Physical deposition (PVD) and chemical deposition (CVD) are two distinct methods used to deposit thin films onto substrates, each with unique mechanisms, materials, and applications. PVD relies on physical processes like evaporation, sputtering, or sublimation to transfer material from a solid source to a substrate, while CVD involves chemical reactions of gaseous precursors to form a solid film on the substrate. The key differences lie in the precursor types, reaction mechanisms, process conditions, and the resulting film properties. Understanding these distinctions is crucial for selecting the appropriate method for specific applications.
Key Points Explained:
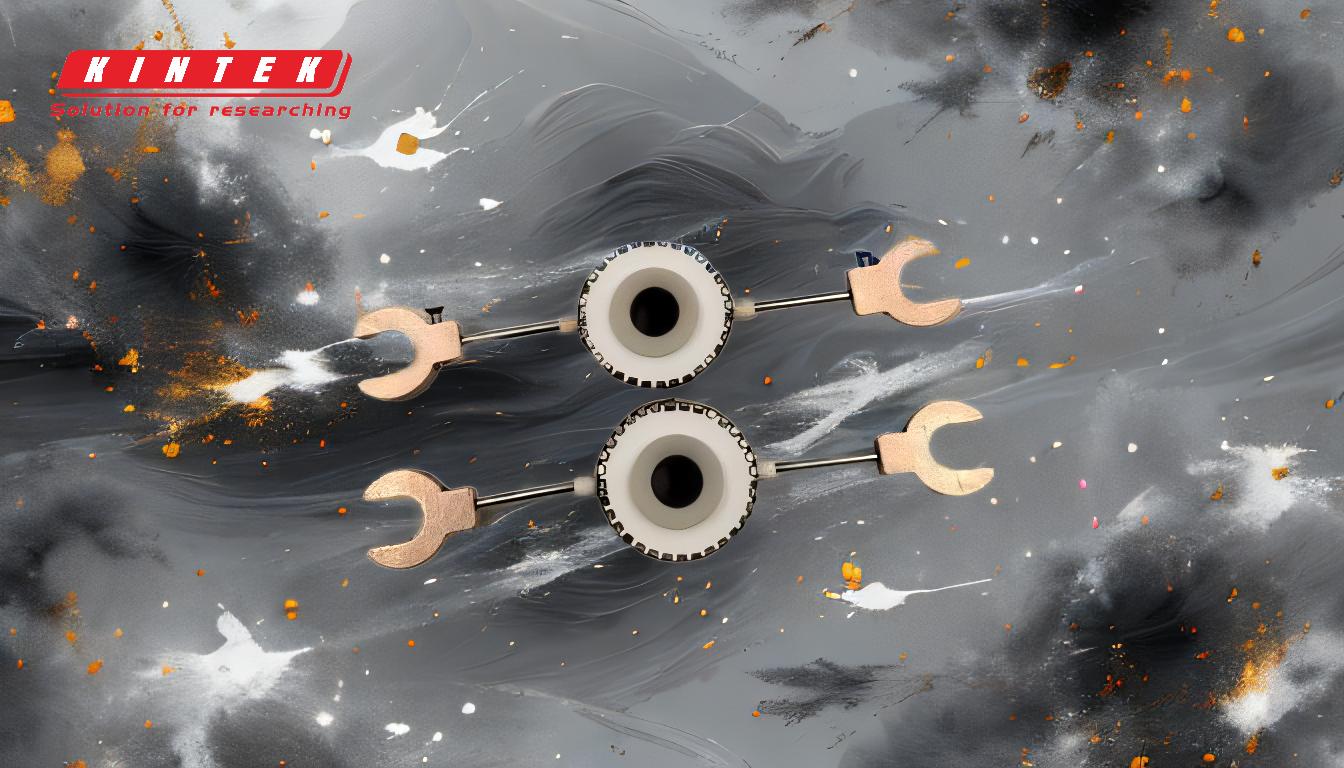
-
Precursor Types:
- PVD: Uses solid materials (targets) that are vaporized through physical means such as heating, sputtering, or laser ablation. The vaporized atoms or molecules then condense on the substrate to form a thin film.
