Pyrolysis gas is a complex mixture of non-condensable gases produced during the pyrolysis process, which involves the thermal decomposition of organic materials in the absence of oxygen. The chemical composition of pyrolysis gas primarily includes carbon monoxide (CO), hydrogen (H₂), methane (CH₄), carbon dioxide (CO₂), nitrogen (N₂), and higher hydrocarbons. The exact composition varies depending on factors such as the type of raw material, temperature, pressure, and duration of the pyrolysis process. Pyrolysis gas is a valuable byproduct, often used to generate heat energy within the pyrolysis plant to sustain the process.
Key Points Explained:
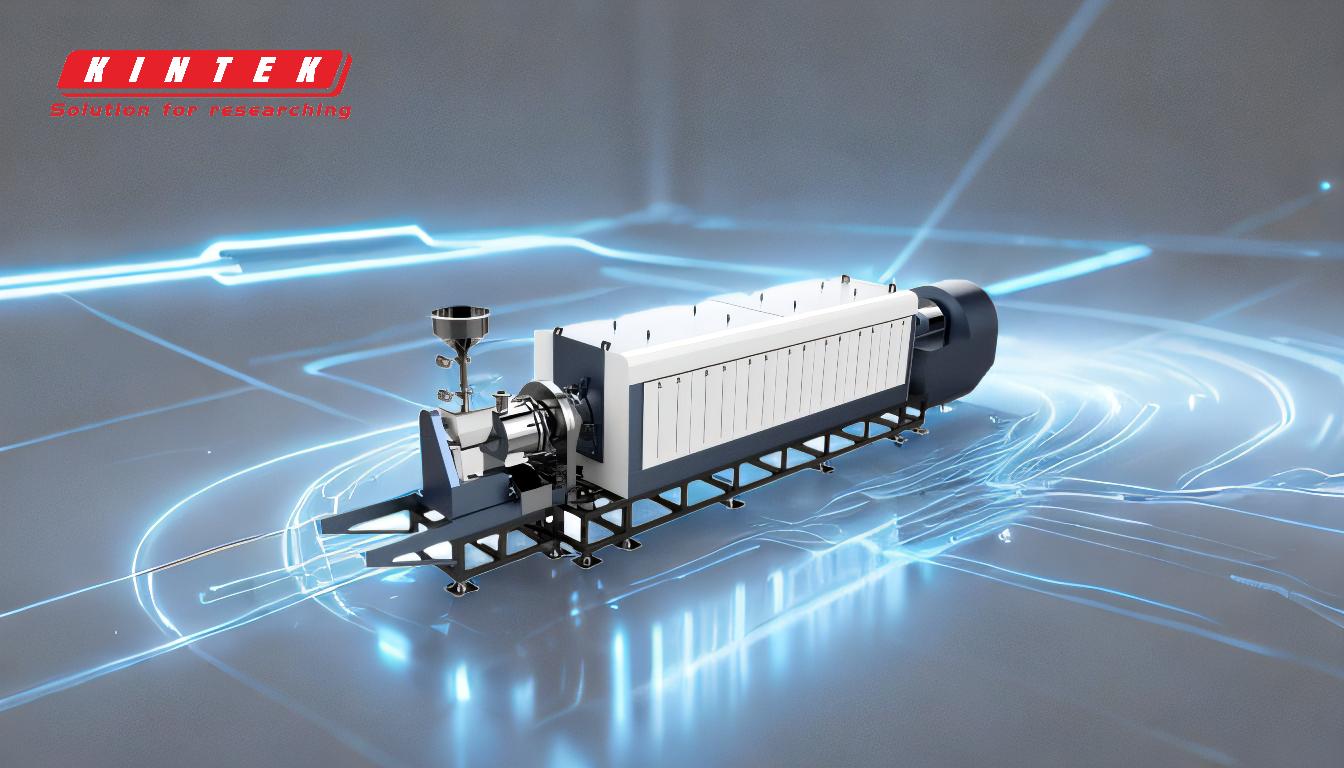
-
Primary Components of Pyrolysis Gas:
- Carbon Monoxide (CO): A major component, formed during the thermal decomposition of organic materials.
- Hydrogen (H₂): Produced from the breakdown of hydrocarbons and water-gas shift reactions.
- Methane (CH₄): A simple hydrocarbon formed during the cracking of larger organic molecules.
- Carbon Dioxide (CO₂): Resulting from partial oxidation or decomposition of oxygenated compounds.
- Nitrogen (N₂): Often present in small amounts, depending on the feedstock and process conditions.
- Higher Hydrocarbons: Include alkanes, alkenes, and aromatic compounds derived from the breakdown of complex organic materials.
-
Factors Influencing Pyrolysis Gas Composition:
- Feedstock Composition: The chemical makeup of the raw material (e.g., cellulose, hemicellulose, lignin in biomass) significantly affects the gas composition.
- Temperature: Higher temperatures favor the production of lighter gases like H₂ and CO, while lower temperatures may yield more CH₄ and higher hydrocarbons.
- Pressure: Elevated pressures can influence the equilibrium of gas-phase reactions, altering the final gas composition.
- Process Duration: Longer residence times can lead to further cracking of hydrocarbons, increasing the proportion of lighter gases.
-
Role of Pyrolysis Gas in the Process:
- Pyrolysis gas is a non-condensable gas that is primarily used to generate heat energy within the pyrolysis plant.
- It is recycled through the syn-gas recycling system to heat the reactor, making the process self-sustaining and energy-efficient.
-
Comparison with Other Pyrolysis Products:
- Coke: A solid residue used for applications like briquetting, energy production, and agriculture.
- Pyrolysis Oil: A liquid product rich in aromatic and aliphatic hydrocarbons, used as an alternative fuel or refined into biodiesel.
- Pyrolysis Gas: Distinguished by its non-condensable nature and high energy content, making it ideal for combustion and heat generation.
-
Applications and Importance:
- Pyrolysis gas is a valuable energy source that reduces the need for external fuel in pyrolysis plants.
- It contributes to the sustainability of the pyrolysis process by minimizing waste and maximizing energy recovery.
-
System Components Supporting Pyrolysis Gas Production:
- Feeding System: Delivers raw materials to the reactor in a sealed manner.
- Pyrolysis Reactor: The core component where high-temperature decomposition occurs.
- Syn-Gas Recycling System: Captures and recycles combustible gases for reactor heating.
- De-Dusting System: Ensures that emissions meet environmental standards by removing particulate matter.
By understanding the chemical composition and influencing factors of pyrolysis gas, stakeholders can optimize the pyrolysis process for specific feedstocks and applications, enhancing both efficiency and environmental sustainability.
Summary Table:
Aspect | Details |
---|---|
Primary Components | CO, H₂, CH₄, CO₂, N₂, and higher hydrocarbons |
Key Factors | Feedstock, temperature, pressure, process duration |
Role in Process | Generates heat energy, sustains pyrolysis process |
Applications | Energy source, reduces external fuel needs, enhances sustainability |
System Components | Feeding system, pyrolysis reactor, syn-gas recycling, de-dusting system |
Optimize your pyrolysis process with expert insights—contact us today to learn more!