In arc welding, the distinction between consumable and non-consumable electrodes lies in their role during the welding process. Consumable electrodes are designed to melt and become part of the weld pool, providing filler material to join the workpieces. Non-consumable electrodes, on the other hand, do not melt during welding; they are used to generate the arc and may require a separate filler material if needed. The choice between these electrodes depends on the welding process, material type, and desired weld characteristics. Below, the key differences, applications, and considerations for each type are explained in detail.
Key Points Explained:
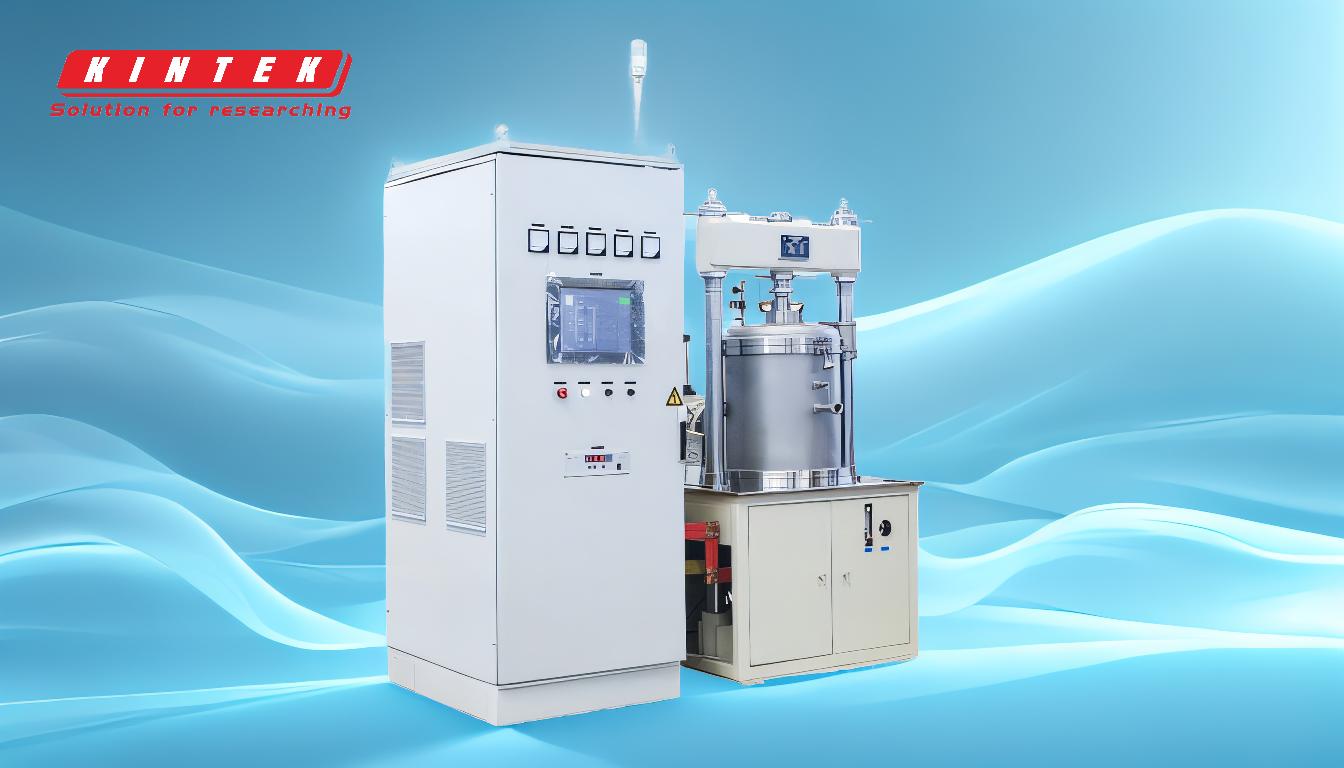
-
Definition and Function:
- Consumable Electrodes: These electrodes melt during the welding process and become part of the weld pool. They serve as both the heat source (arc generator) and the filler material. Examples include electrodes used in Shielded Metal Arc Welding (SMAW) and Gas Metal Arc Welding (GMAW).
