Mechanical presses and hydraulic presses are two distinct types of equipment used in various industries for pressing, forming, and shaping materials. The primary differences lie in their mechanisms, operational efficiency, and suitability for specific tasks. Mechanical presses use mechanical force, often driven by a motor and flywheel, to generate pressure, while hydraulic presses rely on hydraulic fluid to create force. Each type has its advantages and limitations, depending on the application, precision requirements, and workflow demands.
Key Points Explained:
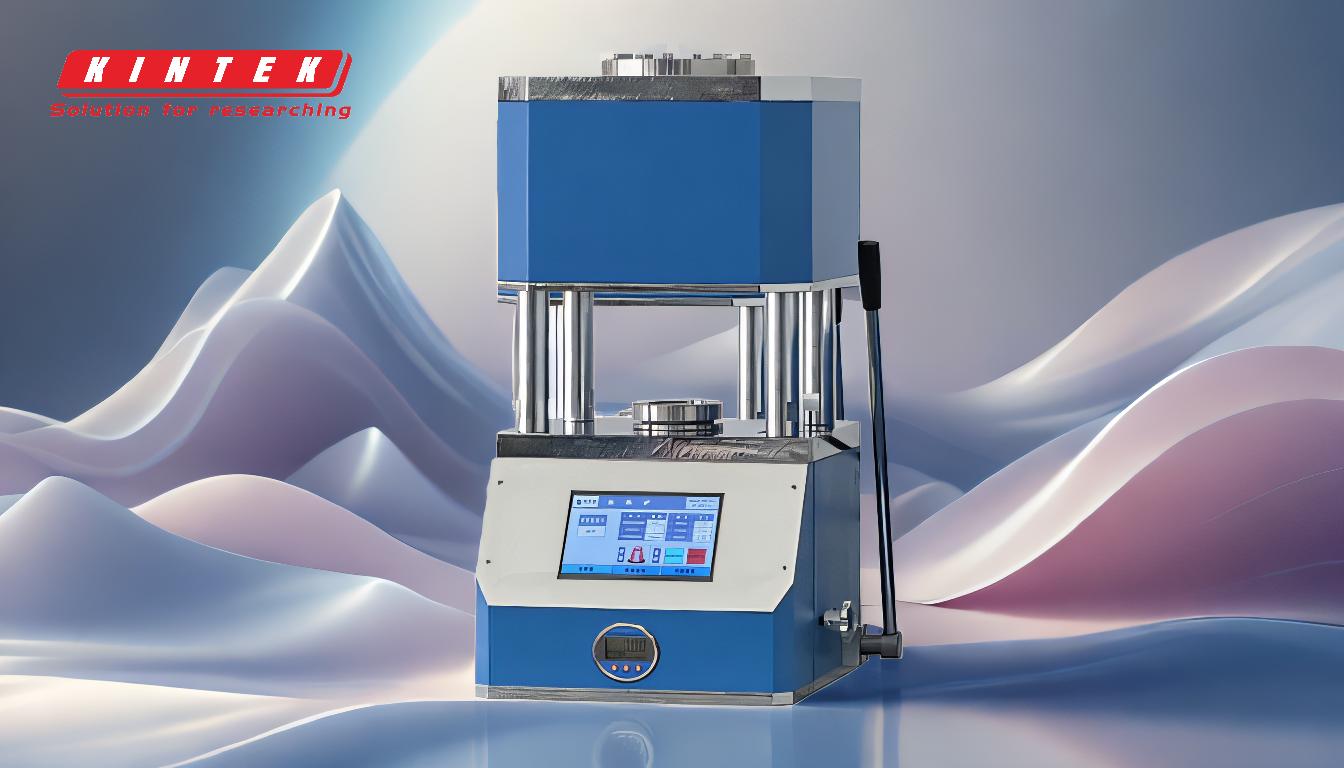
-
Mechanism of Operation:
- Mechanical Presses: These presses operate using a motor-driven flywheel and a mechanical linkage system (such as a crank or eccentric mechanism) to convert rotational motion into linear force. The force is applied in a controlled, repetitive manner, making them ideal for high-speed operations.
