Physical Vapor Deposition (PVD) and Chemical Vapor Deposition (CVD) are two widely used techniques for growing thin films, each with distinct processes, mechanisms, and applications. PVD involves the physical transfer of material from a source to a substrate, typically through processes like sputtering or evaporation, and operates at lower temperatures. CVD, on the other hand, relies on chemical reactions between gaseous precursors and the substrate, often requiring high temperatures and resulting in thicker, rougher films. The choice between PVD and CVD depends on factors such as the desired film properties, substrate compatibility, and application requirements.
Key Points Explained:
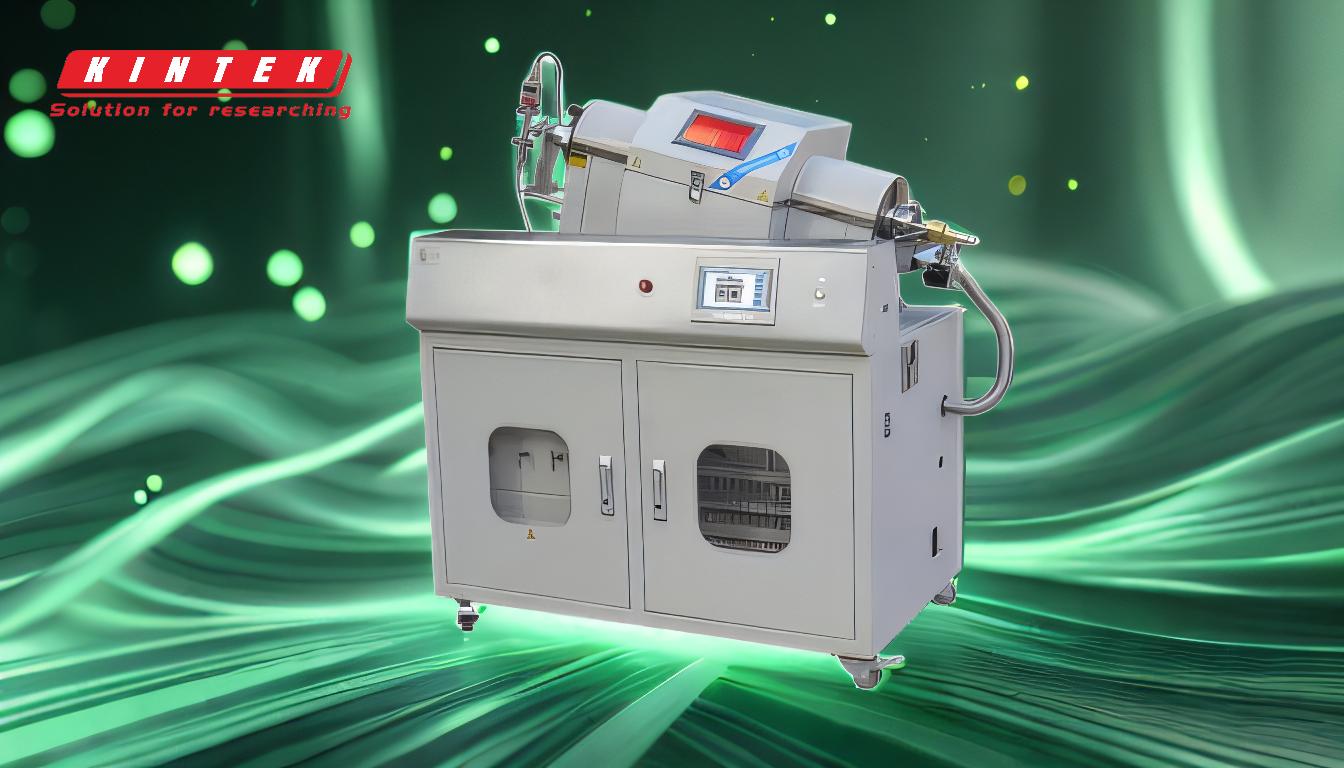
-
Mechanism of Deposition:
- PVD: A physical process where material is vaporized from a solid or liquid source and then deposited onto the substrate. This includes techniques like sputtering and evaporation.
- CVD: A chemical process where gaseous precursors react on the substrate surface, forming a solid film. This involves chemical reactions and often requires high temperatures.
-
Operating Temperatures:
- PVD: Typically operates at lower temperatures, making it suitable for temperature-sensitive substrates.
- CVD: Requires high temperatures (500°–1100°C), which can limit the types of materials and substrates that can be used.
-
Deposition Directionality:
- PVD: A line-of-sight process, meaning deposition occurs directly from the source to the substrate. This can result in uneven coverage on complex geometries.
- CVD: A multidirectional process, allowing for uniform coverage even on complex shapes and high-aspect-ratio structures.
-
Film Characteristics:
- PVD: Produces thin, smooth, and durable coatings with high precision. Films are typically thinner and have better adhesion.
- CVD: Can produce thicker and rougher films, but with excellent conformality and the ability to coat a wide range of materials.
-
Applications:
- PVD: Commonly used for optical coatings, decorative finishes, and wear-resistant coatings. It is also preferred for applications requiring high precision and smoothness.
- CVD: Widely used in semiconductor manufacturing (e.g., polycrystalline silicon films for integrated circuits), as well as for creating coatings with specific electrical, thermal, or mechanical properties.
-
Material Utilization and Efficiency:
- PVD: Generally has lower deposition rates but high material utilization efficiency. Techniques like Electron Beam PVD (EBPVD) can achieve high deposition rates (0.1 to 100 μm/min) with low substrate temperatures.
- CVD: Offers high deposition rates and is highly versatile, but may produce corrosive byproducts and impurities in the film.
-
Advantages and Limitations:
- PVD Advantages: Lower deposition temperatures, no corrosive byproducts, and high-quality, smooth films.
- PVD Limitations: Lower deposition rates and challenges in coating complex geometries uniformly.
- CVD Advantages: Excellent conformality, ability to coat a wide range of materials, and high deposition rates.
- CVD Limitations: High temperatures can limit substrate compatibility, and the process may produce corrosive gases.
In summary, PVD and CVD are complementary techniques, each with unique strengths and limitations. PVD is ideal for applications requiring precise, smooth, and durable coatings at lower temperatures, while CVD excels in creating conformal, high-quality films on a variety of materials, albeit at higher temperatures. The choice between the two depends on the specific requirements of the application, including the desired film properties, substrate material, and operational constraints.
Summary Table:
Aspect | PVD | CVD |
---|---|---|
Mechanism | Physical transfer of material (e.g., sputtering, evaporation). | Chemical reactions between gaseous precursors and substrate. |
Temperature | Lower temperatures, suitable for sensitive substrates. | High temperatures (500°–1100°C), limiting substrate compatibility. |
Directionality | Line-of-sight process, uneven on complex geometries. | Multidirectional, uniform on complex shapes. |
Film Characteristics | Thin, smooth, durable coatings with high precision. | Thicker, rougher films with excellent conformality. |
Applications | Optical coatings, decorative finishes, wear-resistant coatings. | Semiconductor manufacturing, coatings with specific properties. |
Material Efficiency | Lower deposition rates, high material utilization. | High deposition rates, versatile but may produce corrosive byproducts. |
Advantages | Lower temperatures, no corrosive byproducts, smooth films. | Excellent conformality, wide material compatibility, high deposition rates. |
Limitations | Lower deposition rates, challenges with complex geometries. | High temperatures, corrosive gases, and impurities in films. |
Need help choosing between PVD and CVD for your application? Contact our experts today!