Molecular Beam Epitaxy (MBE) and Metal-Organic Chemical Vapor Deposition (MOCVD) are two advanced techniques used for thin-film deposition, particularly in the semiconductor industry. While both methods are used to grow high-quality thin films, they differ significantly in their operational principles, equipment, and applications. MBE is a physical vapor deposition technique that operates under ultra-high vacuum conditions, using atomic or molecular beams to deposit materials onto a substrate. In contrast, MOCVD is a chemical vapor deposition method that relies on chemical reactions between gaseous precursors to form thin films. Below, we explore these differences in detail.
Key Points Explained:
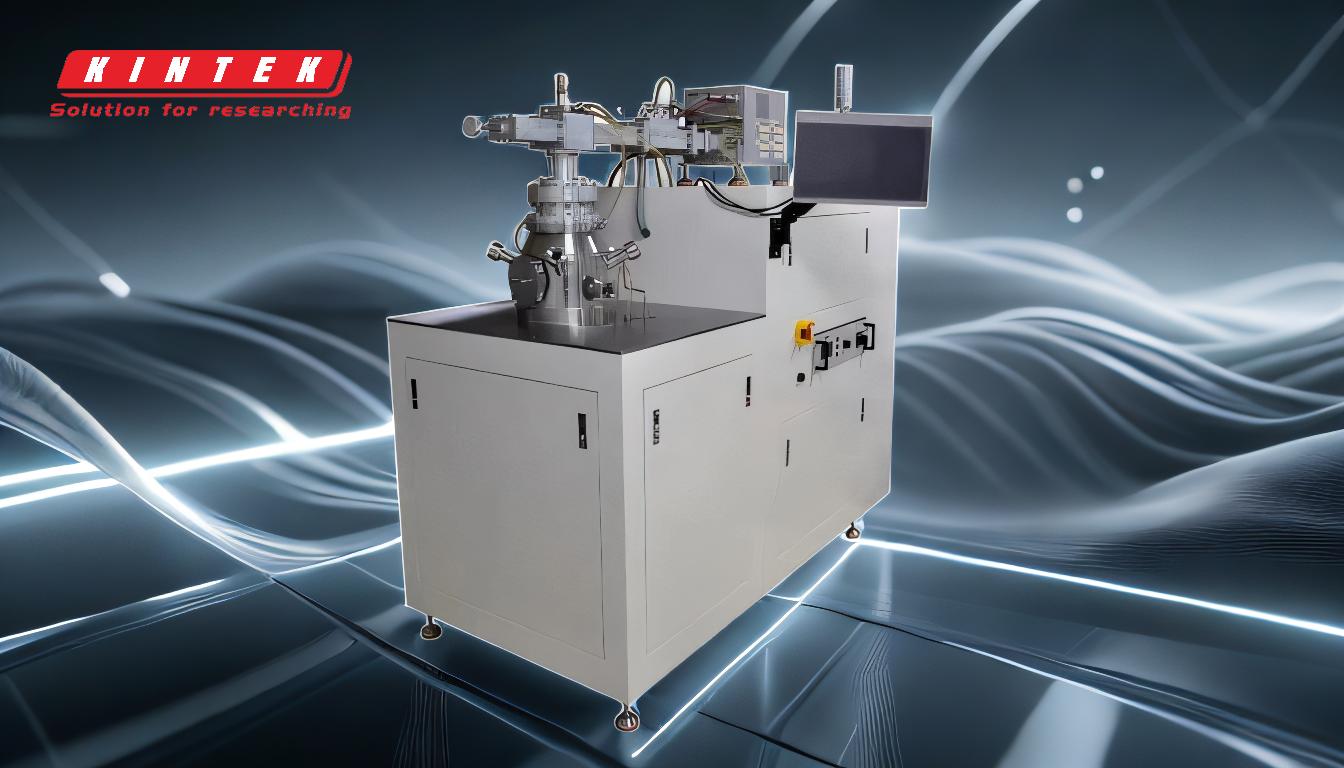
-
Operational Principles:
- MBE: MBE is a physical process where materials are evaporated in a high vacuum environment and directed as a beam onto a substrate. The process involves the use of effusion cells to produce atomic or molecular beams, which are then deposited layer by layer on the substrate.
