infrastructure.
-
Types of Catalysts:
- Zeolites: Zeolites, such as ZSM-5, are widely used due to their high acidity and porous structure, which facilitate the cracking of large polymer molecules into smaller hydrocarbons. They are particularly effective for producing high-quality bio-oil.
- Metal Oxides: Catalysts like alumina (Al2O3) and silica-alumina (SiO2-Al2O3) are used for their ability to deoxygenate and reduce impurities in pyrolysis oil. They are often chosen for their stability and effectiveness at high temperatures.
- Mixed Catalysts: Combining different catalysts, such as zeolites with metal oxides, can optimize the pyrolysis process by leveraging the strengths of each component. This approach is useful for tailoring the process to specific feedstocks or desired end products.
-
Factors Influencing Catalyst Selection:
- Type of Plastic: Different plastics (e.g., polyethylene, polypropylene, polystyrene) require different catalysts due to variations in their chemical structure and degradation behavior.
- Desired End Products: The choice of catalyst depends on whether the goal is to maximize oil yield, produce high-quality gases, or reduce impurities. For instance, zeolites are preferred for producing high-quality oil, while metal oxides are better for gas production.
- Process Conditions: Temperature, pressure, and residence time significantly influence catalyst performance. For example, higher temperatures (e.g., 1000°C to 1220°C) can enhance the effectiveness of certain catalysts by improving degradation efficiency.
-
Impact of Operating Conditions:
- Temperature: Higher temperatures generally improve the efficiency of pyrolysis and catalyst performance. For example, temperatures above 1000°C can reduce COD and TOC levels in flue gases by up to 80-99%, depending on the catalyst used.
- Residence Time: Longer residence times allow for more complete degradation of plastics, which can enhance the effectiveness of the catalyst in producing high-quality products.
- Feedstock Quality: The quality of the plastic waste, including its moisture content, purity, and non-plastic content, affects the performance of the catalyst. Clean, dry, and pure plastics generally yield better results.
-
Technologies to Enhance Catalyst Performance:
- Pyrolysis Oil Purification: Technologies like Pyrolysis Oil Purification can help produce consistent oil quality despite variations in raw material quality. This is particularly useful when dealing with mixed or contaminated plastic waste.
- Catalyst Regeneration: Some catalysts can be regenerated and reused, which reduces costs and improves the sustainability of the pyrolysis process.
-
Practical Considerations for Equipment Purchasers:
- When selecting a catalyst for plastic pyrolysis, purchasers should consider the compatibility of the catalyst with their specific pyrolysis equipment and feedstock. They should also evaluate the cost, availability, and potential for catalyst regeneration.
- It is important to conduct pilot tests to determine the optimal catalyst and operating conditions for the specific type of plastic waste being processed.
By carefully considering these factors, purchasers can select the best catalyst for their plastic pyrolysis process, ensuring high-quality products and efficient operation.
Summary Table:
Factor | Details |
---|---|
Catalyst Types | Zeolites, Metal Oxides, Mixed Catalysts |
Key Role | Enhance product quality, reduce impurities, increase hydrocarbon production |
Plastic Types | Polyethylene, Polypropylene, Polystyrene |
Desired Products | Bio-oil, gases, or high-quality hydrocarbons |
Operating Conditions | Temperature, pressure, residence time |
Performance Enhancers | Pyrolysis oil purification, catalyst regeneration |
Ready to optimize your plastic pyrolysis process? Contact our experts today for tailored solutions!