Carbon nanotubes (CNTs) are cylindrical nanostructures made of carbon atoms, known for their exceptional mechanical, electrical, and thermal properties. They are synthesized using various methods, with chemical vapor deposition (CVD) being the most widely used commercial technique due to its cost-effectiveness and structural controllability. Emerging methods focus on sustainability, utilizing green or waste feedstocks like carbon dioxide and methane. The synthesis process involves critical parameters such as temperature, carbon source concentration, and residence time, which must be optimized to achieve high growth rates and minimize environmental impact.
Key Points Explained:
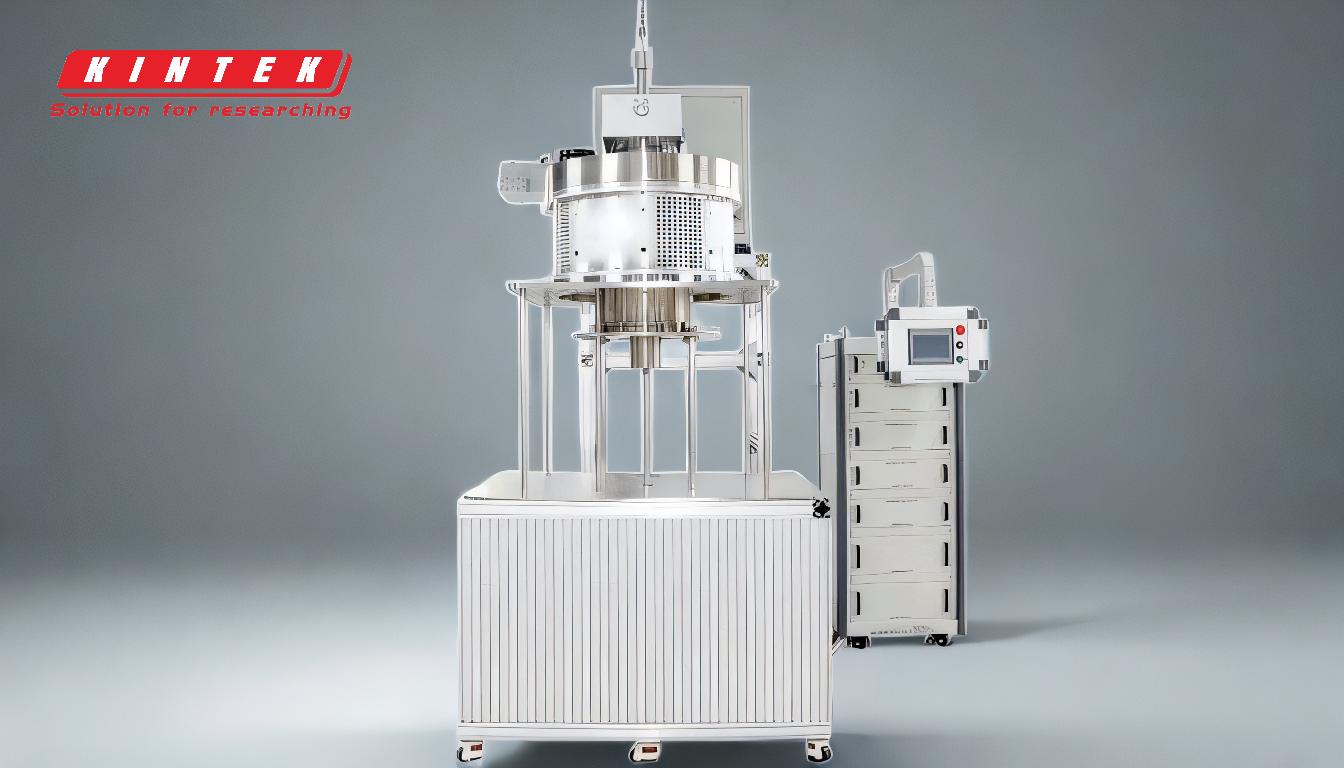
-
Chemical Vapor Deposition (CVD) as the Dominant Method:
- CVD is the most common commercial method for synthesizing carbon nanotubes. It involves the decomposition of a carbon-containing gas (such as methane or ethylene) on a catalyst surface at high temperatures.
- The process allows for precise control over the structure and properties of the nanotubes, making it suitable for large-scale production.
- Catalytic chemical vapor deposition (CCVD) is a variant of CVD that uses metal catalysts (e.g., iron, cobalt, or nickel) to enhance the growth efficiency and structural quality of CNTs.
-
Emerging Green Synthesis Methods:
- Researchers are exploring sustainable alternatives to traditional carbon sources, such as carbon dioxide captured by electrolysis in molten salts or methane pyrolysis.
- These methods aim to reduce the environmental impact of CNT production by utilizing waste or renewable feedstocks.
- For example, methane pyrolysis breaks down methane into hydrogen and solid carbon, which can be used to grow CNTs, offering a dual benefit of carbon capture and nanotube synthesis.
-
Critical Operating Parameters:
- Temperature: The synthesis temperature significantly affects the growth rate and quality of CNTs. Optimal temperatures typically range between 600°C and 1000°C, depending on the carbon source and catalyst used.
- Carbon Source Concentration: The concentration of the carbon-containing gas influences the growth rate and morphology of the nanotubes. Too low a concentration may result in incomplete growth, while too high a concentration can lead to by-product formation.
- Residence Time: The time the carbon source spends in the reaction zone must be carefully controlled. Insufficient residence time can lead to incomplete growth, while excessive residence time may cause by-product accumulation and reduced efficiency.
-
Environmental Considerations:
- The synthesis process is a major contributor to the life cycle ecotoxicity of CNTs. Efforts are being made to reduce material and energy consumption, as well as greenhouse gas emissions.
- Innovations in feedstock selection and process optimization aim to minimize the environmental footprint of CNT production.
-
Applications and Innovations:
- CNTs have diverse applications in electronics, materials science, and medicine due to their unique properties.
- Ongoing research focuses on creating hybrid products, functionalizing CNTs with other materials, and developing continuous conductive yarns for advanced applications.
- The ability to control the aspect ratio and structure of CNTs during synthesis opens up new possibilities for tailored materials with specific properties.
By understanding these key points, purchasers of equipment and consumables for CNT synthesis can make informed decisions about the methods and parameters that best suit their production goals while considering cost-effectiveness and environmental impact.
Summary Table:
Aspect | Details |
---|---|
Dominant Method | Chemical Vapor Deposition (CVD) |
Emerging Methods | Green synthesis using CO₂, methane pyrolysis |
Key Parameters | Temperature (600°C–1000°C), carbon source concentration, residence time |
Environmental Impact | Reduced ecotoxicity through sustainable feedstocks and optimized processes |
Applications | Electronics, materials science, medicine, and hybrid materials |
Discover the best methods for carbon nanotube synthesis—contact our experts today for tailored solutions!