- Non-Consumable Electrodes: These electrodes do not melt during welding. Their primary role is to generate the arc, and they may require a separate filler rod if additional material is needed. Examples include electrodes used in Tungsten Inert Gas (TIG) welding.
-
Material Composition:
- Consumable Electrodes: Typically made of materials that match or complement the base metal being welded. They are often coated with flux to stabilize the arc, protect the weld pool from contamination, and improve weld quality.
- Non-Consumable Electrodes: Made from materials with high melting points, such as tungsten or carbon. These materials are chosen for their ability to withstand high temperatures without melting.
-
Welding Processes:
- Consumable Electrodes: Commonly used in processes like SMAW, GMAW, and Flux-Cored Arc Welding (FCAW). These processes are suitable for a wide range of materials and thicknesses.
- Non-Consumable Electrodes: Primarily used in TIG welding, which is ideal for welding thin materials, non-ferrous metals, and applications requiring high precision and clean welds.
-
Advantages and Disadvantages:
-
Consumable Electrodes:
- Advantages: Higher deposition rates, suitable for thicker materials, and easier to use in outdoor or windy conditions due to flux coatings.
- Disadvantages: May produce slag that needs to be removed, and the weld quality can be affected by the electrode's consistency.
-
Non-Consumable Electrodes:
- Advantages: Produce clean, high-quality welds with minimal spatter, ideal for precision work and thin materials.
- Disadvantages: Slower deposition rates, requires more skill to operate, and often needs an external shielding gas.
-
Consumable Electrodes:
-
Applications:
- Consumable Electrodes: Widely used in construction, shipbuilding, and heavy fabrication due to their versatility and ability to weld thick materials.
- Non-Consumable Electrodes: Preferred in industries requiring high-quality welds, such as aerospace, automotive, and artisanal metalwork.
-
Cost and Maintenance:
- Consumable Electrodes: Generally more cost-effective for large-scale projects but require frequent replacement due to their consumable nature.
- Non-Consumable Electrodes: Higher initial cost but longer-lasting, as they do not melt. However, they may require periodic sharpening or replacement due to wear.
-
Shielding Requirements:
- Consumable Electrodes: Often come with flux coatings that provide shielding, reducing the need for external shielding gases in some processes.
- Non-Consumable Electrodes: Typically require external shielding gases (e.g., argon or helium) to protect the weld pool from atmospheric contamination.
-
Skill Level and Training:
- Consumable Electrodes: Easier to use for beginners, making them suitable for general-purpose welding.
- Non-Consumable Electrodes: Require more skill and training, particularly in controlling the arc and feeding the filler material manually in TIG welding.
By understanding these differences, a purchaser can make informed decisions based on the specific requirements of their welding projects, such as material type, thickness, desired weld quality, and available resources.
Summary Table:
Aspect | Consumable Electrodes | Non-Consumable Electrodes |
---|---|---|
Definition | Melt and become part of the weld pool, serving as filler material. | Do not melt; generate the arc and may require a separate filler rod. |
Material Composition | Made of materials matching the base metal, often coated with flux. | Made of high-melting-point materials like tungsten or carbon. |
Welding Processes | SMAW, GMAW, FCAW. | Primarily TIG welding. |
Advantages | Higher deposition rates, suitable for thick materials, easier to use outdoors. | Clean, high-quality welds, ideal for precision work and thin materials. |
Disadvantages | May produce slag; weld quality depends on electrode consistency. | Slower deposition rates; requires more skill and external shielding gas. |
Applications | Construction, shipbuilding, heavy fabrication. | Aerospace, automotive, artisanal metalwork. |
Cost & Maintenance | Cost-effective for large projects but requires frequent replacement. | Higher initial cost but longer-lasting; may need periodic sharpening or replacement. |
Shielding Requirements | Flux coatings provide shielding; less need for external gases. | Requires external shielding gases (e.g., argon or helium). |
Skill Level | Easier for beginners; suitable for general-purpose welding. | Requires more skill; ideal for precision and high-quality welds. |
Need help choosing the right electrode for your welding project? Contact our experts today for personalized advice!