Chemical Vapor Deposition (CVD) is a widely used technique for depositing thin films onto substrates, and it can be categorized into hot wall CVD and cold wall CVD based on how the substrate and reactor walls are heated. Hot wall CVD involves heating both the substrate and the reactor walls to similar temperatures, which simplifies the process and is cost-effective but can lead to unwanted deposition on the reactor walls. Cold wall CVD, on the other hand, heats only the substrate, minimizing deposition on the reactor walls but introducing challenges like temperature gradients and gas flow issues. Understanding the differences between these methods is crucial for selecting the right approach for specific applications.
Key Points Explained:
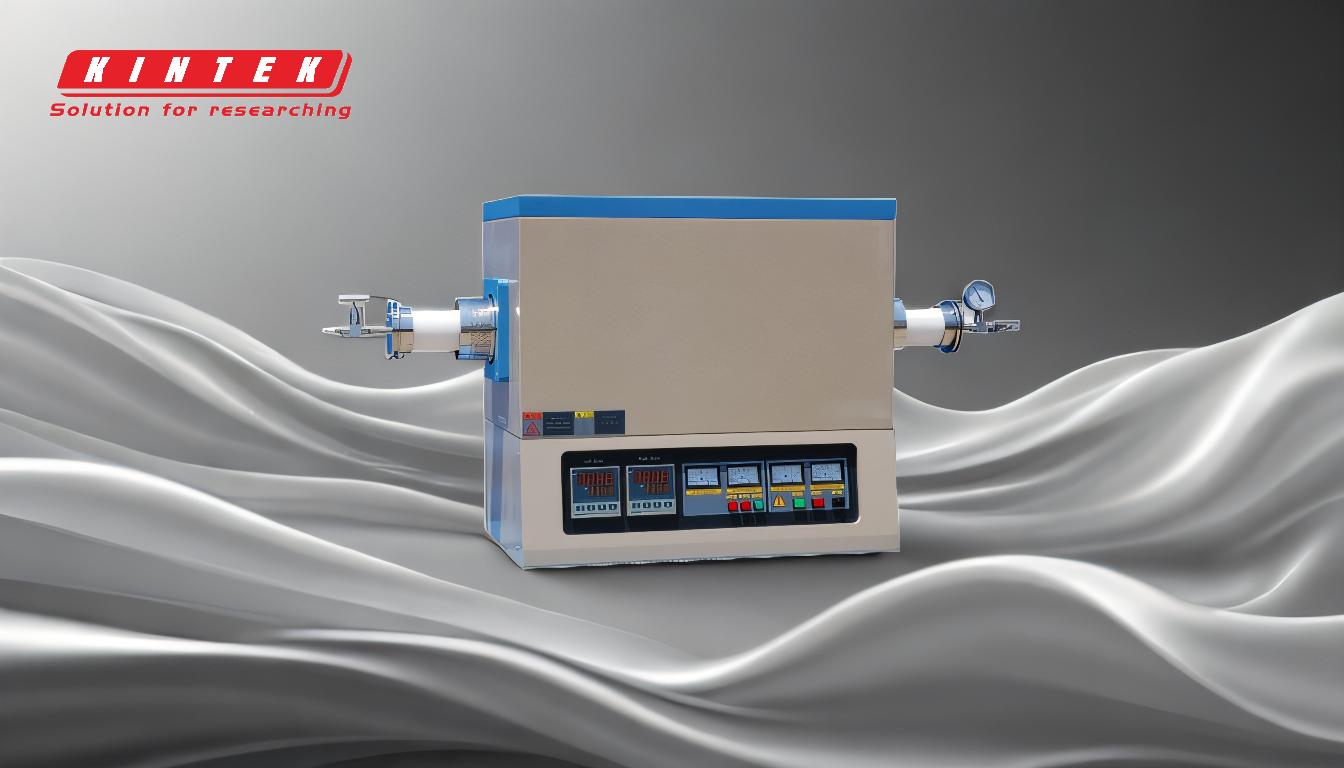
-
Heating Mechanism:
- Hot Wall CVD: Both the substrate and the reactor walls are heated to comparable temperatures. This ensures uniform heating but can lead to deposition on the reactor walls, which may cause contamination or non-uniformity in the deposited film.
- Cold Wall CVD: Only the substrate is heated, typically using a graphite susceptor, while the reactor walls remain cooler. This minimizes deposition on the walls but can create large temperature gradients near the substrate, affecting gas flow and deposition uniformity.
-
Deposition Uniformity:
- Hot Wall CVD: The uniform heating of both the substrate and reactor walls can lead to more consistent deposition across the substrate. However, deposition on the reactor walls can result in powders or flakes falling onto the substrate, potentially causing defects.
- Cold Wall CVD: By heating only the substrate, cold wall reactors reduce the risk of deposition on the reactor walls. However, the temperature gradients near the substrate can lead to non-uniform deposition, especially in large-scale applications.
-
Process Complexity and Cost:
- Hot Wall CVD: This method is generally simpler to implement and more cost-effective, making it suitable for batch processing. The mature technology and lower equipment costs are significant advantages.
- Cold Wall CVD: While more complex due to the need for precise control of substrate heating and cooling, cold wall CVD offers greater flexibility in controlling deposition conditions, which can be crucial for certain high-precision applications.
-
Applications:
- Hot Wall CVD: Commonly used in applications where cost and simplicity are more critical than achieving the highest levels of deposition uniformity. It is well-suited for batch processing and applications where minor contamination from reactor wall deposition is acceptable.
- Cold Wall CVD: Preferred for applications requiring high precision and minimal contamination, such as in the semiconductor industry. The ability to control cooling rates and minimize deposition on reactor walls makes it ideal for high-performance materials.
-
Comparison with Other Techniques:
- CVD vs. PVD: While CVD relies on chemical reactions to deposit materials, Physical Vapor Deposition (PVD) involves the physical vaporization of materials. CVD is typically used for ceramics and polymers, whereas PVD can deposit a broader range of materials, including metals and alloys. CVD coatings are denser and more uniform but take longer to apply compared to PVD coatings.
- Short Path Vacuum Distillation: This technique, often used in molecular distillation, involves reducing pressure to ensure that the mean free path of molecules is longer than the distance between the evaporator and condenser, eliminating back-pressure. This is different from CVD but shares the goal of precise material deposition or separation. For more details, see short path vacuum distillation.
In summary, the choice between hot wall CVD and cold wall CVD depends on the specific requirements of the application, including the need for deposition uniformity, contamination control, and process complexity. Hot wall CVD offers simplicity and cost-effectiveness, while cold wall CVD provides greater precision and control, making it suitable for high-performance applications.
Summary Table:
Aspect | Hot Wall CVD | Cold Wall CVD |
---|---|---|
Heating Mechanism | Heats both substrate and reactor walls uniformly | Heats only the substrate, keeping reactor walls cooler |
Deposition Uniformity | Uniform deposition but risks contamination from reactor wall deposition | Minimizes reactor wall deposition but may face temperature gradient challenges |
Process Complexity | Simpler and cost-effective, ideal for batch processing | More complex, requires precise control of heating and cooling |
Applications | Suitable for cost-sensitive applications with minor contamination risks | Preferred for high-precision applications like semiconductor manufacturing |
Need help choosing the right CVD method for your application? Contact our experts today for personalized guidance!