- MOCVD: MOCVD is a chemical process where metal-organic precursors and other reactive gases are introduced into a reaction chamber. These gases undergo chemical reactions at the substrate surface, leading to the deposition of thin films.
-
Vacuum Requirements:
- MBE: MBE requires ultra-high vacuum conditions (typically around 10^-10 to 10^-12 Torr) to ensure that the atomic or molecular beams travel without scattering and to minimize contamination.
- MOCVD: MOCVD operates at much higher pressures (typically around 10^-2 to 10^2 Torr) compared to MBE. The process does not require an ultra-high vacuum, but it does need a controlled environment to manage the chemical reactions effectively.
-
Precursor Types:
- MBE: In MBE, solid sources are used, and the materials are typically elemental (e.g., gallium, arsenic). These materials are heated to produce atomic or molecular beams.
- MOCVD: MOCVD uses metal-organic precursors (e.g., trimethylgallium, trimethylaluminum) and other reactive gases (e.g., ammonia, arsine). These precursors are volatile and react at the substrate surface to form the desired thin films.
-
Deposition Rate and Control:
- MBE: MBE offers precise control over the deposition process, with very low deposition rates (typically around 1 monolayer per second). This allows for the growth of extremely thin and uniform layers, making it ideal for research and development of advanced materials.
- MOCVD: MOCVD generally has higher deposition rates compared to MBE, making it more suitable for industrial-scale production. However, the control over layer thickness and uniformity is not as precise as in MBE.
-
Applications:
- MBE: MBE is commonly used in research and development for growing high-quality, defect-free thin films, particularly in the fabrication of quantum wells, superlattices, and other nanostructures. It is also used in the production of high-performance optoelectronic devices, such as lasers and photodetectors.
- MOCVD: MOCVD is widely used in the mass production of semiconductor devices, including light-emitting diodes (LEDs), laser diodes, and solar cells. It is also used for growing compound semiconductor materials like gallium nitride (GaN) and indium phosphide (InP).
-
Equipment Complexity and Cost:
- MBE: MBE systems are highly complex and expensive due to the need for ultra-high vacuum conditions, precise control mechanisms, and specialized effusion cells. The maintenance and operation of MBE systems require significant expertise.
- MOCVD: MOCVD systems are generally less complex and less expensive than MBE systems. The process is more scalable and easier to implement for large-scale production, though it still requires careful control of gas flows and temperatures.
-
Material Purity and Quality:
- MBE: MBE is known for producing high-purity, high-quality thin films with excellent control over stoichiometry and defect density. The ultra-high vacuum environment minimizes contamination, leading to superior material properties.
- MOCVD: While MOCVD also produces high-quality films, the presence of chemical precursors and reactive gases can introduce impurities or defects. However, modern MOCVD systems have advanced significantly in controlling these factors, making it possible to achieve high-quality films suitable for many applications.
In summary, MBE and MOCVD are both essential techniques for thin-film deposition, but they cater to different needs and applications. MBE excels in precision and material quality, making it ideal for research and high-performance devices. In contrast, MOCVD is more suited for industrial-scale production due to its higher deposition rates and scalability. Understanding these differences is crucial for selecting the appropriate method based on the specific requirements of the application.
Summary Table:
Aspect | MBE | MOCVD |
---|---|---|
Operational Principle | Physical vapor deposition in ultra-high vacuum | Chemical vapor deposition using metal-organic precursors |
Vacuum Requirements | Ultra-high vacuum (10^-10 to 10^-12 Torr) | Higher pressures (10^-2 to 10^2 Torr) |
Precursor Types | Solid sources (e.g., gallium, arsenic) | Metal-organic precursors (e.g., trimethylgallium, ammonia) |
Deposition Rate | Low (1 monolayer/second), precise control | Higher, suitable for industrial-scale production |
Applications | Research, quantum wells, optoelectronic devices | LEDs, laser diodes, solar cells, GaN, InP |
Equipment Complexity | High complexity and cost, requires expertise | Less complex, scalable for large-scale production |
Material Quality | High purity, defect-free films | High-quality films, but potential for impurities |
Need help choosing between MBE and MOCVD for your project? Contact our experts today!