The Cold Isostatic Pressing (CIP) process is a powder compaction technique that uses fluid pressure to uniformly compress materials at ambient temperatures. It involves placing powder or a pre-formed part into a flexible mold, which is then subjected to high-pressure liquid (often water or an oil-water mixture) from all directions. This method ensures uniform density and shape retention, making it ideal for materials like ceramics, metals, and composites. CIP is divided into wet bag and dry bag methods, depending on how the mold interacts with the pressure medium. It is widely used in industries requiring high-density, complex-shaped components, such as aerospace, medical, and tool manufacturing.
Key Points Explained:
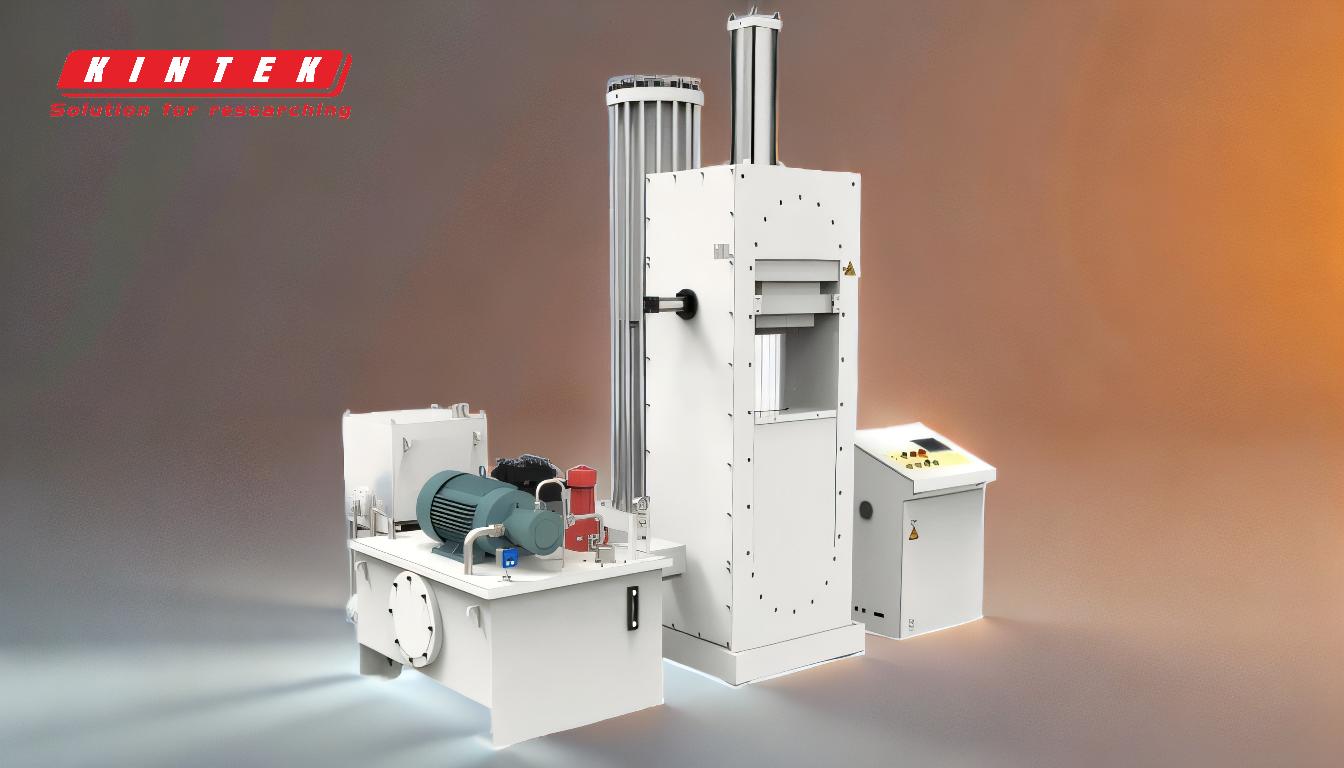
-
Definition and Process of Cold Isostatic Pressing (CIP):
- CIP is a powder compaction method that applies uniform hydrostatic pressure to materials at room temperature.
- The material is placed in a flexible mold, which is then immersed in a pressurized liquid medium (e.g., water or an oil-water mixture).
- The pressure, which can reach up to 100,000 psi, is evenly distributed, ensuring uniform density and shape.
-
Wet Bag vs. Dry Bag Methods:
- Wet Bag Method: The mold is removed from the pressure vessel after each cycle. This method is suitable for small-scale production or prototyping.
- Dry Bag Method: The mold remains inside the pressure vessel, and only the material is loaded and unloaded. This method is more efficient for large-scale production.
-
Applications of CIP:
- CIP is used in the powder forming of various materials, including:
- Refractory materials and insulators.
- Isotropic graphite and high-melting-point metals.
- Cemented carbides and tool steel.
- Sintered filters, artificial bones, and resin powder.
- Food processing industries.
- CIP is used in the powder forming of various materials, including:
-
Advantages of CIP:
- Uniform density and pressure distribution, leading to consistent product quality.
- Ability to produce complex shapes and large components.
- Suitable for a wide range of materials, including brittle and hard-to-compact powders.
-
Equipment Used in CIP:
- The core equipment is the isostatic press, which consists of a pressure chamber, a pump to pressurize the liquid medium, and a flexible mold.
- The pressure chamber is designed to withstand cyclic loading and extreme pressures.
-
Process Parameters:
- Pressure levels typically range from 15,000 to 100,000 psi, depending on the material and application.
- The liquid medium often contains corrosion inhibitors to protect the equipment and mold.
-
Industries Utilizing CIP:
- Aerospace: For producing high-strength, lightweight components.
- Medical: For manufacturing artificial bones and implants.
- Tooling: For creating durable cutting tools and dies.
- Food Processing: For compacting powdered food products.
By leveraging the CIP process, manufacturers can achieve high-density, complex-shaped components with excellent material properties, making it a versatile and essential technique in modern manufacturing.
Summary Table:
Aspect | Details |
---|---|
Process | Uniform hydrostatic pressure at room temperature using a liquid medium. |
Methods | Wet Bag (small-scale) and Dry Bag (large-scale). |
Applications | Ceramics, metals, composites, artificial bones, and food processing. |
Advantages | Uniform density, complex shapes, and compatibility with brittle materials. |
Pressure Range | 15,000 to 100,000 psi. |
Industries | Aerospace, medical, tooling, and food processing. |
Discover how the CIP process can transform your manufacturing—contact our experts today!