Sintered iron is a type of iron-based material produced through the sintering process, which involves compacting iron powder into a desired shape and then heating it below the melting point to bond the particles together. The composition of sintered iron typically includes iron as the primary component, along with other elements such as carbon, copper, nickel, and sometimes alloying agents like chromium or molybdenum. These additives enhance specific properties such as strength, wear resistance, and corrosion resistance. The exact composition depends on the intended application, with variations tailored to meet mechanical, thermal, or chemical requirements.
Key Points Explained:
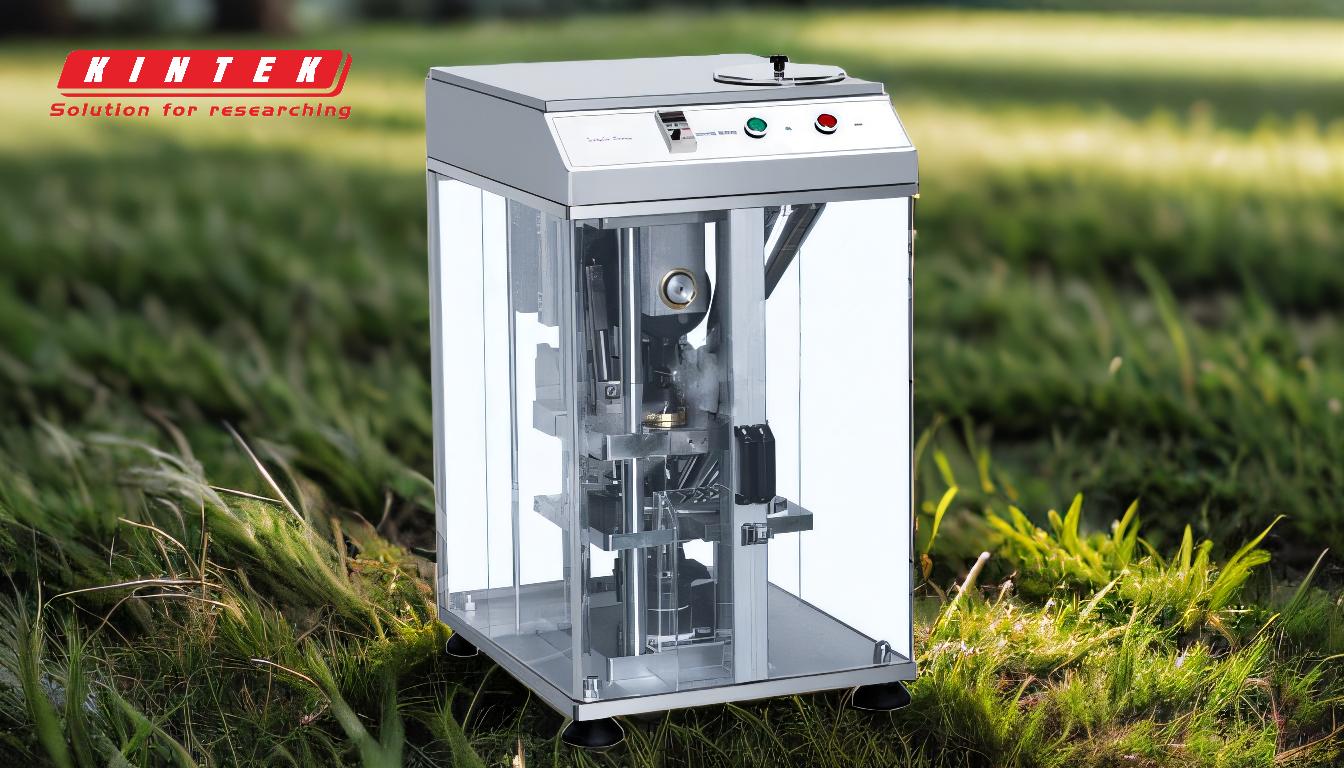
-
Primary Component: Iron
- Iron is the main constituent of sintered iron, forming the bulk of the material. It provides the foundational structure and mechanical properties, such as strength and ductility.
-
Carbon Content
- Carbon is often added to sintered iron to improve hardness and strength. The amount of carbon can vary depending on the desired properties, with higher carbon content typically resulting in increased hardness but reduced ductility.
-
Alloying Elements
- Alloying elements such as copper, nickel, chromium, and molybdenum are frequently incorporated to enhance specific characteristics:
- Copper: Improves strength and wear resistance.
- Nickel: Enhances toughness and corrosion resistance.
- Chromium and Molybdenum: Increase hardness and high-temperature performance.
- Alloying elements such as copper, nickel, chromium, and molybdenum are frequently incorporated to enhance specific characteristics:
-
Additives for Specific Properties
- Other additives, such as graphite or lubricants, may be included to improve machinability, reduce friction, or facilitate the sintering process.
-
Porosity and Density
- Sintered iron often exhibits a porous structure due to the sintering process. The porosity can be controlled to achieve specific density and permeability requirements, which are crucial for applications like filters or self-lubricating bearings.
-
Applications and Composition Variations
- The composition of sintered iron is tailored to its intended use. For example:
- Automotive Parts: High strength and wear resistance are prioritized, often achieved with higher carbon and alloying element content.
- Filters or Bearings: Controlled porosity and lower density are more important, requiring adjustments in the sintering process and additives.
- The composition of sintered iron is tailored to its intended use. For example:
-
Manufacturing Process Influence
- The sintering process itself influences the final composition. Factors such as sintering temperature, time, and atmosphere (e.g., reducing or inert) can affect the distribution and bonding of elements within the material.
By understanding the composition and its impact on properties, manufacturers can design sintered iron materials optimized for specific applications, ensuring they meet the necessary performance criteria.
Summary Table:
Component | Role |
---|---|
Iron | Primary component providing strength and ductility. |
Carbon | Enhances hardness and strength; higher content increases hardness. |
Copper | Improves strength and wear resistance. |
Nickel | Boosts toughness and corrosion resistance. |
Chromium/Molybdenum | Increases hardness and high-temperature performance. |
Additives (e.g., graphite) | Improves machinability and reduces friction. |
Porosity/Density | Controlled for specific applications like filters or bearings. |
Need sintered iron tailored for your application? Contact our experts today for customized solutions!