Hot isostatic pressing (HIP) and cold isostatic pressing (CIP) are two advanced manufacturing processes used to densify and strengthen materials, but they differ significantly in terms of temperature, pressure, and application. HIP involves high temperatures and pressures, typically using inert gases, to eliminate porosity and improve material properties in a single step. It is ideal for producing high-performance components with superior mechanical properties. On the other hand, CIP operates at room or slightly elevated temperatures, using liquid media to form "raw" parts that require subsequent sintering. CIP is suitable for larger parts, complex shapes, and materials that do not require high precision in their sintered state. Both processes offer uniform pressure application, but their specific conditions and outcomes cater to different industrial needs.
Key Points Explained:
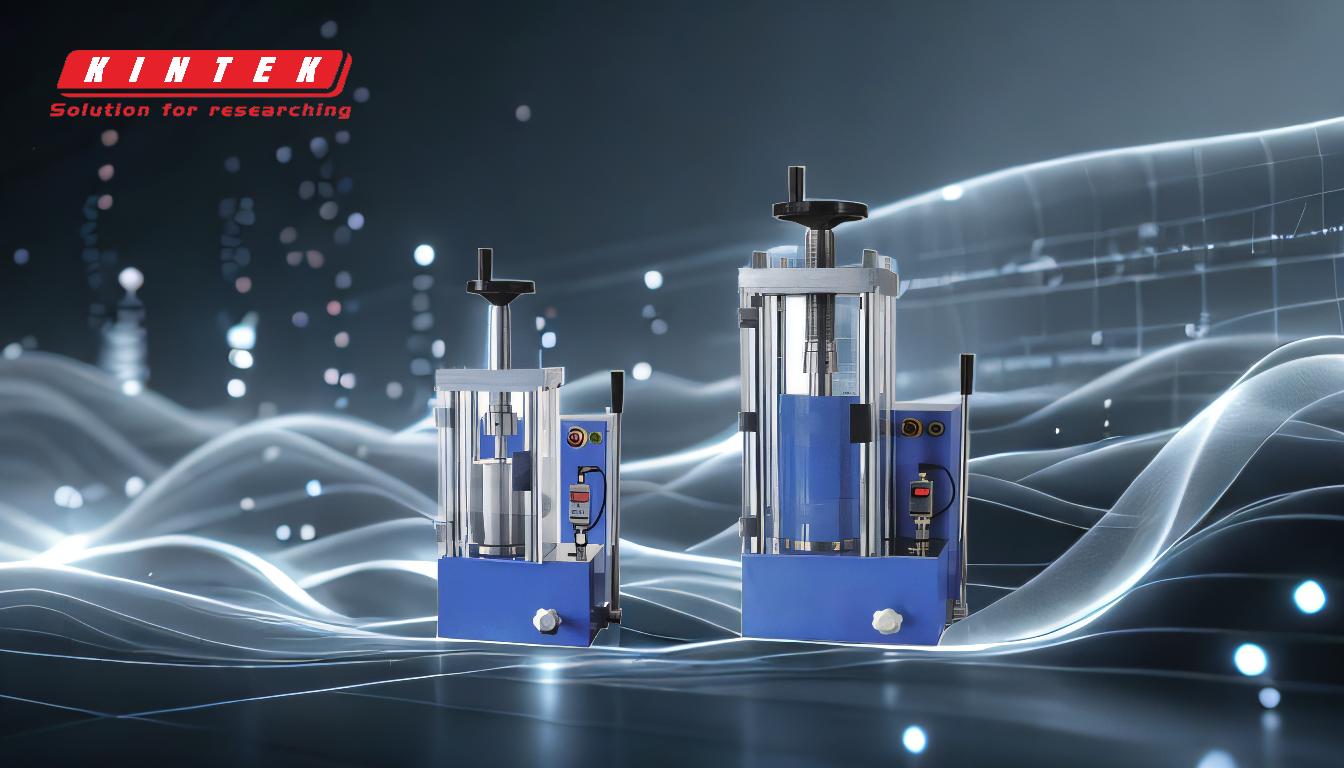
-
Temperature and Pressure Conditions:
- Hot Isostatic Pressing (HIP): Operates at elevated temperatures (up to 2000°F or 1100°C) and high pressures (up to 15,000 lb/in² or 100 MPa). The process uses inert gases like argon or glass-like fluids to simultaneously apply heat and pressure, eliminating porosity and enhancing material density in a single step.
- Cold Isostatic Pressing (CIP): Conducted at room temperature or slightly higher (<93°C) with liquid media such as water, oil, or glycol mixtures. It forms "raw" parts that require additional sintering to achieve final strength and density.
-
Material Applications:
- HIP: Primarily used for densification and improving mechanical properties in metals, ceramics, polymers, and composite materials. It is ideal for high-performance applications such as aerospace components, medical implants, and advanced ceramics.
- CIP: Commonly used for consolidating ceramic powders, graphite, refractory materials, and electrical insulators. It is suitable for wear-resistant tools, metal forming tools, and advanced ceramics like silicon nitride and boron carbide.
-
Process Outcomes:
- HIP: Produces parts with superior mechanical properties, such as increased strength, toughness, and fatigue resistance. It eliminates porosity and achieves near-net-shape components with high precision.
- CIP: Forms parts with sufficient green strength for handling and further processing. The final properties are achieved after sintering, making it suitable for less precise but complex shapes.
-
Equipment and Media:
- HIP: Utilizes molds made from sheet metal or ceramics and employs inert gases or glass-like fluids as pressure media. The process requires specialized high-temperature and high-pressure equipment.
- CIP: Uses elastic rubber or plastic molds and liquid media like water or oil. The cold isostatic pressing machine is designed for room-temperature operations, making it more accessible for a wide range of industrial applications.
-
Industrial Suitability:
- HIP: Best for high-value, high-performance components where material integrity and precision are critical. It is often used in industries like aerospace, automotive, and medical devices.
- CIP: Ideal for large-scale production of complex shapes, long thin-walled products, and materials that do not require high precision in their sintered state. It is widely used in the ceramics, refractory, and tooling industries.
-
Advantages and Limitations:
- HIP: Offers superior material properties and near-net-shape capabilities but requires expensive equipment and energy-intensive processes.
- CIP: Provides cost-effective solutions for forming complex shapes and large parts but requires additional sintering steps to achieve final properties.
By understanding these key differences, manufacturers can choose the appropriate isostatic pressing method based on their specific material requirements, production scale, and desired outcomes.
Summary Table:
Aspect | Hot Isostatic Pressing (HIP) | Cold Isostatic Pressing (CIP) |
---|---|---|
Temperature | High (up to 2000°F / 1100°C) | Room temperature or slightly elevated (<93°C) |
Pressure | High (up to 15,000 lb/in² / 100 MPa) | Moderate (liquid media) |
Media | Inert gases or glass-like fluids | Water, oil, or glycol mixtures |
Applications | Aerospace, medical implants, advanced ceramics | Ceramics, refractory materials, wear-resistant tools |
Outcomes | Superior mechanical properties, near-net-shape components | Green strength for handling, requires sintering for final properties |
Industrial Suitability | High-value, high-performance components | Large-scale production, complex shapes |
Advantages | Eliminates porosity, enhances density, and improves material properties | Cost-effective, suitable for large and complex parts |
Limitations | Expensive equipment, energy-intensive | Requires additional sintering steps |
Need help choosing the right isostatic pressing method for your project? Contact our experts today!