Blast furnaces and induction furnaces are two distinct types of industrial furnaces used in metal production, each with unique operating principles, applications, and advantages. Blast furnaces are primarily used for large-scale iron production, relying on combustion and chemical reactions to reduce iron ore into molten iron. In contrast, induction furnaces use electromagnetic induction to melt metals, offering precise temperature control, energy efficiency, and suitability for smaller batch sizes. Below, the key differences between these two furnace types are explained in detail, focusing on their working principles, structural characteristics, fuel sources, applications, and environmental impacts.
Key Points Explained:
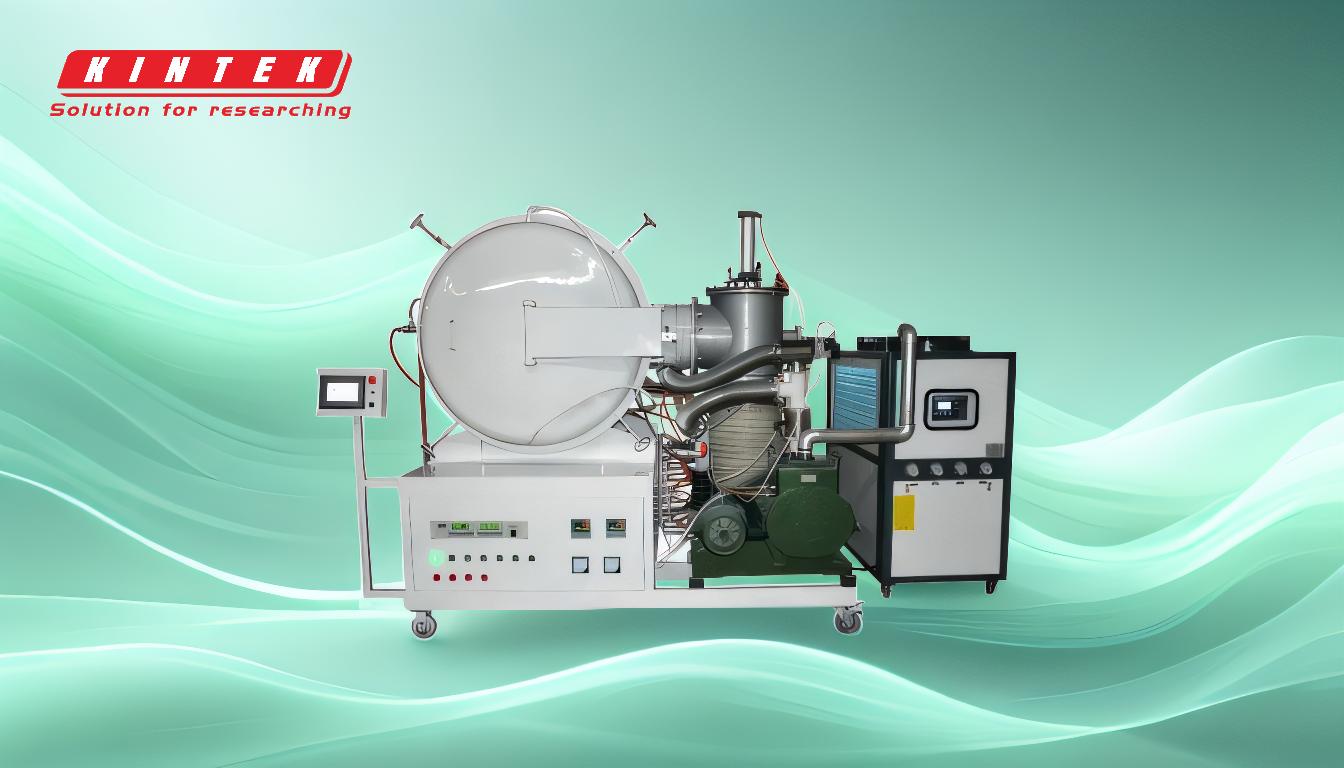
-
Working Principles:
-
Blast Furnace:
- Operates through a continuous process involving the reduction of iron ore using coke (a carbon-rich fuel) and limestone as a flux.
