Sintering is a critical process in materials science, used to create dense, solid materials from powders. Conventional sintering and microwave sintering are two distinct methods, each with unique mechanisms and advantages. Conventional sintering relies on external heat sources to gradually raise the temperature of the material, while microwave sintering uses electromagnetic waves to heat the material internally. This difference in heating mechanisms leads to variations in processing time, energy efficiency, and material properties. Below, we explore the key differences between these two methods, focusing on their mechanisms, advantages, and applications.
Key Points Explained:
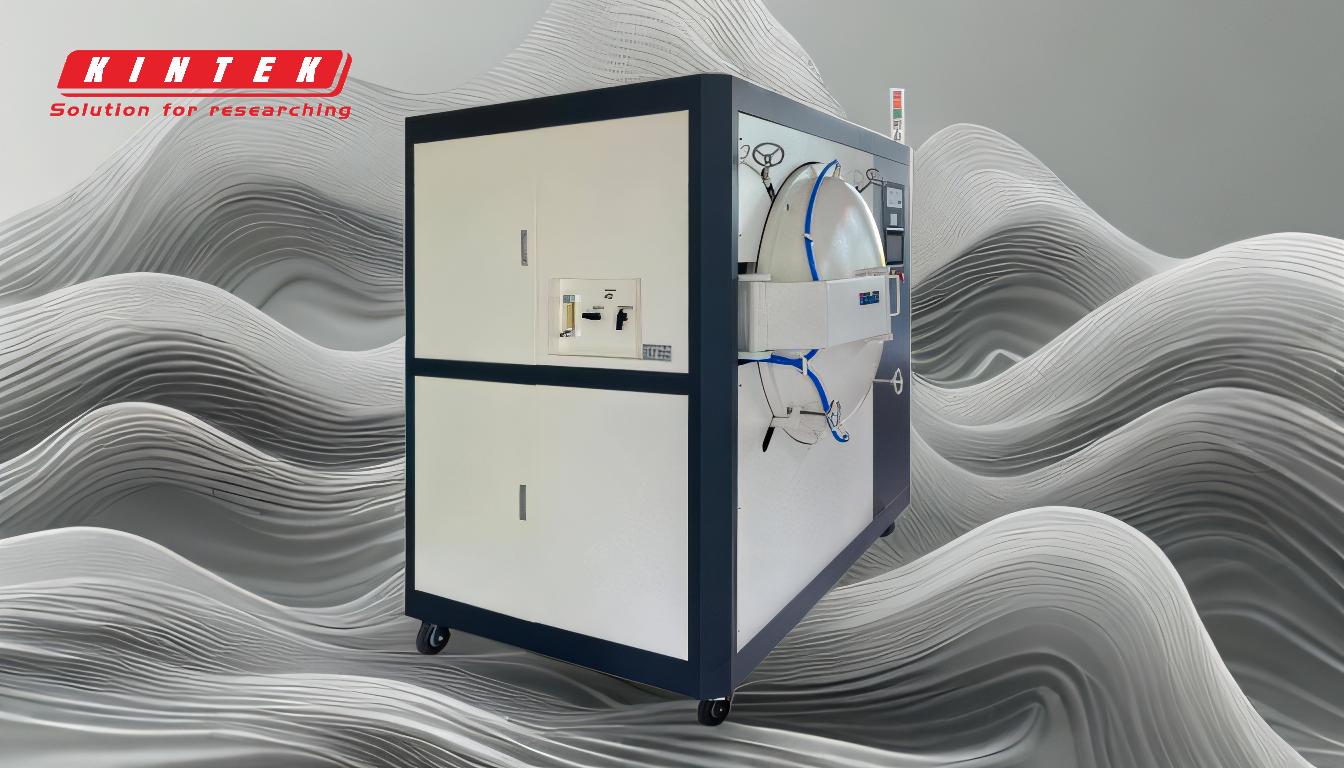
-
Heating Mechanism:
- Conventional Sintering: This method uses external heat sources, such as furnaces, to transfer heat to the material. The heat is conducted from the surface to the interior of the material, which can lead to temperature gradients and slower heating rates.
- Microwave Sintering: This method uses microwave radiation to directly interact with the material's molecules, causing them to vibrate and generate heat internally. This results in uniform heating throughout the material, reducing the risk of thermal gradients.
-
Processing Time:
- Conventional Sintering: Typically requires several hours to achieve the desired density and properties due to slower heating rates and the need for prolonged holding times at high temperatures.
- Microwave Sintering: Offers significantly faster heating rates, often reducing the sintering time to just a few minutes. This is due to the direct interaction of microwaves with the material, leading to rapid and efficient heating.
-
Energy Efficiency:
- Conventional Sintering: Generally less energy-efficient because a significant amount of energy is lost to the environment during the heating process.
- Microwave Sintering: More energy-efficient as the energy is directly absorbed by the material, minimizing energy loss and reducing overall energy consumption.
-
Material Properties:
- Conventional Sintering: Can result in coarser microstructures due to longer processing times, which may lead to grain growth and reduced mechanical properties.
- Microwave Sintering: Produces finer microstructures with improved mechanical properties, such as higher density and better grain uniformity. The rapid heating and cooling rates help in preserving the nanostructure of the material, leading to enhanced properties.
-
Environmental Impact:
- Conventional Sintering: Typically has a higher environmental impact due to longer processing times and higher energy consumption.
- Microwave Sintering: Offers a lower environmental impact due to reduced energy consumption and shorter processing times, making it a more sustainable option.
-
Applications:
- Conventional Sintering: Widely used in traditional powder metallurgy and ceramics industries where high temperatures and long processing times are acceptable.
- Microwave Sintering: Particularly advantageous for advanced materials, such as nanomaterials, where preserving fine microstructures and achieving high densities are crucial. It is also suitable for materials with enhanced magnetic, piezoelectric, thermoelectric, and biomedical properties.
In summary, while conventional sintering is a well-established method with broad applicability, microwave sintering offers significant advantages in terms of processing speed, energy efficiency, and material properties. The choice between the two methods depends on the specific requirements of the material and the desired properties of the final product.
Summary Table:
Aspect | Conventional Sintering | Microwave Sintering |
---|---|---|
Heating Mechanism | External heat sources (e.g., furnaces) | Internal heating via microwave radiation |
Processing Time | Several hours | Few minutes |
Energy Efficiency | Less efficient (energy loss to environment) | More efficient (direct energy absorption) |
Material Properties | Coarser microstructures, reduced mechanical properties | Finer microstructures, enhanced mechanical properties |
Environmental Impact | Higher impact (longer times, more energy) | Lower impact (shorter times, less energy) |
Applications | Traditional powder metallurgy, ceramics | Advanced materials, nanomaterials, biomedical |
Want to learn more about sintering methods? Contact our experts today for tailored solutions!