The cheapest way to produce graphene depends on the desired quality and application. Mechanical exfoliation, while cost-effective, is not scalable and is primarily used for research. Liquid-phase exfoliation is suitable for mass production but yields graphene with lower electrical quality. Chemical vapor deposition (CVD) is the most promising for producing high-quality graphene at scale, but it is more expensive. For cost-sensitive applications where high electrical quality is not critical, liquid-phase exfoliation is likely the cheapest method. However, if high-quality graphene is required, CVD, despite its higher cost, remains the most viable option for large-scale production.
Key Points Explained:
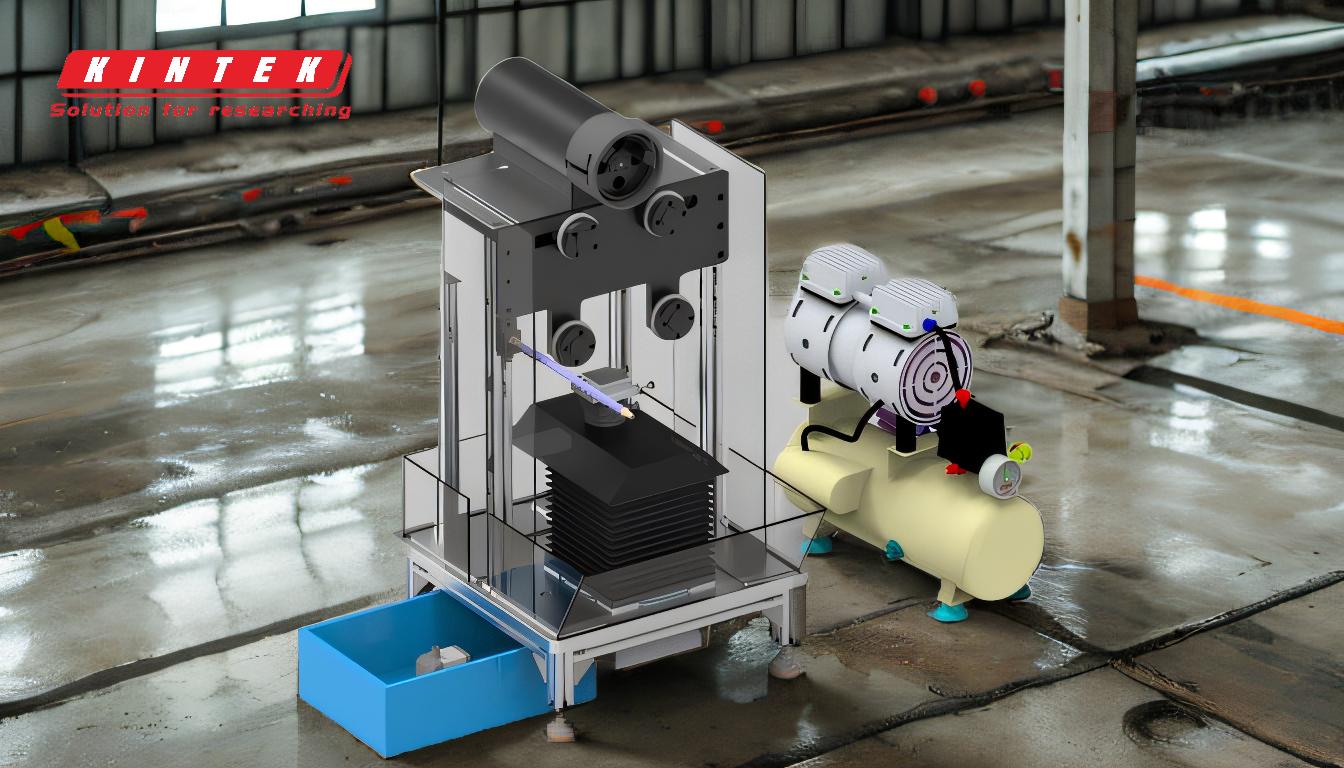
-
Mechanical Exfoliation:
- Process: Involves peeling layers of graphene from graphite using adhesive tape.
- Cost: Low cost due to minimal equipment and material requirements.
- Quality: Produces high-quality graphene but in very small quantities.
- Scalability: Not scalable for industrial applications.
- Use Case: Primarily used in research and fundamental studies.
-
Liquid-Phase Exfoliation:
- Process: Involves dispersing graphite in a liquid medium and applying ultrasonic energy to exfoliate layers.
- Cost: Relatively low cost, suitable for mass production.
- Quality: Produces graphene with lower electrical quality compared to other methods.
- Scalability: Highly scalable, making it suitable for large-scale production.
- Use Case: Ideal for applications where high electrical conductivity is not critical, such as in composites or coatings.
-
Chemical Vapor Deposition (CVD):
- Process: Involves depositing carbon atoms onto a substrate (e.g., copper) in a high-temperature chamber.
- Cost: Higher cost due to the need for specialized equipment and high-purity gases.
- Quality: Produces large-area, high-quality graphene with excellent electrical properties.
- Scalability: Scalable for industrial applications, though more expensive than liquid-phase exfoliation.
- Use Case: Suitable for applications requiring high-quality graphene, such as electronics and sensors.
-
Reduction of Graphene Oxide (GO):
- Process: Involves oxidizing graphite to produce graphene oxide, which is then reduced to graphene.
- Cost: Moderate cost, depending on the reduction method used.
- Quality: Graphene quality is lower than that produced by CVD, with more defects.
- Scalability: Scalable, but the quality may not meet the requirements for high-performance applications.
- Use Case: Suitable for applications where cost is a concern, and high electrical quality is not essential.
-
Sublimation of Silicon Carbide (SiC):
- Process: Involves heating SiC to high temperatures to sublime silicon atoms, leaving behind graphene.
- Cost: High cost due to the expensive SiC substrate and high energy requirements.
- Quality: Produces high-quality graphene, but the process is not cost-effective.
- Scalability: Limited scalability due to high costs.
- Use Case: Primarily used in research and specialized applications where cost is not a primary concern.
In summary, the cheapest method for producing graphene depends on the intended use. For research or small-scale applications, mechanical exfoliation is the most cost-effective. For large-scale production where electrical quality is not critical, liquid-phase exfoliation is the cheapest option. However, for applications requiring high-quality graphene, CVD, despite its higher cost, is the most viable method.
Summary Table:
Method | Cost | Quality | Scalability | Use Case |
---|---|---|---|---|
Mechanical Exfoliation | Low | High (small quantities) | Not scalable | Research and fundamental studies |
Liquid-Phase Exfoliation | Low | Lower electrical quality | Highly scalable | Composites, coatings (non-critical electrical) |
CVD | High | High (large-area) | Scalable | Electronics, sensors (high-quality graphene) |
Reduction of Graphene Oxide | Moderate | Lower (more defects) | Scalable | Cost-sensitive applications (non-critical) |
Sublimation of SiC | High | High | Limited scalability | Research and specialized applications |
Need help choosing the best graphene production method for your project? Contact our experts today!