The capacity of a furnace is primarily determined by its heating power, which is measured in British Thermal Units (BTUs) per hour. This measurement indicates how much heat the furnace can produce in an hour and is crucial for ensuring the furnace matches the heating needs of a specific space, such as a home or laboratory. Furnace capacity also depends on factors like the size of the chamber, the power rating, and the intended application. Furnaces are designed to provide uniform temperature, fast heating, energy efficiency, and durability, making them suitable for various scientific and industrial uses.
Key Points Explained:
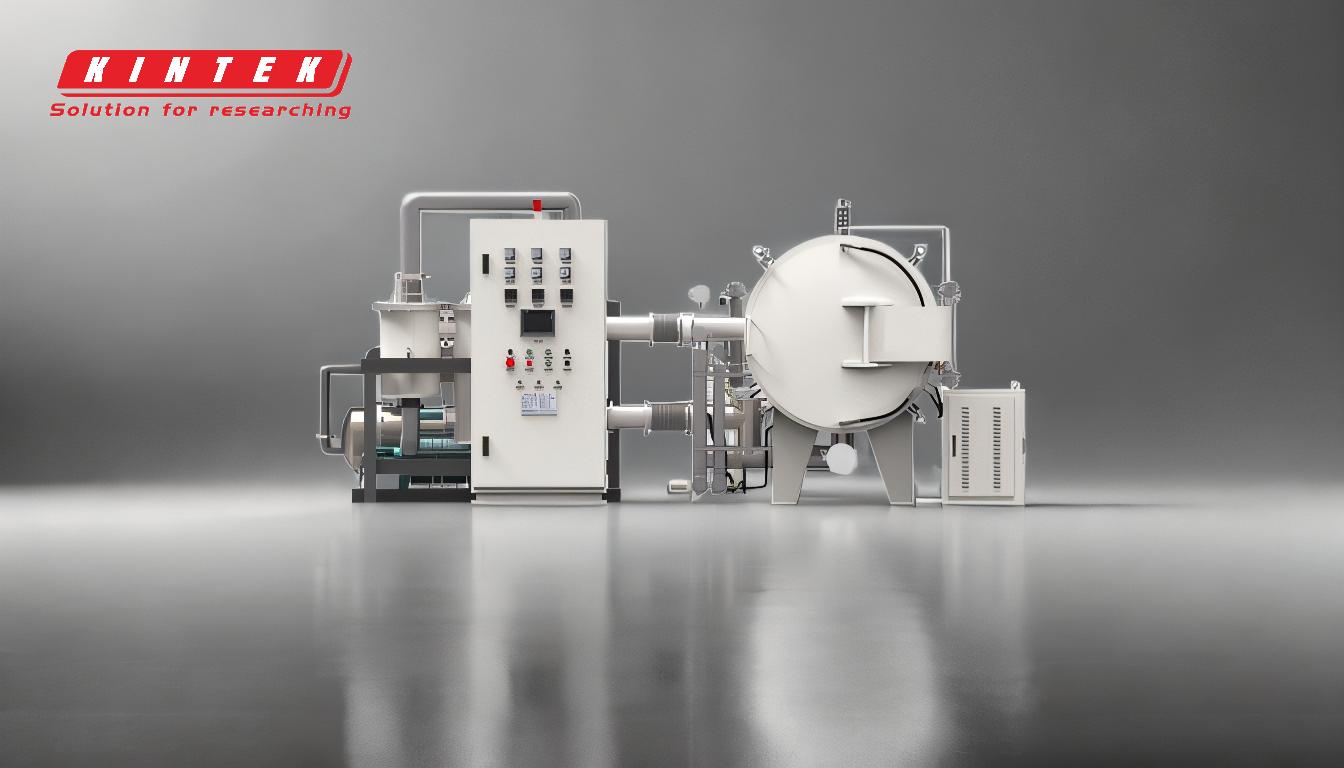
-
Heating Capacity Measurement (BTUs):
- Furnace capacity is measured in British Thermal Units (BTUs) per hour. This metric quantifies the amount of heat the furnace can generate in one hour.
- The BTU rating varies depending on the make and model of the furnace. It is essential to match the furnace's BTU output to the heating requirements of the space it will serve. For example, a larger home or industrial application may require a furnace with a higher BTU rating to ensure adequate heating.
-
Factors Influencing Furnace Capacity:
- Chamber Size: The size of the furnace chamber plays a significant role in determining its capacity. Larger chambers can accommodate more materials or larger volumes, making them suitable for industrial or high-capacity applications.
- Power Rating: The power rating of the furnace, often expressed in watts or kilowatts, directly affects its heating capacity. Higher power ratings generally correspond to greater heating capabilities.
- Application Requirements: The intended use of the furnace, such as scientific research, industrial processing, or residential heating, influences the required capacity. For instance, a muffle furnace used in laboratories may have different capacity requirements compared to a home heating furnace.
-
Performance Characteristics:
- Uniform Temperature: Furnaces are designed to maintain a consistent temperature throughout the chamber, ensuring even heating of materials.
- Fast Heating Speed: Modern furnaces are engineered to heat up quickly, reducing wait times and improving efficiency.
- Energy Efficiency: Advanced furnace designs prioritize energy savings, making them cost-effective and environmentally friendly.
- High Use Temperature: Furnaces can achieve and sustain high temperatures, making them suitable for applications requiring extreme heat.
- Long Lifespan: Durable construction and high-quality materials contribute to the long operational life of furnaces.
-
Types of Furnaces and Their Capacities:
- Muffle Furnaces: These furnaces are commonly used in laboratories and come in various sizes to accommodate different volumes of materials. Their capacity depends on the chamber size and power rating.
- Residential Furnaces: Designed for home heating, these furnaces have BTU ratings tailored to the size and insulation of the home. Proper sizing ensures efficient and effective heating.
- Industrial Furnaces: Used in manufacturing and processing, industrial furnaces often have larger capacities to handle high-volume or high-temperature applications.
-
Matching Furnace Capacity to Needs:
- Selecting the right furnace capacity involves assessing the heating requirements of the space or application. For residential use, this includes considering the square footage, insulation quality, and climate. For industrial or scientific applications, factors like material volume, desired temperature, and processing time are critical.
- Oversized furnaces can lead to inefficiency and higher energy costs, while undersized furnaces may struggle to meet heating demands. Proper matching ensures optimal performance and cost-effectiveness.
-
Conclusion:
- The capacity of a furnace is a critical factor in its performance and suitability for specific applications. Understanding the BTU rating, chamber size, power rating, and intended use helps in selecting the right furnace. Whether for residential heating, laboratory research, or industrial processing, choosing the appropriate furnace capacity ensures efficient, reliable, and cost-effective operation.
Summary Table:
Factor | Description |
---|---|
BTU Rating | Measures heating power in British Thermal Units per hour. |
Chamber Size | Larger chambers accommodate more materials or larger volumes. |
Power Rating | Higher power ratings (watts/kilowatts) enable greater heating capabilities. |
Application Needs | Determines capacity based on residential, laboratory, or industrial use. |
Performance Features | Uniform temperature, fast heating, energy efficiency, and durability. |
Need help selecting the right furnace for your needs? Contact our experts today!