Physical vapor deposition (PVD) and chemical vapor deposition (CVD) are two widely used techniques for depositing thin films onto substrates, but they differ significantly in their mechanisms, processes, and applications. PVD involves the physical transformation of a solid material into a vapor, which is then deposited onto a substrate, while CVD relies on chemical reactions between gaseous precursors to form a solid film on the substrate. CVD typically operates at higher temperatures and can produce corrosive byproducts, whereas PVD operates at lower temperatures and avoids such issues. Both methods have unique advantages, such as CVD's ability to produce high-purity films and PVD's versatility in deposition techniques.
Key Points Explained:
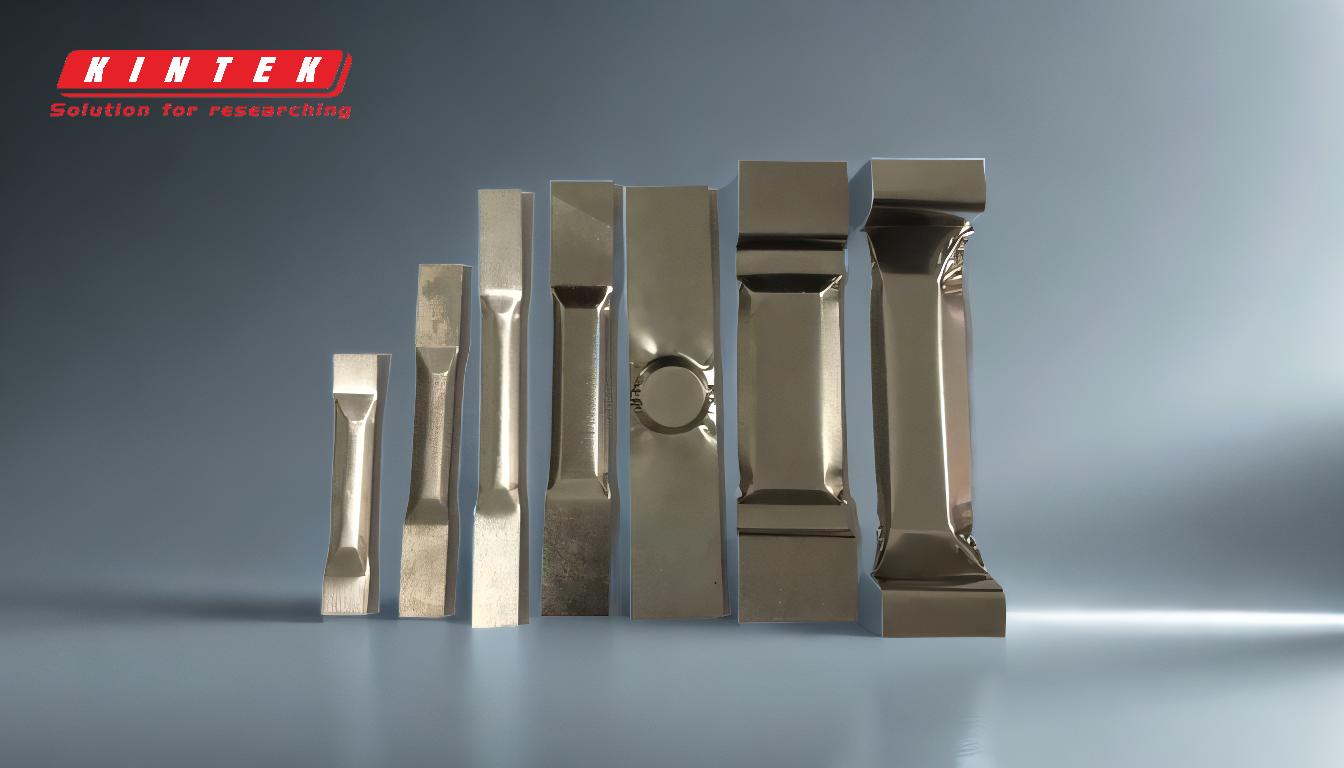
-
Mechanism of Deposition:
- PVD: Involves the physical transformation of a solid material into a vapor through processes like evaporation, sputtering, or sublimation. The vaporized atoms or molecules then condense onto the substrate to form a thin film.
- CVD: Relies on chemical reactions between gaseous precursors. These precursors react or decompose on the substrate surface to form a solid film. The process often involves high temperatures to facilitate the chemical reactions.
-
Temperature Requirements:
- PVD: Typically operates at lower temperatures compared to CVD. This makes PVD suitable for substrates that cannot withstand high temperatures.
- CVD: Generally requires high temperatures, often in the range of 500°C to 1100°C, to activate the chemical reactions necessary for film deposition.
-
Deposition Rates and Efficiency:
- PVD: Deposition rates are generally lower, but techniques like electron beam physical vapor deposition (EBPVD) can achieve high deposition rates (0.1 to 100 μm/min) with high material utilization efficiency.
- CVD: Can achieve high deposition rates, but the process may produce corrosive gaseous byproducts, which can complicate the process and require additional handling.
-
Material Utilization:
- PVD: High material utilization efficiency, especially in techniques like EBPVD, where the material is vaporized and deposited with minimal waste.
- CVD: Material utilization can be less efficient due to the chemical reactions involved, which may produce byproducts that are not part of the final film.
-
Byproducts and Impurities:
- PVD: Does not produce corrosive byproducts, making it a cleaner process in terms of chemical handling.
- CVD: Can produce corrosive gaseous byproducts, which may require additional safety measures and can sometimes leave impurities in the film.
-
Applications:
- PVD: Commonly used in applications requiring high-purity films, such as in the semiconductor industry, optical coatings, and decorative finishes.
- CVD: Often used in applications requiring complex chemical compositions, such as in the production of graphene, carbon nanotubes, and advanced ceramics.
-
Techniques and Variants:
- PVD: Includes techniques like sputtering, evaporation, and sublimation. Each technique has its own advantages and is chosen based on the specific requirements of the application.
- CVD: Includes variants like plasma-enhanced chemical vapor deposition (PECVD), which uses plasma to activate the source gas, allowing for lower processing temperatures and more precise control over film properties.
In summary, while both PVD and CVD are essential techniques for thin film deposition, they differ fundamentally in their mechanisms, temperature requirements, and the types of materials they can deposit. PVD is generally cleaner and operates at lower temperatures, making it suitable for a wide range of substrates, while CVD offers the ability to deposit complex chemical compositions and is often used in high-temperature applications. The choice between PVD and CVD depends on the specific requirements of the application, including the desired film properties, substrate material, and processing conditions.
Summary Table:
Aspect | PVD | CVD |
---|---|---|
Mechanism | Physical transformation of solid into vapor (e.g., sputtering, evaporation). | Chemical reactions between gaseous precursors to form a solid film. |
Temperature | Lower temperatures, suitable for heat-sensitive substrates. | High temperatures (500°C–1100°C), ideal for high-temperature processes. |
Deposition Rate | Generally lower, but EBPVD can achieve high rates (0.1–100 μm/min). | High deposition rates, but may produce corrosive byproducts. |
Material Utilization | High efficiency, minimal waste. | Less efficient due to chemical byproducts. |
Byproducts | No corrosive byproducts, cleaner process. | May produce corrosive byproducts, requiring additional handling. |
Applications | High-purity films (semiconductors, optical coatings, decorative finishes). | Complex chemical compositions (graphene, carbon nanotubes, ceramics). |
Techniques | Sputtering, evaporation, sublimation. | PECVD, plasma-enhanced CVD for lower temperatures and precise control. |
Still unsure which deposition method is right for your application? Contact our experts today for personalized guidance!