- CVD: Utilizes gaseous precursors that chemically react or decompose on the substrate surface to form the desired film. The chemical reactions are often activated by heat, plasma, or other energy sources.
-
Mechanism of Deposition:
- PVD: Involves physical processes like evaporation, sputtering, or sublimation. The material is transferred from a solid source to the substrate without significant chemical changes. The process is primarily driven by kinetic energy and thermal energy.
- CVD: Relies on chemical reactions, such as decomposition, oxidation, or reduction, occurring on or near the substrate surface. The process is governed by thermodynamics, reaction kinetics, and mass transport.
-
Process Conditions:
- PVD: Typically operates at lower temperatures compared to CVD, as it relies on physical vaporization rather than chemical reactions. The process is often conducted in a vacuum to minimize contamination and enhance control over the deposition.
- CVD: Requires higher temperatures to activate the chemical reactions. The process can be conducted at atmospheric pressure or under vacuum, depending on the specific type of CVD (e.g., low-pressure CVD, plasma-enhanced CVD).
-
Film Properties:
- PVD: Produces films with high purity and excellent adhesion due to the direct transfer of atoms or molecules. However, the films may have limited conformality, making it challenging to coat complex geometries uniformly.
- CVD: Offers superior conformality, allowing for uniform coating of complex shapes and high aspect ratio structures. The films can also exhibit better step coverage and can be tailored for specific properties through the choice of precursors and reaction conditions.
-
Applications:
- PVD: Commonly used for applications requiring high-purity films, such as semiconductor devices, optical coatings, and wear-resistant coatings. It is also favored for its ability to deposit a wide range of materials, including metals, alloys, and ceramics.
- CVD: Widely employed in industries requiring conformal coatings, such as microelectronics, MEMS, and protective coatings. CVD is particularly useful for depositing materials like silicon dioxide, silicon nitride, and various metal oxides.
-
Variants and Techniques:
- PVD: Includes techniques like thermal evaporation, electron beam evaporation, sputtering, and arc vapor deposition. Each method offers unique advantages in terms of deposition rate, material compatibility, and film quality.
- CVD: Encompasses various methods such as atmospheric pressure CVD (APCVD), low-pressure CVD (LPCVD), plasma-enhanced CVD (PECVD), and atomic layer deposition (ALD). These techniques allow for precise control over film thickness, composition, and properties.
In summary, the choice between PVD and CVD depends on the specific requirements of the application, including the desired film properties, substrate geometry, and process conditions. While PVD is ideal for high-purity, simple geometries, CVD excels in conformal coatings and complex structures. Understanding these differences enables better decision-making in thin-film deposition processes.
Summary Table:
Aspect | PVD (Physical Vapor Deposition) | CVD (Chemical Vapor Deposition) |
---|---|---|
Precursor Types | Solid materials (targets) vaporized through physical means (e.g., heating, sputtering). | Gaseous precursors that chemically react or decompose on the substrate. |
Mechanism | Physical processes like evaporation, sputtering, or sublimation. | Chemical reactions (e.g., decomposition, oxidation) on the substrate surface. |
Process Conditions | Lower temperatures, often conducted in a vacuum. | Higher temperatures, can operate at atmospheric pressure or under vacuum. |
Film Properties | High purity, excellent adhesion, limited conformality. | Superior conformality, uniform coating of complex shapes, tailored properties. |
Applications | Semiconductor devices, optical coatings, wear-resistant coatings. | Microelectronics, MEMS, protective coatings, silicon dioxide, silicon nitride, metal oxides. |
Variants/Techniques | Thermal evaporation, electron beam evaporation, sputtering, arc vapor deposition. | APCVD, LPCVD, PECVD, ALD. |
Need help choosing between PVD and CVD for your application? Contact our experts today for tailored solutions!