- Combustion of coke generates heat and carbon monoxide, which reacts with iron oxides to produce molten iron and slag.
- The process is highly dependent on chemical reactions and requires a constant supply of raw materials and fuel.
-
Induction Furnace:
- Uses electromagnetic induction to generate heat within the metal itself.
- A coil carrying alternating current creates a magnetic field, inducing eddy currents in the metal, which heats and melts it.
- This method provides precise temperature control and uniform heating, making it ideal for melting and refining metals like steel, aluminum, and alloys.
-
Blast Furnace:
-
Structural Characteristics:
-
Blast Furnace:
- A large, vertical structure typically over 30 meters tall, designed to handle high volumes of raw materials.
- Consists of a stack, hearth, and tuyeres for injecting hot air into the furnace.
- Built to withstand extreme temperatures and pressures, with refractory linings to protect against wear and corrosion.
-
Induction Furnace:
- Compact and modular, with a crucible or heating chamber surrounded by induction coils.
- Designed for smaller batch sizes and precise control over melting conditions.
- Often features advanced cooling systems and insulation to maintain efficiency and safety.
-
Blast Furnace:
-
Fuel Sources:
-
Blast Furnace:
- Relies on coke as the primary fuel and reducing agent.
- Requires a continuous supply of coke, iron ore, and limestone, making it resource-intensive.
-
Induction Furnace:
- Powered by electricity, eliminating the need for combustible fuels.
- More energy-efficient and environmentally friendly, as it produces fewer emissions and can utilize renewable energy sources.
-
Blast Furnace:
-
Applications:
-
Blast Furnace:
- Primarily used for large-scale iron production in integrated steel plants.
- Suitable for producing pig iron, which is further refined into steel in basic oxygen furnaces or electric arc furnaces.
-
Induction Furnace:
- Ideal for melting and refining metals in smaller batches, such as in foundries and specialty steel production.
- Commonly used for producing high-quality alloy steels, non-ferrous metals, and precision castings.
-
Blast Furnace:
-
Environmental Impact:
-
Blast Furnace:
- Generates significant emissions, including carbon dioxide, sulfur oxides, and particulate matter.
- Requires extensive pollution control measures to mitigate environmental impact.
-
Induction Furnace:
- Produces fewer emissions and has a lower carbon footprint, especially when powered by renewable energy.
- More sustainable and aligned with modern environmental regulations.
-
Blast Furnace:
-
Cost and Efficiency:
-
Blast Furnace:
- High capital and operational costs due to its large scale and continuous operation.
- Economical for mass production but less flexible for small-scale or specialized applications.
-
Induction Furnace:
- Lower initial investment and operational costs for smaller batch sizes.
- Highly efficient and cost-effective for producing high-quality metals with minimal waste.
-
Blast Furnace:
In summary, blast furnaces and induction furnaces serve different purposes in metal production, with blast furnaces excelling in large-scale iron production and induction furnaces offering precision and efficiency for smaller-scale operations. The choice between the two depends on factors such as production scale, material requirements, and environmental considerations.
Summary Table:
Aspect | Blast Furnace | Induction Furnace |
---|---|---|
Working Principle | Uses coke combustion and chemical reactions to reduce iron ore into molten iron. | Uses electromagnetic induction to melt metals with precise temperature control. |
Structure | Large, vertical structure (30+ meters tall) for high-volume production. | Compact and modular, designed for smaller batch sizes. |
Fuel Source | Coke (carbon-rich fuel) and limestone. | Electricity, making it energy-efficient and eco-friendly. |
Applications | Large-scale iron production in steel plants. | Melting and refining metals in foundries and specialty steel production. |
Environmental Impact | High emissions (CO2, SOx, particulate matter); requires pollution control. | Lower emissions and carbon footprint, especially with renewable energy. |
Cost & Efficiency | High capital and operational costs; economical for mass production. | Lower costs for small batches; efficient and cost-effective for high-quality metals. |
Need help choosing the right furnace for your metal production? Contact our experts today!