When selecting the best media for a ball mill, the choice depends on the specific application, material properties, and desired outcomes. Ceramic balls are highly durable and minimize contamination, making them ideal for high-purity applications. Steel balls, on the other hand, are robust and better suited for heavy-duty milling tasks, especially when dealing with hard materials. Flint pebbles and stainless steel balls are also viable options, each offering unique advantages depending on the milling requirements. Understanding the properties and benefits of each media type is crucial for optimizing the milling process.
Key Points Explained:
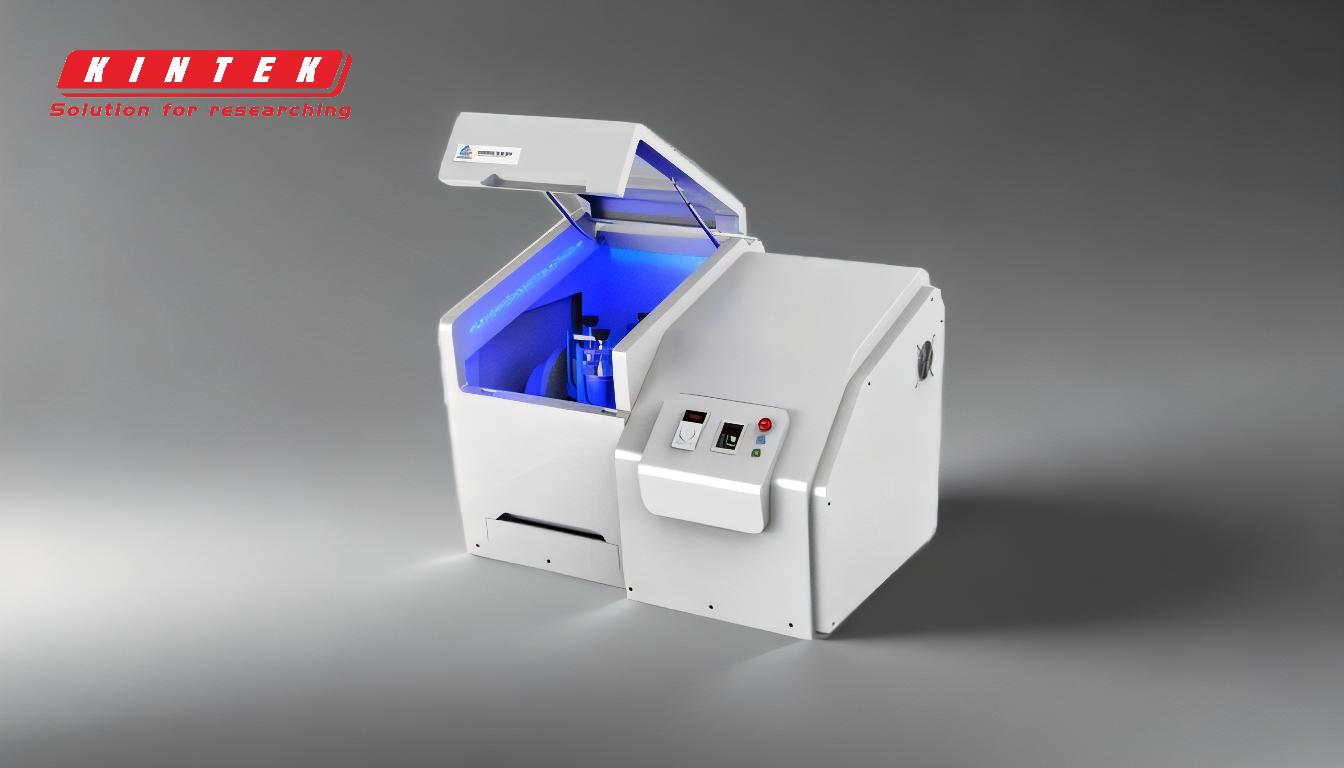
-
Ceramic Balls
- High Durability: Ceramic balls are known for their long-lasting performance, reducing the need for frequent replacements.
- Minimal Contamination: They are ideal for applications requiring high purity, as they do not introduce impurities into the material being milled.
- Applications: Commonly used in industries like pharmaceuticals, food processing, and electronics where contamination must be avoided.
-
Steel Balls
- Robustness: Steel balls are extremely durable and can withstand heavy-duty milling tasks.
- Material Hardness: They are particularly effective for milling hard materials due to their high density and strength.
- Applications: Suitable for industries such as mining, metallurgy, and construction where toughness and durability are critical.
-
Flint Pebbles
- Natural Material: Flint pebbles are a natural grinding media, often used for softer materials.
- Cost-Effective: They are generally less expensive than ceramic or steel balls.
- Applications: Ideal for applications where cost is a significant factor and the material being milled is not extremely hard.
-
Stainless Steel Balls
- Corrosion Resistance: These balls are resistant to rust and corrosion, making them suitable for wet milling processes.
- Versatility: They can be used in a variety of milling applications, including those involving corrosive materials.
- Applications: Commonly used in chemical processing, food industries, and any application where corrosion resistance is necessary.
-
Factors to Consider When Choosing Media
- Material Hardness: The hardness of the material being milled should match the hardness of the grinding media to ensure effective milling.
- Contamination Risk: For high-purity applications, choose media that minimizes contamination, such as ceramic balls.
- Durability and Cost: Consider the balance between the durability of the media and the cost, especially for large-scale operations.
- Milling Environment: Whether the milling process is dry or wet can influence the choice of media, with stainless steel being preferable for wet environments due to its corrosion resistance.
By carefully evaluating these factors, you can select the most appropriate grinding media for your ball mill, ensuring optimal performance and efficiency.
Summary Table:
Media Type | Key Properties | Applications |
---|---|---|
Ceramic Balls | High durability, minimal contamination | Pharmaceuticals, food processing, electronics (high-purity applications) |
Steel Balls | Robust, high density, durable | Mining, metallurgy, construction (heavy-duty milling tasks) |
Flint Pebbles | Natural, cost-effective | Soft materials, cost-sensitive applications |
Stainless Steel | Corrosion-resistant, versatile | Chemical processing, food industries, wet milling environments |
Need help selecting the perfect grinding media for your ball mill? Contact our experts today for personalized advice!