- Hydraulic Presses: These presses use hydraulic fluid to generate force. A pump moves the fluid into a cylinder, creating pressure that drives a piston to apply force. Hydraulic presses are known for their ability to deliver consistent and precise pressure over a wide range of loads.
-
Force Application:
- Mechanical Presses: The force in mechanical presses is typically applied in a single stroke, which is determined by the design of the press. This makes them suitable for tasks requiring high-speed, repetitive operations, such as stamping or punching.
- Hydraulic Presses: Hydraulic presses can apply force over a longer stroke and maintain consistent pressure throughout the operation. This makes them ideal for tasks requiring precise control, such as molding or deep drawing.
-
Speed and Efficiency:
- Mechanical Presses: These presses are generally faster and more efficient for high-volume production tasks. Their mechanical nature allows for rapid cycling, which is beneficial in industries like automotive manufacturing.
- Hydraulic Presses: While slower in terms of cycling speed, hydraulic presses offer greater flexibility and control. They are better suited for applications requiring variable pressure or complex forming processes.
-
Precision and Control:
- Mechanical Presses: Precision in mechanical presses is limited by the mechanical linkages and the fixed nature of the stroke. They are less adaptable to changes in pressure or stroke length during operation.
- Hydraulic Presses: Hydraulic presses excel in precision and control. The pressure can be finely tuned, and the stroke length can be adjusted dynamically, making them suitable for applications requiring high accuracy.
-
Cost and Maintenance:
- Mechanical Presses: These presses are often less expensive to purchase and maintain due to their simpler mechanical design. However, they may require more frequent maintenance due to wear and tear on mechanical components.
- Hydraulic Presses: Hydraulic presses tend to have higher initial costs and require regular maintenance of the hydraulic system, including fluid changes and seal replacements. However, they offer longer service life and greater reliability in demanding applications.
-
Applications:
- Mechanical Presses: Commonly used in high-speed manufacturing processes such as stamping, blanking, and forging. They are ideal for applications where speed and repeatability are critical.
- Hydraulic Presses: Widely used in applications requiring precise force control, such as molding, laminating, and deep drawing. They are also preferred for tasks involving large or irregularly shaped materials.
-
Manual vs. Automatic Operation:
- Manual Hydraulic Presses: These are operated using a hand lever and are more affordable but require physical effort. They are suitable for low-volume or occasional use.
- Automatic Hydraulic Presses: These use a pump and automated controller to apply consistent pressure, making them more efficient and less labor-intensive. They are ideal for high-volume or precision-critical applications.
In summary, the choice between mechanical and hydraulic presses depends on the specific requirements of the task, including speed, precision, and the nature of the materials being processed. Mechanical presses are better suited for high-speed, repetitive tasks, while hydraulic presses offer greater flexibility and control for complex or precision-oriented applications.
Summary Table:
Aspect | Mechanical Presses | Hydraulic Presses |
---|---|---|
Mechanism | Motor-driven flywheel and mechanical linkage system | Hydraulic fluid and piston system |
Force Application | Single stroke, ideal for high-speed, repetitive tasks | Longer stroke, consistent pressure for precise control |
Speed | Faster, suited for high-volume production | Slower, but offers greater flexibility and control |
Precision | Limited by mechanical linkages and fixed stroke | High precision with adjustable pressure and stroke length |
Cost | Lower initial cost, simpler maintenance | Higher initial cost, requires regular hydraulic system maintenance |
Applications | Stamping, blanking, forging | Molding, laminating, deep drawing |
Operation | High-speed, repetitive tasks | Complex or precision-oriented tasks |
Need help choosing the right press for your application? Contact our experts today for personalized advice!