CIP (Cold Isostatic Pressing) and HIP (Hot Isostatic Pressing) are both advanced manufacturing processes used to achieve high-density materials, but they differ significantly in their application, temperature, pressure medium, and outcomes. CIP operates at room temperature using liquid pressure, making it suitable for large or complex parts where uniform density is critical. HIP, on the other hand, combines high temperature and gas pressure to achieve near-theoretical density, making it ideal for high-performance applications like engineered ceramics or aerospace components. The choice between CIP and HIP depends on factors such as material type, desired density, and application requirements.
Key Points Explained:
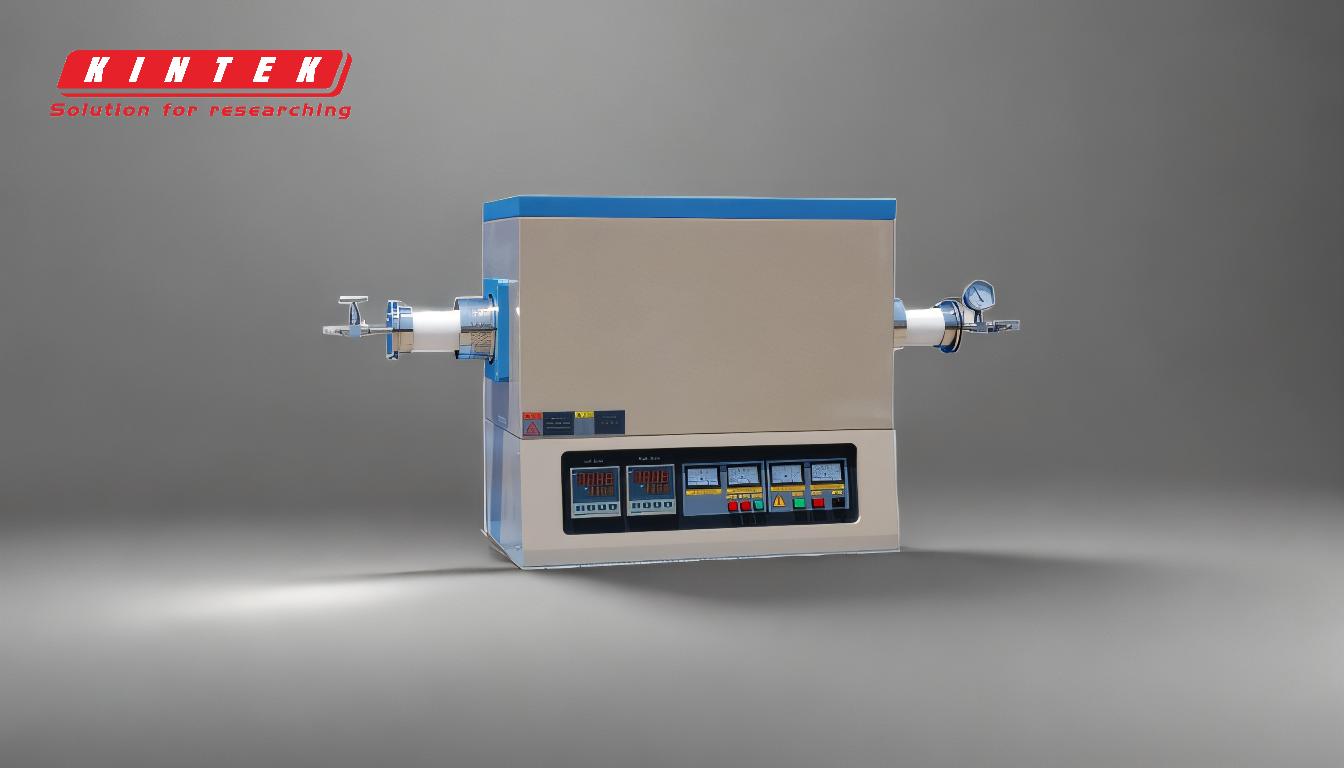
-
Temperature and Pressure Medium:
- CIP: Operates at room temperature using liquid pressure (typically water or oil). The process applies uniform pressure from all directions, ensuring high homogeneity and uniform density in the final product. This makes CIP ideal for materials that cannot withstand high temperatures.
- HIP: Combines high temperature (up to 2000°C) and gas pressure (using inert gases like argon or nitrogen). The simultaneous application of heat and pressure allows HIP to achieve nearly 100% theoretical density, making it suitable for high-performance materials like ceramics and superalloys.
-
Density and Material Properties:
- CIP: Produces parts with uniform density but typically lower than HIP. It is often used for preliminary shaping or when the material does not require extremely high density.
- HIP: Achieves densities exceeding 99%, minimizing voids and ensuring superior mechanical properties. This is particularly important for applications requiring high strength, fatigue resistance, and reliability, such as in aerospace or medical implants.
-
Applications:
- CIP: Commonly used for large or complex parts where the initial cost of tooling is prohibitive. It is also used for materials that are sensitive to high temperatures.
- HIP: Primarily used for high-performance applications, such as engineered ceramics, turbine blades, and critical aerospace components. The process is more expensive but provides unparalleled material properties.
-
Process Variants:
- WIP (Warm Isostatic Pressing): A hybrid between CIP and HIP, WIP uses warm water or a similar medium to apply pressure at temperatures below the boiling point of the liquid. This variant is useful for materials that benefit from moderate heating but do not require the extreme temperatures of HIP.
- Hot Pressing: Unlike HIP, hot pressing applies uniaxial pressure, which can lead to density variations due to friction between the powder and the mold. HIP, with its isostatic pressure, maintains the initial shape and uniformity of the material more effectively.
-
Cost and Complexity:
- CIP: Generally less expensive than HIP due to lower energy requirements and simpler equipment. It is a cost-effective solution for producing large or complex parts.
- HIP: More costly due to the need for high-temperature furnaces, gas pressure systems, and advanced controls. However, the superior material properties justify the expense for critical applications.
-
Material Behavior:
- CIP: Suitable for materials that do not require high-temperature sintering. The process is effective for achieving uniform density in green compacts before further processing.
- HIP: Ideal for materials that benefit from high-temperature densification, such as ceramics, metals, and composites. The process also improves grain structure and eliminates internal defects.
In summary, the choice between CIP and HIP depends on the specific requirements of the application, including material type, desired density, and performance criteria. Both processes leverage the principles of isostatic press to achieve uniform pressure, but their differences in temperature, pressure medium, and outcomes make them suitable for distinct applications.
Summary Table:
Aspect | CIP (Cold Isostatic Pressing) | HIP (Hot Isostatic Pressing) |
---|---|---|
Temperature | Room temperature | Up to 2000°C |
Pressure Medium | Liquid (water or oil) | Gas (argon or nitrogen) |
Density | Uniform but lower than HIP | Exceeds 99%, near-theoretical density |
Applications | Large/complex parts, temperature-sensitive materials | High-performance ceramics, aerospace components |
Cost | Lower cost, simpler equipment | Higher cost, advanced controls |
Material Suitability | Materials not requiring high-temperature sintering | Ceramics, metals, composites needing high density |
Still unsure which process is right for your application? Contact our experts today for personalized guidance!