The biggest obstacle in producing graphene lies in achieving mass production of high-quality graphene that is free from contaminants and defects, has a large grain size, and is cost-effective. Current methods, such as Chemical Vapor Deposition (CVD), face challenges in controlling domain size, layer count, grain boundaries, and defects. Additionally, the separation of graphene from substrates without damaging its structure remains a significant hurdle. Industrial production also struggles with ensuring homogeneity, reliability, and stability across large-scale outputs, making transfer processes a critical bottleneck.
Key Points Explained:
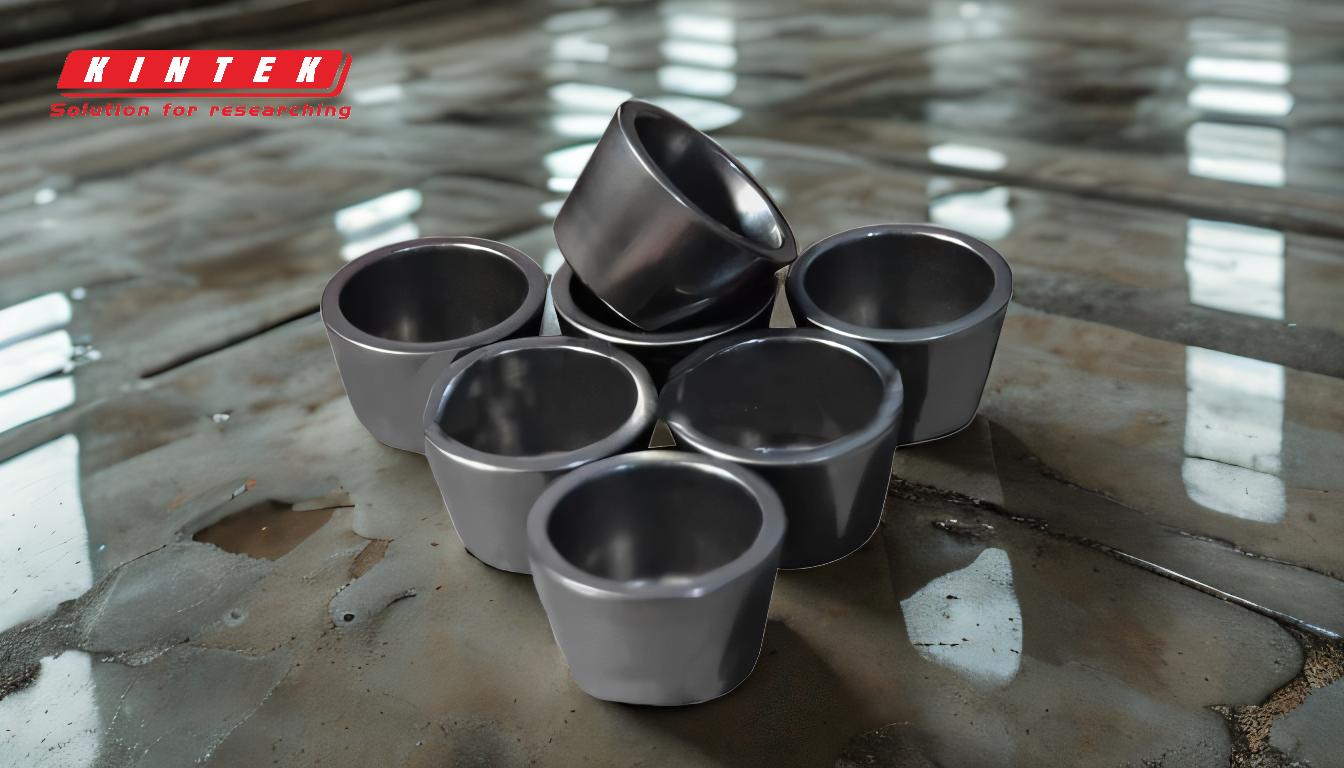
-
Mass Production of High-Quality Graphene:
- The primary challenge is producing graphene at scale without compromising quality. High-quality graphene must have minimal contaminants, few defects, and large grain sizes to ensure optimal performance in applications.
- Current methods, such as CVD, produce graphene with varying dimensions, flake shapes, and quality, but these are not yet scalable to industrial levels.
-
Control Over Graphene Properties:
- Domain Size and Grain Boundaries: CVD-produced graphene is typically polycrystalline, with domains ranging from micrometers to millimeters. Controlling the size of these domains and the density of grain boundaries is crucial for achieving uniform properties.
- Layer Count: The number of graphene layers must be precisely controlled, as single-layer graphene has different properties compared to multi-layer graphene.
- Defects: Reducing defects is essential for maintaining the electrical, thermal, and mechanical properties of graphene.
-
Separation from Substrates:
- Challenges in Exfoliation: One of the main challenges in CVD graphene production is separating the graphene from the substrate without damaging its structure. The relationship between graphene and the substrate is not fully understood, making this process complex.
- Harmful Methods: Current separation techniques, such as dissolving the substrate in harmful acids, can affect the quality of graphene. Developing safer and more effective separation methods is critical.
-
Industrial-Scale Production:
- Homogeneity and Reliability: Industrial production requires graphene that is homogeneous, reliable, and stable across large batches. Achieving this consistency is challenging due to the variability in current production methods.
- Transfer Processes: The transfer of graphene from the production substrate to the final application substrate is a significant bottleneck. Improving transfer techniques is essential for scaling up production.
-
Cost Considerations:
- Cost-Effectiveness: Producing high-quality graphene at a low cost is a significant hurdle. Current methods are either too expensive or do not produce graphene of sufficient quality for widespread industrial use.
- Scalability: Techniques that work well in the lab often do not scale efficiently to industrial levels, leading to higher costs and lower yields.
-
Research and Development Needs:
- New Methods: There is a need for new methods that can produce graphene on larger scales with larger surface areas. This includes improving existing techniques like CVD and developing entirely new approaches.
- Understanding Substrate Interactions: More research is needed to understand the interactions between graphene and substrates to develop better separation techniques.
In summary, the biggest obstacle for producing graphene is the combination of achieving high-quality, defect-free graphene at a large scale and low cost. Addressing these challenges requires advancements in production techniques, better control over graphene properties, improved separation methods, and more research into substrate interactions.
Summary Table:
Key Challenges | Details |
---|---|
Mass Production | Scaling up production without compromising quality (e.g., contaminants, defects). |
Control Over Properties | Precise control of domain size, layer count, grain boundaries, and defects. |
Separation from Substrates | Challenges in exfoliation and avoiding harmful methods during separation. |
Industrial-Scale Production | Ensuring homogeneity, reliability, and stability in large-scale outputs. |
Cost-Effectiveness | Balancing high-quality production with low costs for industrial use. |
Research and Development Needs | New methods and better understanding of substrate interactions required. |
Interested in overcoming graphene production challenges? Contact our experts today for tailored solutions!