The compression ratio of a pellet die is a critical factor in determining the quality and durability of the pellets produced. It is defined as the ratio of the effective length of the die (the thickness of the die that performs work on the feed) to the diameter of the die hole. A higher compression ratio generally results in more compact and durable pellets, while a lower ratio may produce less dense pellets. The compression ratio is influenced by factors such as feed formulation, raw material properties, and operator skill, all of which also impact the overall life and performance of the pellet die.
Key Points Explained:
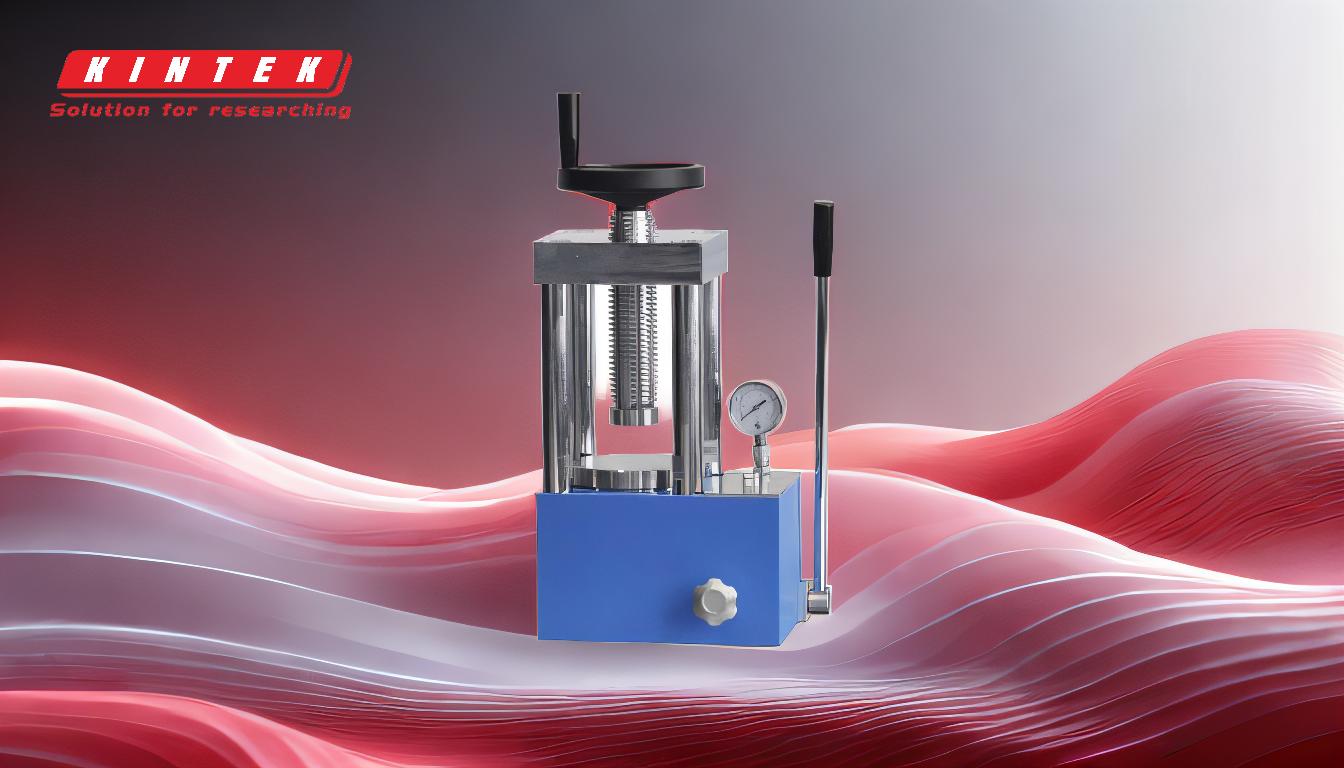
-
Definition of Compression Ratio:
- The compression ratio of a pellet die is calculated as the ratio of the effective length (E) of the die to the diameter of the die hole. This ratio is crucial in determining the density and durability of the pellets produced. A higher compression ratio typically results in more compact pellets, while a lower ratio may yield less dense pellets.
-
Effective Length (E) of the Die:
- The effective length is the portion of the die thickness that actively works on the feed to compress it into pellets. A greater effective length means more work is done on the feed, leading to more compact pellets. Conversely, a lesser effective length reduces the compactness of the pellets.
-
Factors Influencing Compression Ratio:
- Feed Formulation and Composition: High fiber content in the feed can reduce the life of the die and affect the compression ratio by making it harder to achieve a uniform pellet density.
- Raw Material Properties: The characteristics of the raw materials, such as being fibrous, spongy, or abrasive, can influence the compression ratio and the overall performance of the die.
- Fat Content: Higher fat content in the feed acts as a lubricant, reducing friction and potentially affecting the compression ratio by making it easier to compress the feed.
- Particle Size: Consistent particle size in the mash can help maintain a uniform compression ratio, leading to more consistent pellet quality.
- Moisture Content: Proper conditioning of the feed with the right moisture content is essential for achieving the desired compression ratio and pellet quality.
-
Operator Skill and Maintenance:
- The skill of the operator plays a significant role in maintaining the correct compression ratio. Regular checks on wear and maintenance, such as changing the side of the die for uniform wear, cleaning magnets, and timely changing of roll shells, are essential for optimal die performance.
-
Impact on Pellet Quality:
- The compression ratio directly affects the quality of the pellets. A higher ratio generally produces more durable and compact pellets, which are less likely to break during handling and storage. Conversely, a lower ratio may result in pellets that are less dense and more prone to breaking.
-
Optimizing Die Performance:
- Using separate dies for different types of feed, such as broiler and layer feed, can help optimize the compression ratio and overall performance of the pellet mill. This ensures that the die is tailored to the specific requirements of each type of feed, leading to better pellet quality and longer die life.
In summary, the compression ratio of a pellet die is a key factor in determining the quality and durability of the pellets produced. It is influenced by various factors, including feed formulation, raw material properties, and operator skill. Proper maintenance and optimization of the die can help achieve the desired compression ratio, leading to high-quality pellets and extended die life.
Summary Table:
Key Factor | Impact on Compression Ratio |
---|---|
Effective Length (E) | Higher E = more compact pellets; lower E = less dense pellets. |
Feed Formulation | High fiber content = harder to achieve uniform density; affects die life. |
Raw Material Properties | Fibrous, spongy, or abrasive materials = influence compression ratio and die performance. |
Fat Content | Higher fat = acts as a lubricant, reduces friction, and eases compression. |
Particle Size | Consistent size = uniform compression ratio and better pellet quality. |
Moisture Content | Proper conditioning = essential for achieving desired compression ratio and pellet quality. |
Operator Skill & Maintenance | Regular checks and maintenance = optimal die performance and consistent compression ratio. |
Optimize your pellet production with the right compression ratio—contact our experts today for tailored solutions!