Hot pressing and Hot Isostatic Pressing (HIP) are both advanced manufacturing techniques used to densify materials, but they differ significantly in their processes, outcomes, and applications. Hot pressing involves applying uniaxial pressure and heat to a material, typically resulting in densities ranging from 65% to 99%. It is simpler and less expensive but often produces billet shapes with less uniform density. In contrast, HIP uses isostatic pressure (applied uniformly from all directions) combined with high temperatures, achieving densities exceeding 99% and minimizing voids. HIP is more costly but excels in producing complex shapes with near-net dimensional tolerances and superior material properties. Both methods are suited for different applications, with hot pressing being more economical for simpler forms and HIP preferred for high-performance, complex components.
Key Points Explained:
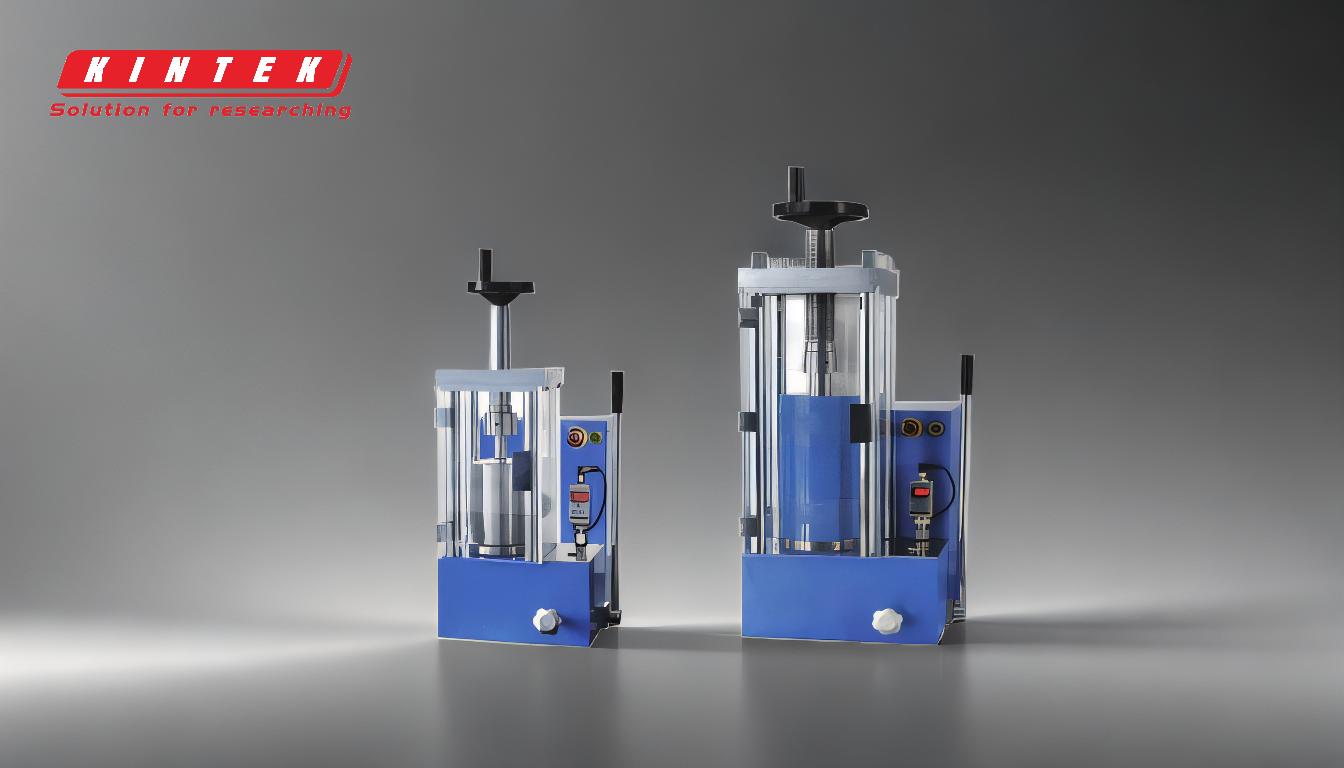
-
Density and Uniformity:
- Hot Pressing: Achieves densities ranging from 65% to 99%, depending on the material. The process is less consistent, often resulting in uneven density and the presence of voids.
- Hot Isostatic Pressing (HIP): Yields densities exceeding 99% and ensures uniform density throughout the material. HIP is particularly effective in minimizing voids, making it ideal for high-performance applications.
-
Temperature and Pressure Application:
- Hot Pressing: Applies uniaxial pressure (pressure from one direction) combined with heat. This method is simpler but less effective in achieving uniform density.
- Hot Isostatic Pressing (HIP): Uses isostatic pressure, which is applied uniformly from all directions, combined with high temperatures. This results in more consistent material properties and higher density.
-
Complexity of Shapes:
- Hot Pressing: Typically produces billet shapes or simpler forms due to the limitations of uniaxial pressure.
- Hot Isostatic Pressing (HIP): Capable of producing complex shapes, which is a significant advantage over hot pressing. However, the dimensional tolerances in HIP are generally near-net due to the use of flexible molds.
-
Cost and Applications:
- Hot Pressing: More economical and suitable for applications where cost is a primary concern and simpler shapes are acceptable.
- Hot Isostatic Pressing (HIP): More expensive but preferred for high-performance applications requiring complex shapes, uniform density, and superior material properties.
-
Material Properties:
- Hot Pressing: May result in materials with less uniform properties and higher porosity, which can affect performance in demanding applications.
- Hot Isostatic Pressing (HIP): Produces materials with minimal porosity and highly uniform properties, making it suitable for critical applications in aerospace, medical, and other high-tech industries.
By understanding these key differences, equipment and consumable purchasers can make informed decisions based on the specific requirements of their applications, balancing cost, complexity, and performance needs.
Summary Table:
Aspect | Hot Pressing | Hot Isostatic Pressing (HIP) |
---|---|---|
Density | 65% to 99%, less uniform | Exceeds 99%, highly uniform |
Pressure Application | Uniaxial (one direction) | Isostatic (uniform from all directions) |
Shape Complexity | Simpler billet shapes | Complex shapes with near-net tolerances |
Cost | Economical | More expensive |
Applications | Suitable for simpler forms | Preferred for high-performance, complex components |
Material Properties | Less uniform, higher porosity | Minimal porosity, highly uniform properties |
Need help choosing the right densification method for your application? Contact our experts today for personalized advice!