High-frequency and low-frequency induction heating differ primarily in their frequency ranges, penetration depths, and applications. High-frequency induction heating operates between 60 kHz to 200 kHz (or up to 500 kHz in some references), with a shallow penetration depth of less than 2 mm, making it ideal for small workpieces and surface-level heating. It is fast, cost-effective, compact, and requires minimal space. In contrast, low-frequency (or medium-frequency) induction heating operates between 1 kHz to 10 kHz, offering deeper heat penetration, which is better suited for larger workpieces and bulk heating applications. The choice between the two depends on the workpiece size, heating depth requirements, and specific application needs.
Key Points Explained:
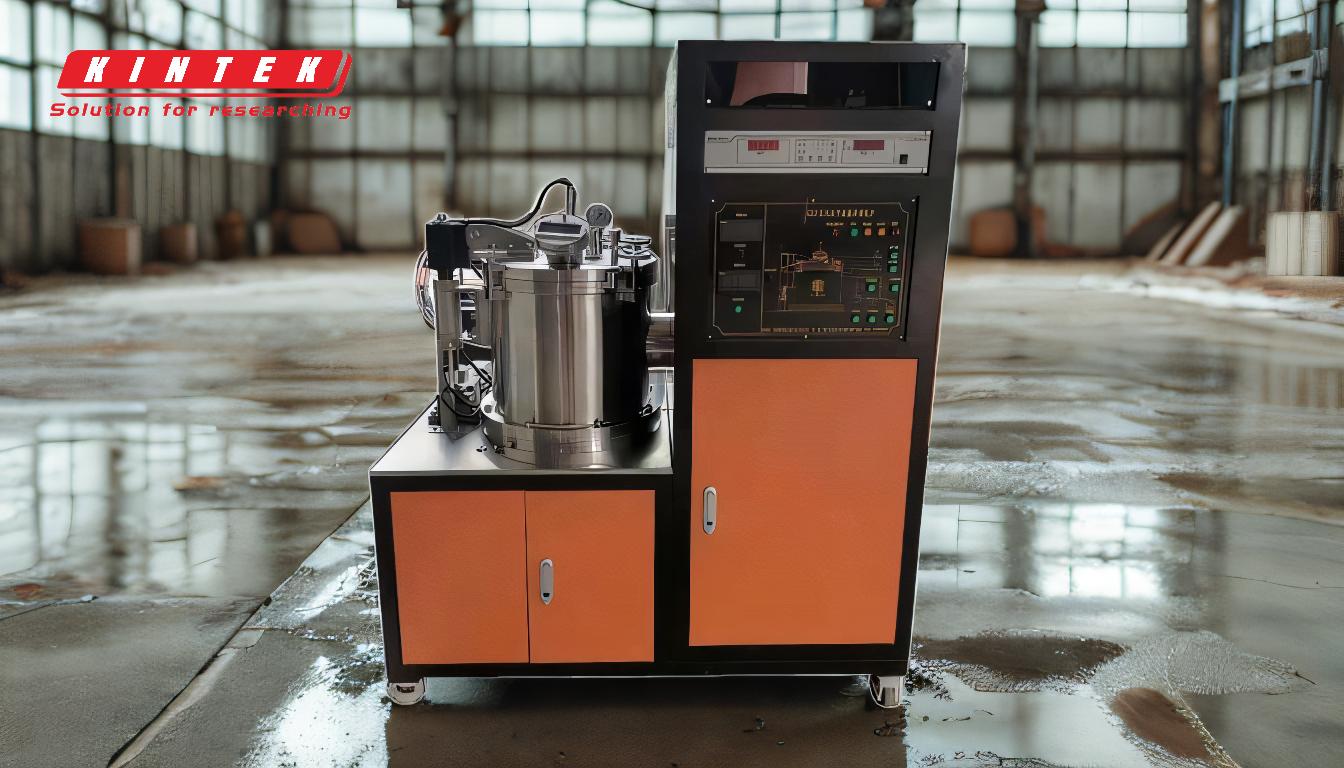
-
Frequency Range:
- High-Frequency Induction Heating: Operates between 60 kHz to 200 kHz, with some references extending the range up to 500 kHz.
- Low-Frequency (Medium-Frequency) Induction Heating: Operates between 1 kHz to 10 kHz.
- Implication: The frequency directly influences the depth of heat penetration and the suitability for different workpiece sizes.
-
Penetration Depth:
- High-Frequency Induction Heating: Has a shallow penetration depth of less than 2 mm, making it ideal for surface-level heating and small workpieces.
- Low-Frequency Induction Heating: Provides deeper heat penetration, making it suitable for larger workpieces and bulk heating applications.
- Implication: The penetration depth determines the type of workpiece and the heating requirements the machine can handle.
-
Applications:
- High-Frequency Induction Heating: Best for small workpieces, thin materials, and operations requiring shallow heating, such as surface hardening, brazing, or annealing.
- Low-Frequency Induction Heating: Suitable for large workpieces, thick materials, and applications requiring deep heating, such as forging, melting, or through-heating.
- Implication: The choice of frequency depends on the specific application and the desired heating effect.
-
Speed and Efficiency:
- High-Frequency Induction Heating: Characterized by being fast and efficient, making it ideal for high-speed production processes.
- Low-Frequency Induction Heating: Slower but more effective for deeper heating applications.
- Implication: High-frequency heating is preferred for quick, surface-level processes, while low-frequency heating is better for slower, deeper heating tasks.
-
Cost and Size:
- High-Frequency Induction Heating: Generally cheaper, smaller in size, and requires less space, making it suitable for compact operations.
- Low-Frequency Induction Heating: Typically larger and more expensive due to the need for deeper penetration and handling larger workpieces.
- Implication: High-frequency machines are more cost-effective and space-efficient, while low-frequency machines are better suited for heavy-duty applications.
-
Workpiece Suitability:
- High-Frequency Induction Heating: Ideal for small, thin, or delicate workpieces where precise, shallow heating is required.
- Low-Frequency Induction Heating: Better for large, thick, or heavy workpieces requiring uniform, deep heating.
- Implication: The size and material of the workpiece dictate the choice of induction heating frequency.
By understanding these key differences, equipment purchasers can make informed decisions based on their specific heating requirements, workpiece characteristics, and production goals.
Summary Table:
Aspect | High-Frequency Induction Heating | Low-Frequency Induction Heating |
---|---|---|
Frequency Range | 60 kHz to 200 kHz (up to 500 kHz in some cases) | 1 kHz to 10 kHz |
Penetration Depth | Less than 2 mm (shallow) | Deeper heat penetration |
Applications | Small workpieces, thin materials, surface-level heating | Large workpieces, thick materials, bulk heating |
Speed and Efficiency | Fast and efficient | Slower but effective for deeper heating |
Cost and Size | Cheaper, compact, and space-efficient | Larger and more expensive |
Workpiece Suitability | Small, thin, or delicate workpieces | Large, thick, or heavy workpieces |
Need help choosing the right induction heating solution? Contact us today for expert advice!