Chemical Vapor Deposition (CVD) and Plasma-Enhanced Chemical Vapor Deposition (PECVD) are both techniques used to deposit thin films onto substrates, but they differ significantly in their mechanisms, temperature requirements, and applications. Traditional CVD relies on thermal energy to drive chemical reactions for film deposition, typically at high temperatures (600°C to 800°C). In contrast, PECVD utilizes plasma to provide the energy needed for deposition, allowing it to operate at much lower temperatures (room temperature to 350°C). This makes PECVD ideal for temperature-sensitive substrates. Additionally, PECVD offers advantages such as low energy consumption, reduced pollution, and the ability to induce physical and chemical changes that are challenging to achieve with traditional CVD.
Key Points Explained:
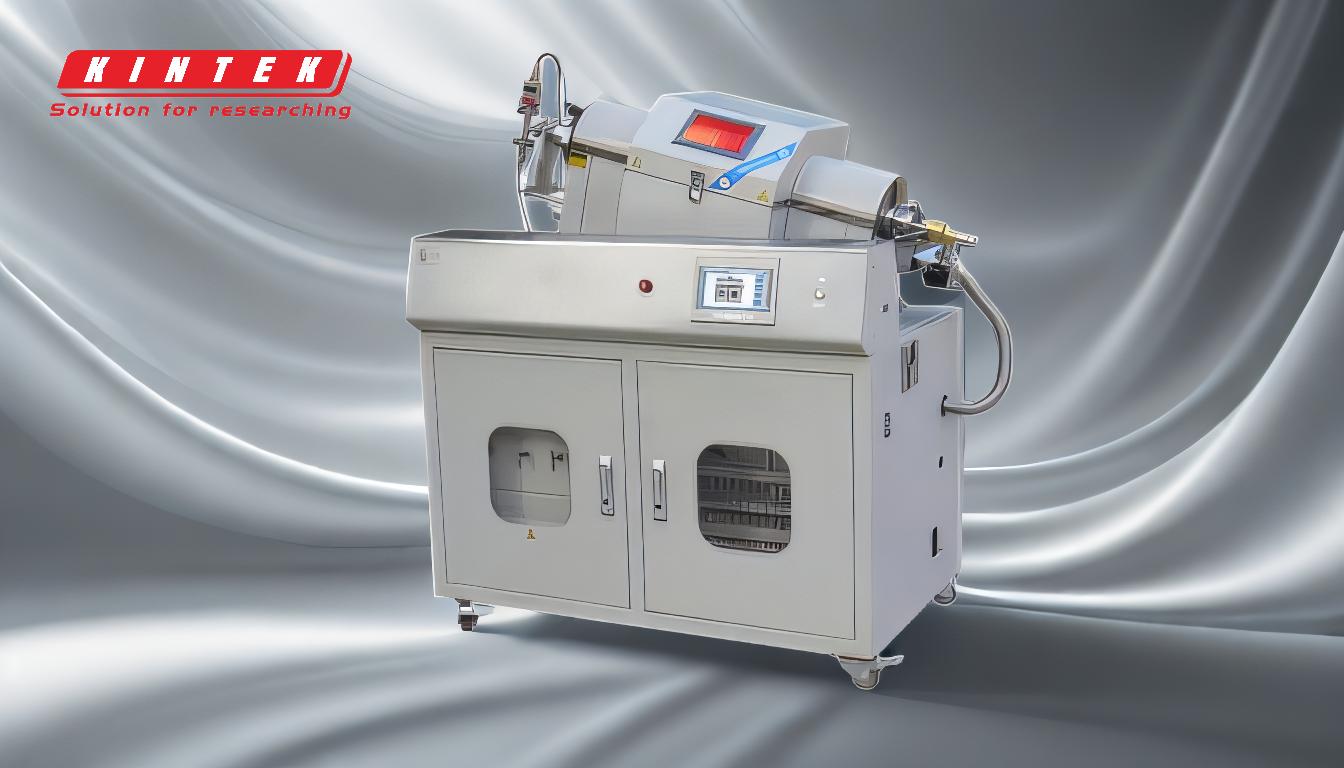
-
Deposition Mechanism:
- CVD: Traditional CVD relies on thermal energy to drive chemical reactions between gaseous precursors and the substrate surface. The high temperatures facilitate the decomposition of gases, leading to the formation of a solid film on the substrate.
- PECVD: PECVD introduces plasma into the process, which provides the necessary energy for chemical reactions. The plasma is a highly energetic state of matter consisting of ions, electrons, and neutral particles. This energy allows reactions to occur at much lower temperatures compared to CVD.
-
Temperature Requirements:
- CVD: Requires high temperatures, typically between 600°C to 800°C, which limits its use to substrates that can withstand such heat.
- PECVD: Operates at significantly lower temperatures, ranging from room temperature to 350°C. This makes it suitable for coating temperature-sensitive materials, such as polymers or certain electronic components.
-
Energy Source:
- CVD: Uses thermal energy exclusively to activate chemical reactions.
- PECVD: Utilizes plasma, which is generated by applying an electric field to a low-pressure gas. The plasma provides high energy density and active ion concentration, enabling reactions that are difficult to achieve with traditional CVD.
-
Advantages of PECVD:
- Low Deposition Temperature: Ideal for substrates that cannot tolerate high temperatures.
- Energy Efficiency: Lower energy consumption compared to CVD.
- Versatility: Can induce unique physical and chemical changes due to the high energy density of plasma.
- Environmental Benefits: Produces fewer pollutants compared to traditional CVD processes.
-
Applications:
- CVD: Commonly used in applications requiring high-quality, high-temperature-resistant films, such as semiconductor manufacturing and hard coatings for tools.
- PECVD: Preferred for applications involving temperature-sensitive substrates, such as flexible electronics, optical coatings, and biomedical devices.
-
Plasma Characteristics in PECVD:
- Plasma in PECVD is a non-equilibrium state, where electrons have much higher kinetic energy than ions and neutral particles. This allows for efficient activation of chemical reactions without significantly heating the substrate.
- The plasma is typically generated using low-pressure gas discharge, resulting in cold plasma. This type of plasma is characterized by:
- High electron energy relative to heavy particles.
- Ionization primarily caused by electron collisions with gas molecules.
- Energy loss compensated by the electric field between collisions.
By understanding these key differences, equipment and consumable purchasers can make informed decisions about which deposition method is best suited for their specific application requirements.
Summary Table:
Aspect | CVD | PECVD |
---|---|---|
Deposition Mechanism | Uses thermal energy to drive chemical reactions. | Utilizes plasma for energy, enabling reactions at lower temperatures. |
Temperature Range | 600°C to 800°C. | Room temperature to 350°C. |
Energy Source | Thermal energy. | Plasma generated by electric field in low-pressure gas. |
Advantages | High-quality, high-temperature-resistant films. | Low energy consumption, reduced pollution, and versatility. |
Applications | Semiconductor manufacturing, hard coatings. | Flexible electronics, optical coatings, biomedical devices. |
Need help choosing the right deposition method for your application? Contact our experts today!