The cost of biomass production is influenced by a variety of factors, including the type of biomass, the scale of production, the technology used, and the geographic location. Biomass can be derived from various sources such as agricultural residues, forestry waste, energy crops, and organic waste. The cost structure typically includes expenses related to feedstock procurement, processing, transportation, and storage. Additionally, the cost can be affected by government policies, subsidies, and market demand. Understanding these factors is crucial for anyone involved in the biomass supply chain, from producers to end-users, as it helps in making informed decisions and optimizing production processes.
Key Points Explained:
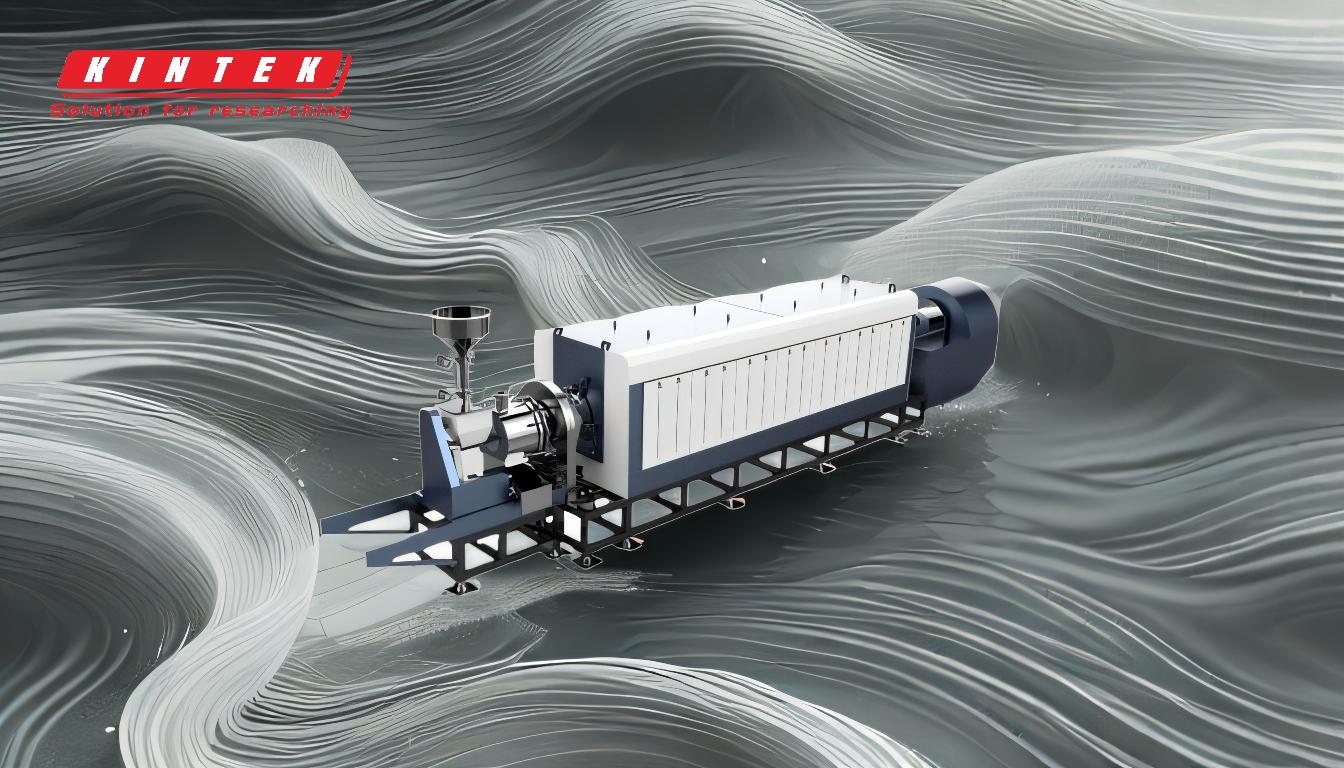
-
Types of Biomass and Their Cost Implications
- Agricultural Residues: These include crop residues like straw, husks, and shells. The cost is generally lower because these are by-products of existing agricultural activities. However, collection and transportation can add to the overall expense.
- Forestry Waste: This includes branches, bark, and sawdust. The cost can vary depending on the accessibility of the forest and the machinery used for collection.
- Energy Crops: Crops like switchgrass and miscanthus are grown specifically for biomass production. The cost is higher due to the need for land, water, and fertilizers.
- Organic Waste: This includes municipal solid waste and animal manure. The cost can be lower if the waste is readily available, but processing can be expensive.
-
Scale of Production
- Small-Scale Production: Typically involves higher per-unit costs due to lower economies of scale. However, it can be more flexible and adaptable to local conditions.
- Large-Scale Production: Benefits from economies of scale, leading to lower per-unit costs. However, it requires significant upfront investment and efficient logistics.
-
Technology and Processing Costs
- Thermochemical Processes: Includes methods like pyrolysis and gasification. These technologies can be expensive to set up but are efficient in converting biomass into energy.
- Biochemical Processes: Includes anaerobic digestion and fermentation. These are generally less expensive but may require more time and specific conditions.
- Mechanical Processing: Involves grinding, pelletizing, and briquetting. The cost depends on the machinery used and the energy required.
-
Transportation and Storage
- Transportation Costs: These can be significant, especially if the biomass needs to be transported over long distances. The cost is influenced by the type of biomass, the distance, and the mode of transportation.
- Storage Costs: Proper storage is essential to prevent degradation of biomass. The cost includes infrastructure like silos, warehouses, and climate control systems.
-
Geographic and Policy Factors
- Geographic Location: The cost can vary widely depending on the region. Areas with abundant biomass resources may have lower costs, while regions with limited resources may face higher costs.
- Government Policies: Subsidies, tax incentives, and grants can significantly reduce the cost of biomass production. Conversely, stringent regulations can increase costs.
-
Market Demand and Pricing
- Demand Fluctuations: High demand can drive up prices, while low demand can lead to oversupply and lower prices.
- Competition: The presence of multiple producers can lead to competitive pricing, benefiting consumers but potentially squeezing margins for producers.
Understanding these key points can help stakeholders in the biomass industry to better navigate the complexities of production costs and make more informed decisions.
Summary Table:
Factor | Cost Implications |
---|---|
Types of Biomass | Agricultural residues (low cost), forestry waste (variable), energy crops (higher), organic waste (processing costs) |
Scale of Production | Small-scale (higher per-unit costs), large-scale (lower per-unit costs, high upfront investment) |
Technology | Thermochemical (high setup costs), biochemical (lower costs, time-intensive), mechanical (machinery-dependent) |
Transportation/Storage | Transportation costs vary by distance and mode; storage requires infrastructure investment |
Geographic/Policy | Costs vary by region; subsidies and regulations can significantly impact expenses |
Market Demand | High demand increases prices; competition can lead to lower prices |
Want to optimize your biomass production costs? Contact us today for expert guidance and solutions!