A brake press and a punch press are both essential tools in metalworking, but they serve different purposes and operate in distinct ways. A brake press is primarily used for bending sheet metal into specific shapes, utilizing a punch and die to create precise angles and bends. On the other hand, a punch press is designed for cutting holes or shapes out of metal sheets by forcing a punch through the material into a die. While both machines involve the use of dies and punches, their applications, mechanisms, and outcomes differ significantly. Understanding these differences is crucial for selecting the right equipment for specific metalworking tasks.
Key Points Explained:
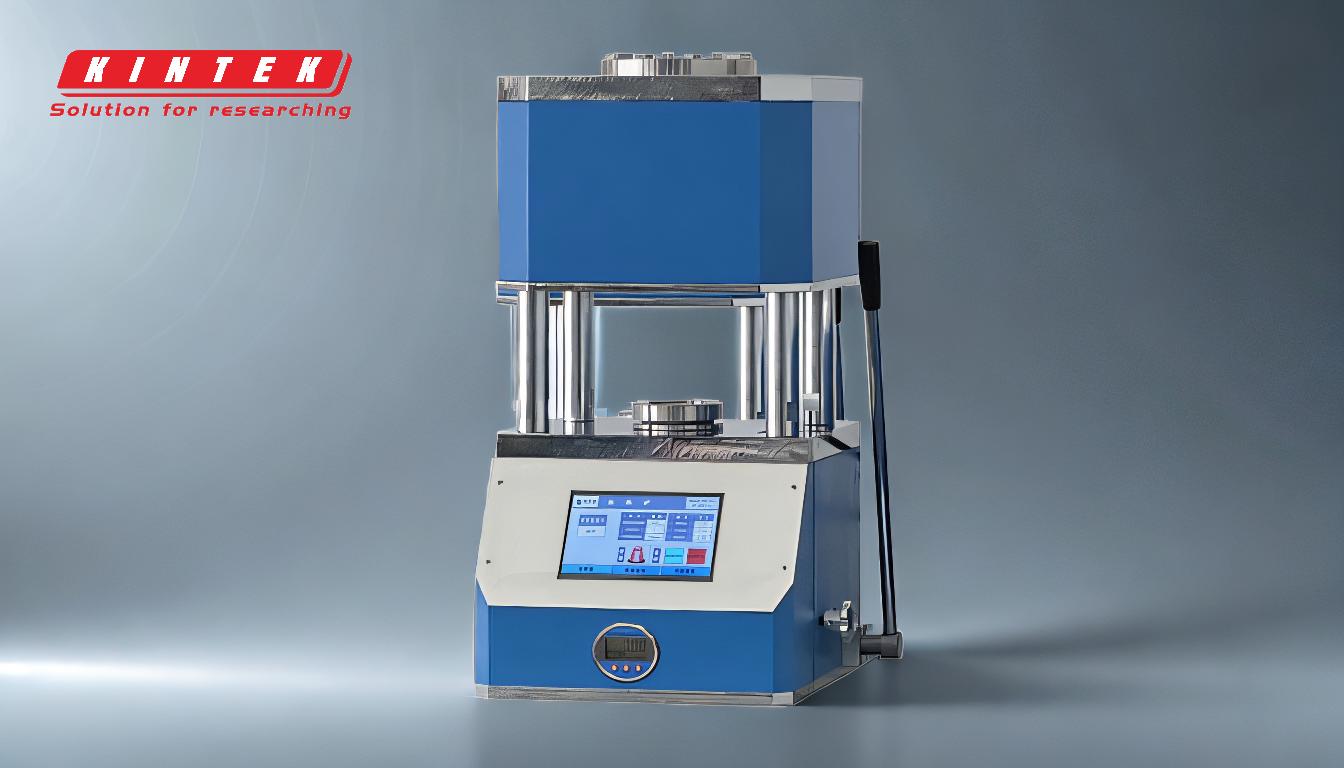
-
Primary Function:
- Brake Press: Used for bending and shaping sheet metal. It applies force to create folds, angles, or curves in the material.
- Punch Press: Used for cutting or punching holes, slots, or shapes out of sheet metal. It removes material rather than reshaping it.
-
Mechanism of Operation:
- Brake Press: Operates by clamping the sheet metal between a punch and a die, then applying downward force to bend the material. The bending angle is determined by the tooling and the depth of the press.
- Punch Press: Uses a punch and die to shear or cut through the material. The punch moves vertically to pierce the metal, creating the desired shape or hole.
-
Applications:
- Brake Press: Ideal for creating components like brackets, enclosures, and panels that require precise bends or folds.
- Punch Press: Suitable for producing parts with holes, slots, or intricate cutouts, such as electrical panels or decorative metalwork.
-
Tooling:
- Brake Press: Requires specialized tooling, such as V-dies and punches, designed for specific bending operations.
- Punch Press: Uses a variety of punches and dies tailored for cutting specific shapes or sizes.
-
Precision and Flexibility:
- Brake Press: Offers high precision in bending angles and is highly flexible for different sheet metal thicknesses and materials.
- Punch Press: Provides high accuracy in hole placement and shape consistency but is less flexible for varying material thicknesses.
-
Automation:
- Brake Press: Often manually operated or CNC-controlled for complex bending tasks.
- Punch Press: Frequently automated with CNC technology for high-speed, repetitive punching operations.
-
Material Handling:
- Brake Press: Typically handles larger sheets of metal, making it suitable for big projects.
- Punch Press: Can handle smaller or larger sheets but is often used for smaller, more intricate work.
-
Output:
- Brake Press: Produces bent or folded components without removing material.
- Punch Press: Produces components with holes or cutouts by removing material.
-
Cost and Maintenance:
- Brake Press: Generally has lower maintenance costs but requires skilled operators for precise bending.
- Punch Press: May have higher maintenance costs due to the wear and tear of punches and dies but can be more cost-effective for high-volume production.
-
Industry Use:
- Brake Press: Commonly used in industries like automotive, aerospace, and construction for creating structural components.
- Punch Press: Widely used in manufacturing, electronics, and decorative metalwork for producing parts with specific cutouts or designs.
Understanding these differences helps in selecting the appropriate machine based on the specific requirements of a project, ensuring efficiency, precision, and cost-effectiveness.
Summary Table:
Aspect | Brake Press | Punch Press |
---|---|---|
Primary Function | Bending and shaping sheet metal | Cutting or punching holes, slots, or shapes in sheet metal |
Mechanism | Clamps sheet metal between a punch and die to bend | Uses a punch and die to shear or cut through material |
Applications | Brackets, enclosures, panels | Electrical panels, decorative metalwork |
Tooling | V-dies and punches for bending | Punches and dies for cutting specific shapes |
Precision | High precision in bending angles | High accuracy in hole placement and shape consistency |
Automation | Manual or CNC-controlled | Often CNC-automated for high-speed operations |
Material Handling | Handles larger sheets of metal | Handles smaller or larger sheets, often for intricate work |
Output | Produces bent or folded components | Produces components with holes or cutouts |
Cost & Maintenance | Lower maintenance costs, requires skilled operators | Higher maintenance costs, cost-effective for high-volume production |
Industry Use | Automotive, aerospace, construction | Manufacturing, electronics, decorative metalwork |
Need help choosing the right press for your project? Contact our experts today for personalized advice!