E-beam evaporation is a sophisticated physical vapor deposition (PVD) technique used to create thin films on substrates. It involves using a high-power electron beam to evaporate the source material, which then deposits onto the substrate. This method is highly versatile, capable of evaporating materials with high melting points, and offers advantages such as low contamination, high deposition rates, and excellent uniformity. The process is widely used in applications like optical thin films, solar panels, and architectural glass. The electron beam's current is a critical parameter, as it directly influences the energy delivered to the source material, affecting the evaporation rate and film quality.
Key Points Explained:
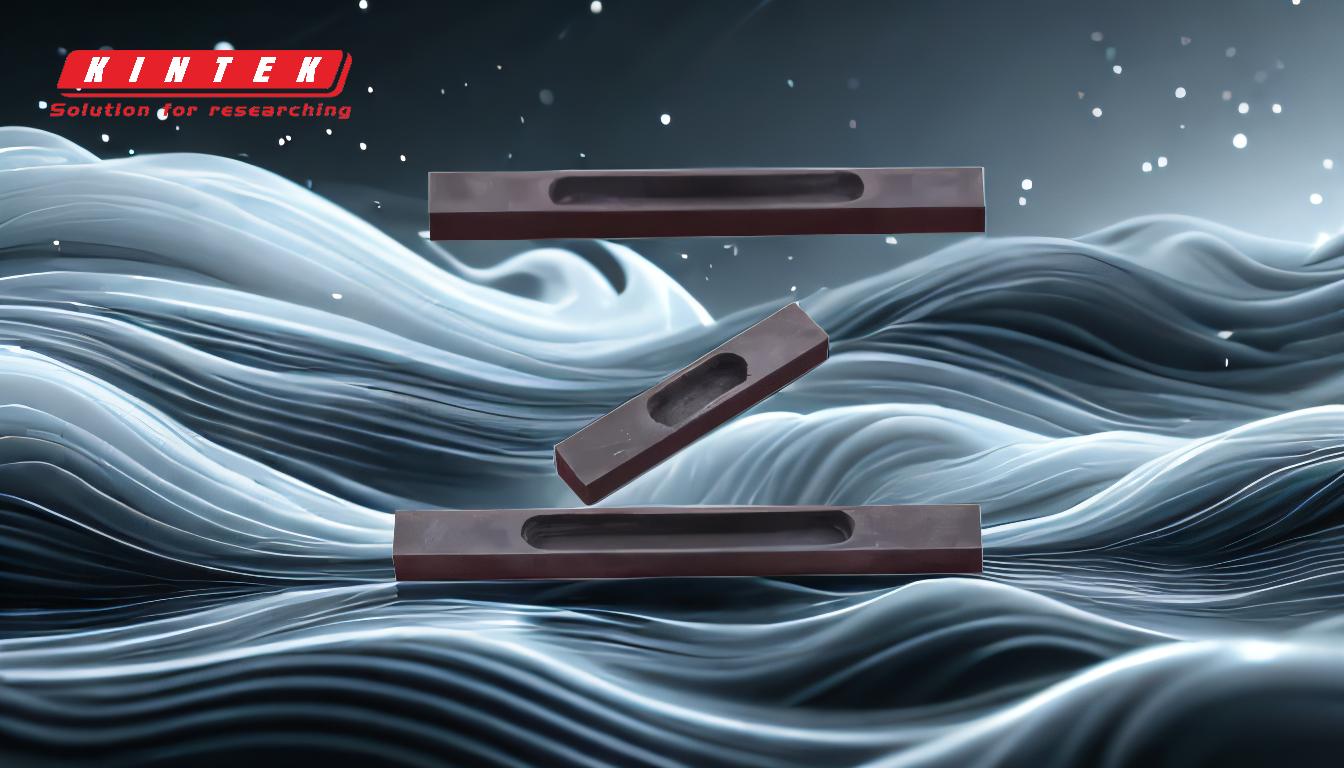
-
E-beam Evaporation Process:
- E-beam evaporation is a type of physical vapor deposition (PVD) where a high-power electron beam is directed at the source material, causing it to evaporate.
- The evaporated material then deposits onto a substrate, forming a thin film. This process is conducted under high vacuum conditions to minimize contamination.
-
Role of Electron Beam Current:
- The current of the electron beam is a crucial parameter in e-beam evaporation. It determines the energy delivered to the source material, which in turn affects the evaporation rate.
- Higher beam currents result in greater energy transfer, enabling the evaporation of materials with high melting points, such as refractory metals.
-
Advantages of E-beam Evaporation:
- Low Contamination: The high vacuum environment and precise control of the electron beam minimize impurities in the deposited film.
- High Deposition Rates: The focused electron beam allows for rapid evaporation and deposition, making the process efficient for industrial applications.
- Versatility: E-beam evaporation can handle a wide range of materials, including those with high melting points, which are difficult to evaporate using other methods.
-
Applications of E-beam Evaporation:
- Optical Thin Films: Used in the production of coatings for solar panels, glasses, and architectural glass.
- Refractory Metals: Ideal for depositing materials like tungsten and tantalum, which require high temperatures for evaporation.
- Semiconductors: Utilized in the fabrication of electronic components due to its precision and low contamination levels.
-
Control and Monitoring:
- The process is monitored and controlled using tools like quartz crystal microbalances, which regulate the deposition rate and ensure uniform film thickness.
- Precise control of the electron beam current and other parameters is essential for achieving the desired film properties.
-
Comparison with Thermal Evaporation:
- E-beam evaporation is more complex than thermal evaporation but offers significant advantages, such as the ability to evaporate high-melting-point materials and achieve higher purity levels.
- Thermal evaporation is limited by the operating temperature range of the heating elements, whereas e-beam evaporation can handle much higher temperatures.
In summary, the current of the electron beam in e-beam evaporation is a key factor that influences the energy delivered to the source material, affecting the evaporation rate and the quality of the deposited film. This method is highly versatile, offering low contamination, high deposition rates, and the ability to handle a wide range of materials, making it suitable for various industrial applications.
Summary Table:
Aspect | Details |
---|---|
Process | High-power electron beam evaporates source material, depositing thin films. |
Key Parameter | Electron beam current determines energy transfer and evaporation rate. |
Advantages | Low contamination, high deposition rates, and material versatility. |
Applications | Optical thin films, refractory metals, semiconductors, and more. |
Monitoring Tools | Quartz crystal microbalances ensure uniform film thickness. |
Comparison | Superior to thermal evaporation for high-melting-point materials. |
Discover how e-beam evaporation can enhance your thin film processes—contact our experts today!