Pneumatic and hydraulic press machines are both used to apply pressure, but they differ in their mechanisms, applications, and performance characteristics. Pneumatic presses use compressed air to generate force, making them faster and more suitable for lighter tasks. Hydraulic presses, on the other hand, use fluid pressure to generate significantly higher force, making them ideal for heavy-duty applications. The choice between the two depends on factors like required force, speed, precision, and operational environment.
Key Points Explained:
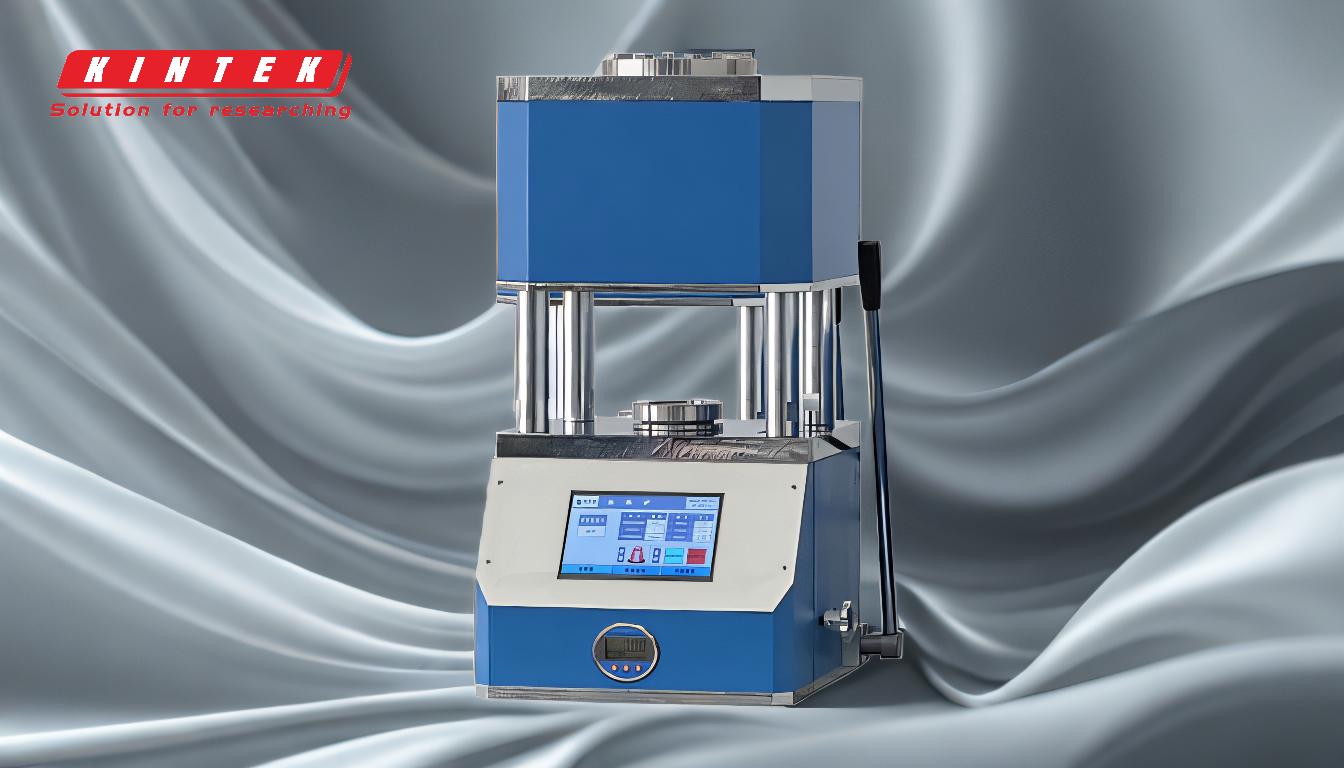
-
Mechanism of Operation:
- Pneumatic Press: Operates using compressed air. Air is pumped into a cylinder, where it expands to push a piston and generate force.
- Hydraulic Press: Operates using hydraulic fluid. A pump pressurizes the fluid, which then moves a piston to generate force. This system can produce much higher forces compared to pneumatic systems.
-
Force Generation:
- Pneumatic Press: Generates lower force compared to hydraulic presses, typically suitable for applications requiring up to a few tons of force.
- Hydraulic Press: Capable of generating extremely high forces, often used in applications requiring tens or hundreds of tons of force.
-
Speed and Efficiency:
- Pneumatic Press: Faster cycle times due to the quick expansion and contraction of air. Ideal for high-speed, repetitive tasks.
- Hydraulic Press: Slower cycle times because hydraulic fluid is less compressible and requires more time to build and release pressure. However, it offers greater precision and control.
-
Precision and Control:
- Pneumatic Press: Less precise due to the compressibility of air, which can lead to variability in force application.
- Hydraulic Press: Offers superior precision and consistent pressure application, making it suitable for tasks requiring exact force measurements.
-
Applications:
- Pneumatic Press: Commonly used in light-duty applications such as assembly, clamping, and small-scale forming.
- Hydraulic Press: Used in heavy-duty applications such as metal forming, forging, and stamping, where high force is required.
-
Maintenance and Durability:
- Pneumatic Press: Generally requires less maintenance due to fewer moving parts and no hydraulic fluid to manage. However, air compressors and seals may need regular upkeep.
- Hydraulic Press: Requires more maintenance due to the complexity of hydraulic systems, including fluid leaks, pump maintenance, and filter changes.
-
Cost:
- Pneumatic Press: Typically less expensive to purchase and operate, with lower energy consumption and simpler components.
- Hydraulic Press: Higher initial cost and operational expenses due to the need for hydraulic fluid, pumps, and more complex systems.
-
Environmental and Safety Considerations:
- Pneumatic Press: Safer in terms of fire risk since it uses air instead of flammable hydraulic fluids. However, air compressors can be noisy.
- Hydraulic Press: Requires careful handling of hydraulic fluids, which can be hazardous if leaked. Proper sealing and maintenance are critical to prevent environmental contamination.
By understanding these differences, purchasers can make informed decisions based on their specific needs, whether they prioritize speed, force, precision, or cost-effectiveness.
Summary Table:
Feature | Pneumatic Press | Hydraulic Press |
---|---|---|
Mechanism | Compressed air | Hydraulic fluid |
Force Generation | Lower force (up to a few tons) | High force (tens or hundreds of tons) |
Speed | Faster cycle times | Slower cycle times |
Precision | Less precise | Superior precision |
Applications | Light-duty (assembly, clamping) | Heavy-duty (forging, stamping) |
Maintenance | Less maintenance | More maintenance |
Cost | Lower cost | Higher cost |
Safety | Safer (no flammable fluids) | Requires careful handling of fluids |
Need help choosing the right press machine for your needs? Contact our experts today!