PECVD (Plasma-Enhanced Chemical Vapor Deposition) and CVD (Chemical Vapor Deposition) are both techniques used to deposit thin films onto substrates, but they differ significantly in their processes, temperature requirements, and applications. The primary distinction lies in the use of plasma in PECVD, which allows for lower temperature deposition compared to traditional CVD. This plasma provides the activation energy needed for chemical reactions, enabling the process to occur at reduced temperatures. Additionally, PECVD offers advantages such as faster growth rates, better edge coverage, and more uniform films, making it suitable for high-quality applications. CVD, on the other hand, operates at higher temperatures and relies solely on chemical reactions without the use of plasma. The choice between PECVD and CVD depends on the specific requirements of the application, including temperature sensitivity, film quality, and deposition rate.
Key Points Explained:
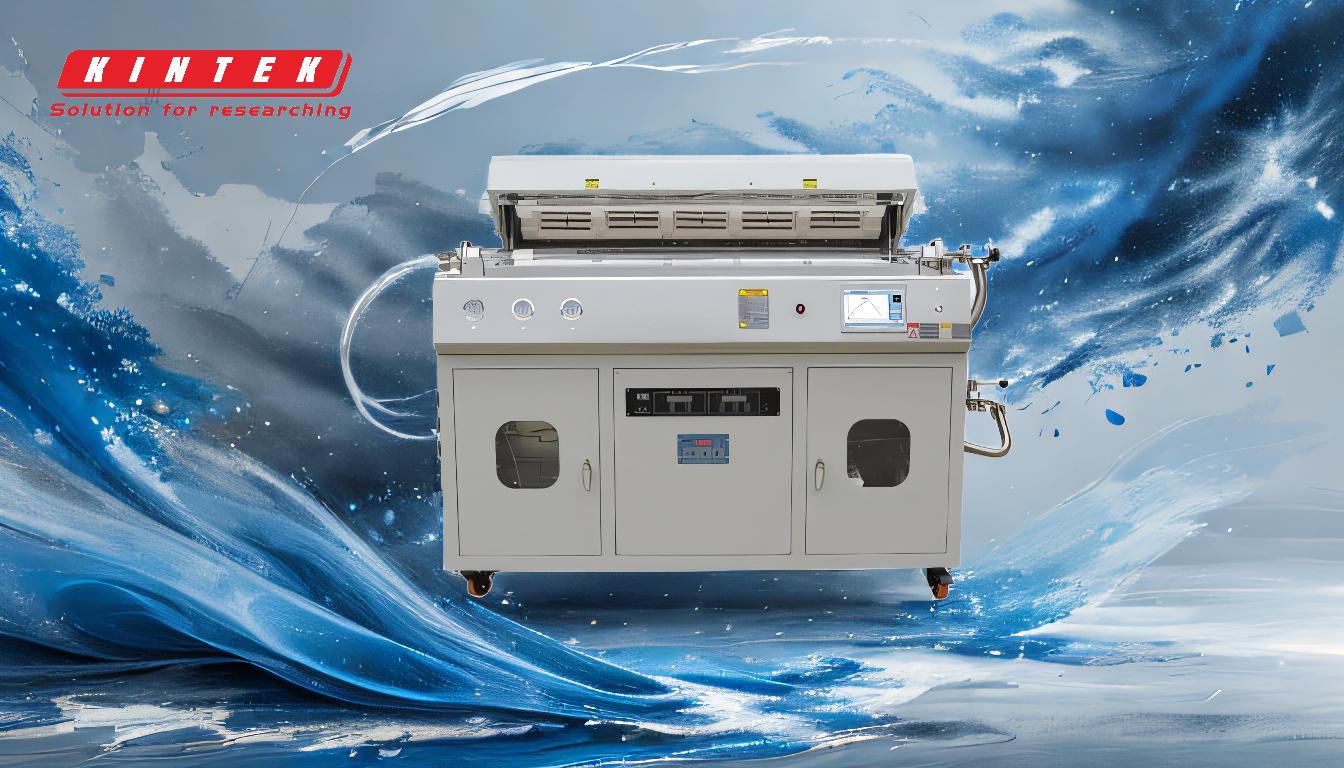
-
Temperature Requirements:
- PECVD: Operates at lower temperatures due to the use of plasma, which provides the necessary activation energy for chemical reactions. This makes PECVD suitable for temperature-sensitive substrates.
- CVD: Requires higher temperatures to initiate and sustain the chemical reactions necessary for deposition. This can limit its use with materials that cannot withstand high temperatures.
-
Deposition Mechanism:
- PECVD: Utilizes plasma to enhance the chemical reactions, allowing for faster deposition rates and better control over film properties. The plasma contains high-energy electrons that facilitate the process at lower temperatures.
- CVD: Relies solely on thermal energy to drive the chemical reactions. The process is typically slower and requires higher temperatures to achieve the same results as PECVD.
-
Film Quality and Uniformity:
- PECVD: Produces more uniform films with better edge coverage. The use of plasma allows for precise control over the deposition process, resulting in high-quality films suitable for demanding applications.
- CVD: While it can produce dense and uniform films, the process is generally slower and may not offer the same level of control over film properties as PECVD.
-
Applications:
- PECVD: Ideal for applications requiring high-quality films at lower temperatures, such as in the semiconductor industry for depositing dielectric layers, passivation layers, and other thin films.
- CVD: Commonly used in applications where high-temperature processing is acceptable, such as in the production of silicon wafers, coatings for cutting tools, and other high-temperature-resistant materials.
-
Reproducibility and Control:
- PECVD: Offers better reproducibility and control over the deposition process due to the use of plasma. This makes it more suitable for high-precision applications where consistency is critical.
- CVD: While it can produce high-quality films, the process may be less reproducible due to the reliance on thermal energy alone. This can lead to variations in film properties, especially in large-scale production.
In summary, PECVD and CVD are both valuable techniques for thin film deposition, but they cater to different needs based on temperature sensitivity, film quality, and application requirements. PECVD's use of plasma allows for lower temperature processing, faster deposition rates, and better film uniformity, making it a preferred choice for many high-quality applications. CVD, with its reliance on higher temperatures, remains a robust method for applications where thermal stability is not a concern.
Summary Table:
Aspect | PECVD | CVD |
---|---|---|
Temperature | Lower temperatures due to plasma activation | Higher temperatures required for thermal reactions |
Deposition Mechanism | Uses plasma for faster, controlled reactions | Relies on thermal energy, slower process |
Film Quality | More uniform films, better edge coverage | Dense and uniform but less controlled |
Applications | Ideal for temperature-sensitive, high-quality films (e.g., semiconductors) | Suitable for high-temperature-resistant materials (e.g., silicon wafers) |
Reproducibility | Better control and reproducibility | Less reproducible due to thermal reliance |
Need help choosing between PECVD and CVD for your application? Contact our experts today!